Departments
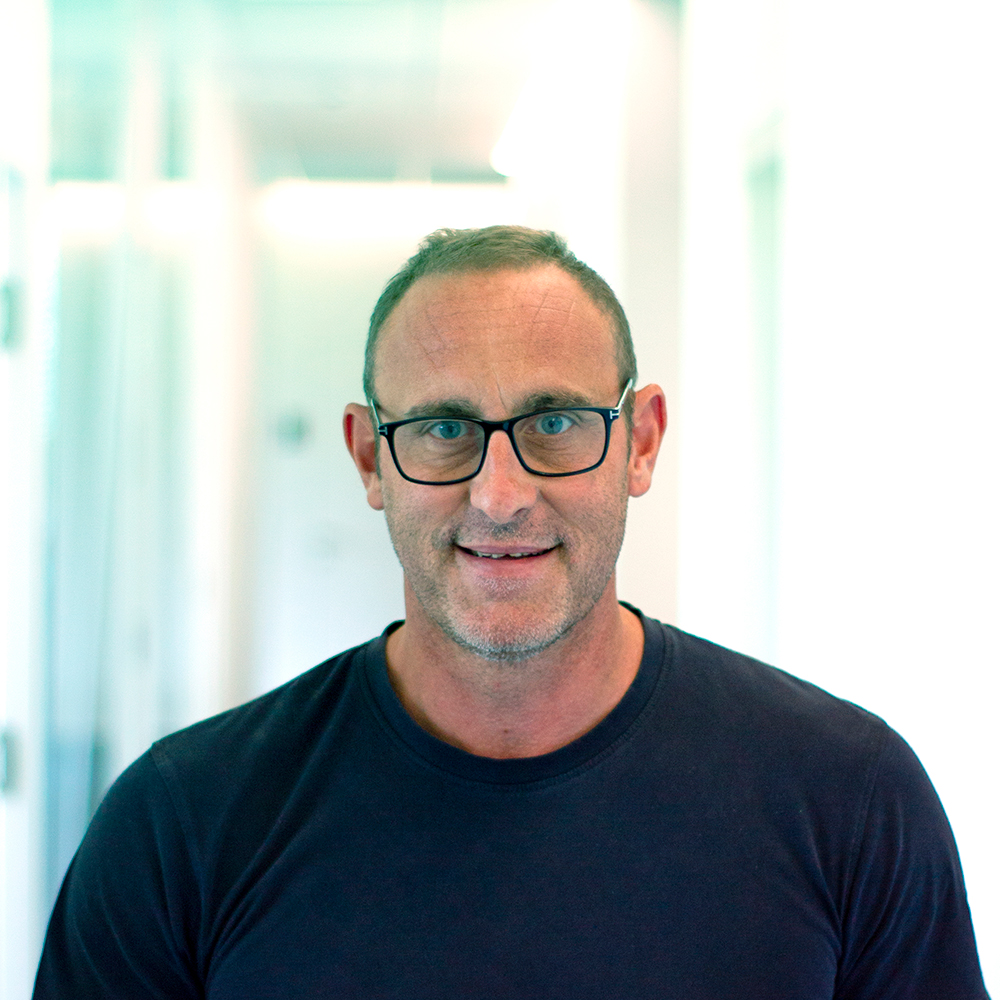
Georg Dick
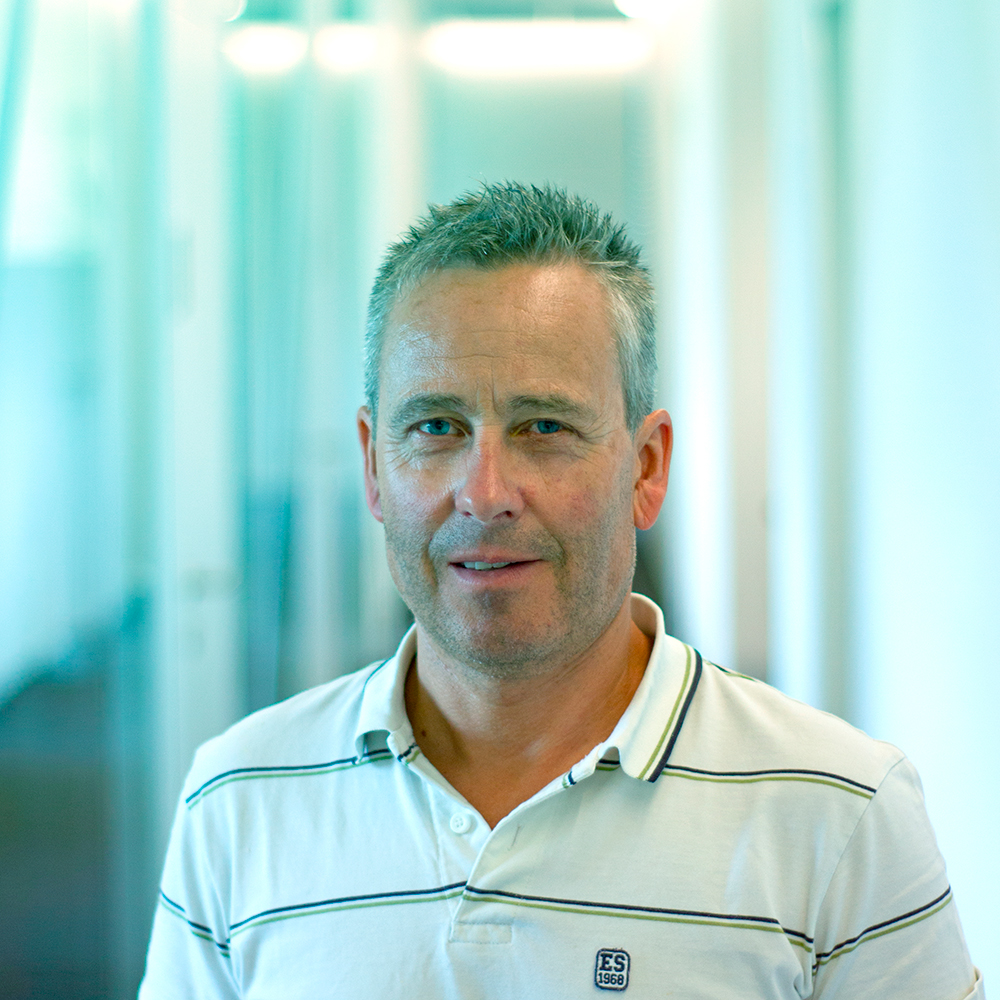
Helmut Zaller
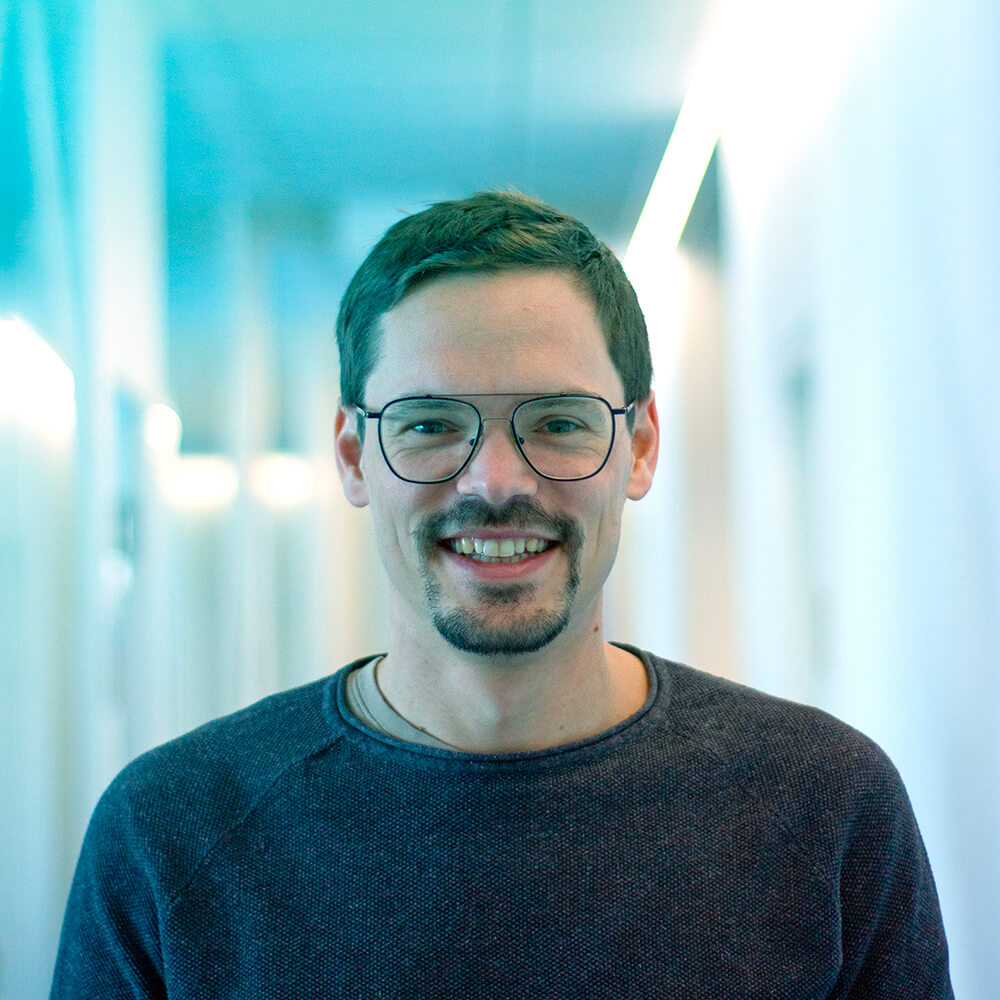
Riedl Tristan
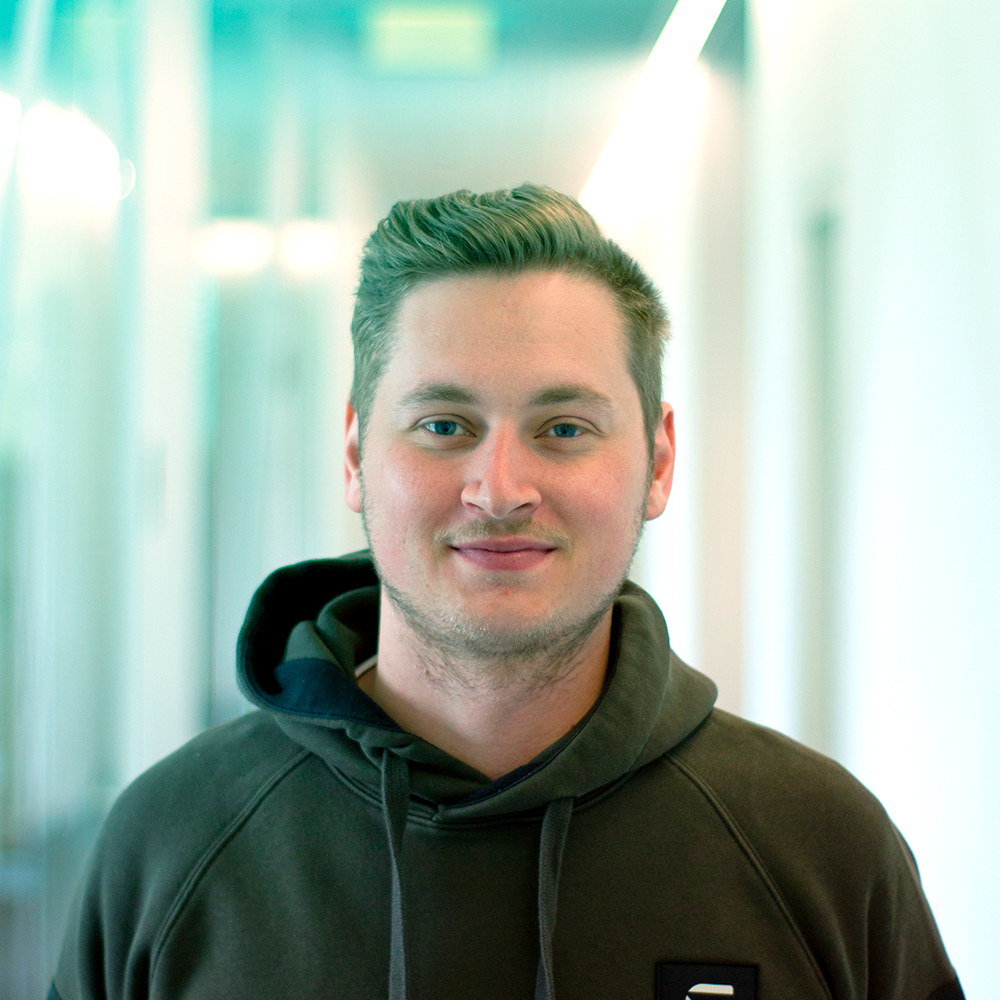
Berger Daniel NEU
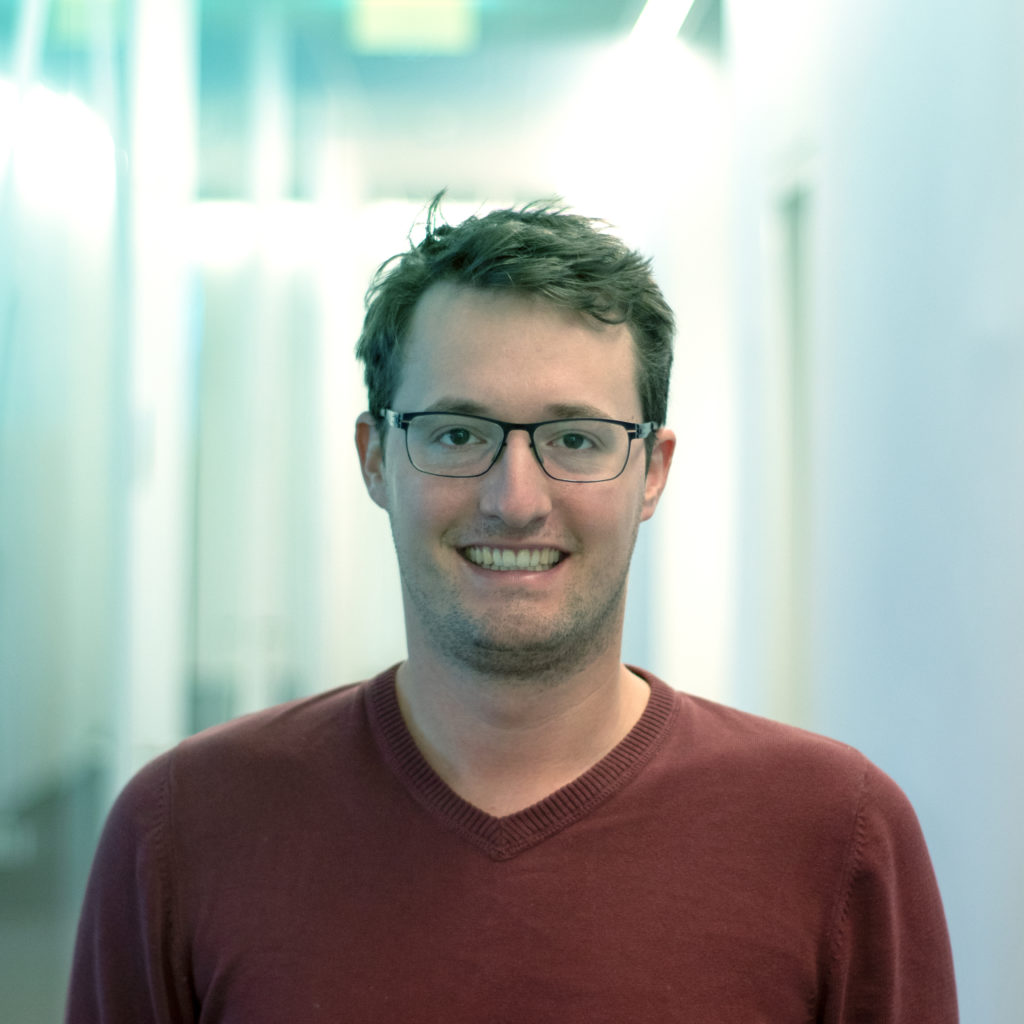
Markus Rossmann
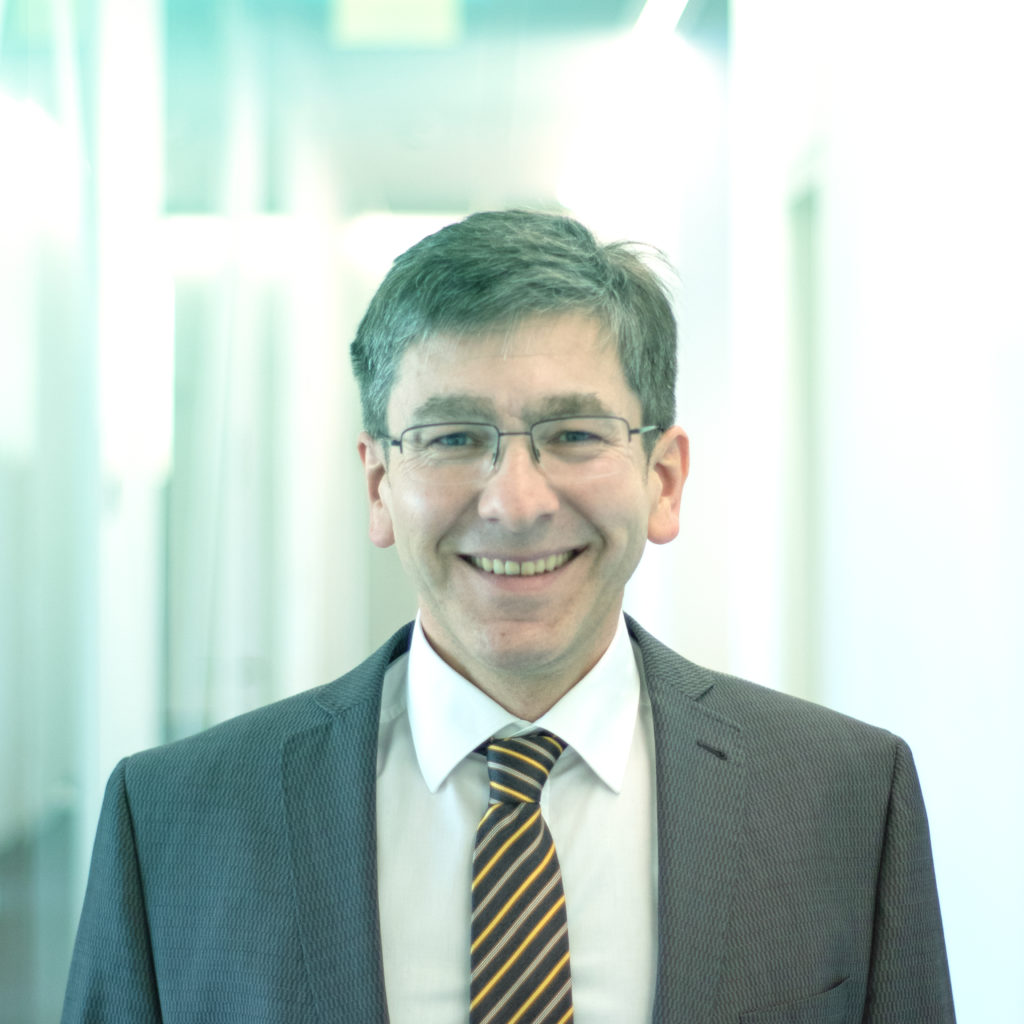
Rupert Schoenauer Neu
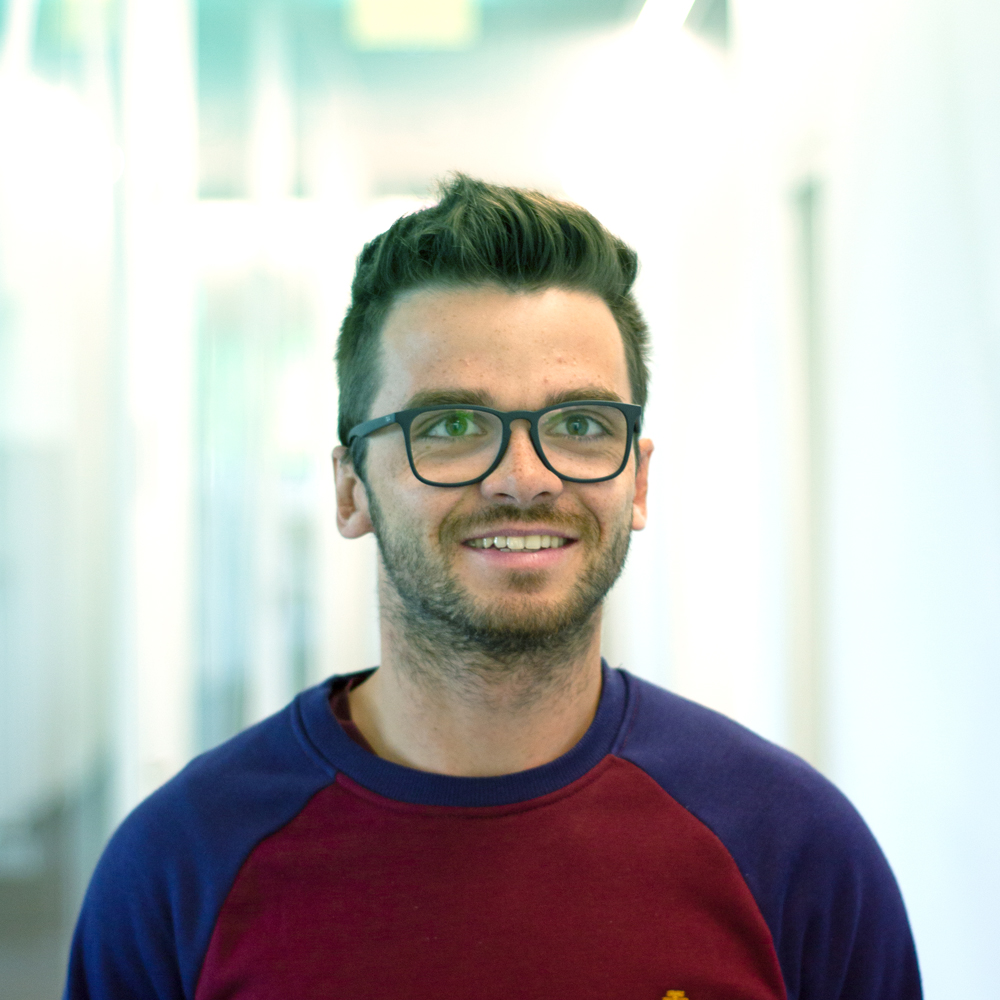
Buchegger Michael

Stefanie_Schnegg_NEU
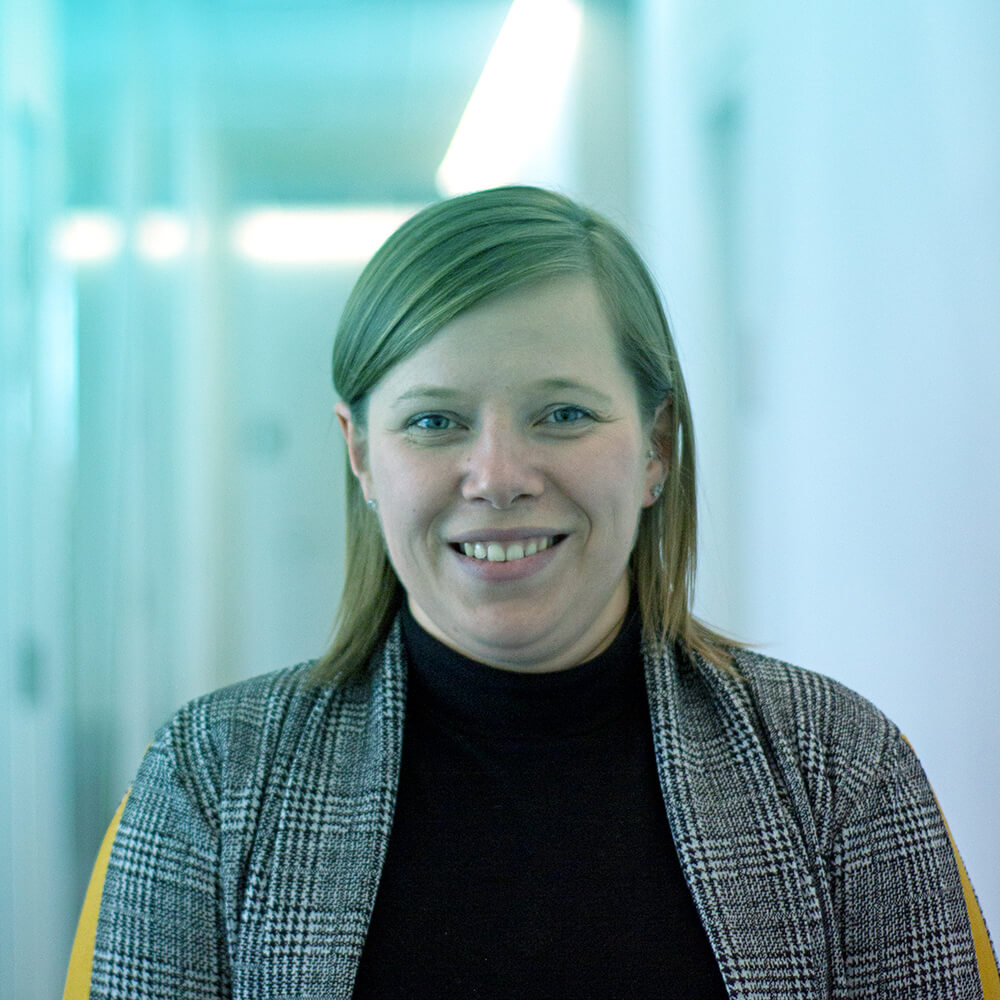
Lechner Susanna
Description:
This department is responsible for recording the dental milling service orders. After the orders have been checked for completeness by the order portal, they are entered into Navision and given to the responsible department (HSC / HL). They are also responsible for the production technology orders. After consultation with the support, orders are entered in the Navision, scanner offers are written and commissioned, delivery notes are created and invoices are issued. Activities such as the creation of waybills for delivery and collection or the registration of new customers also fall within their area of responsibility.

Stefanie_Schnegg_NEU
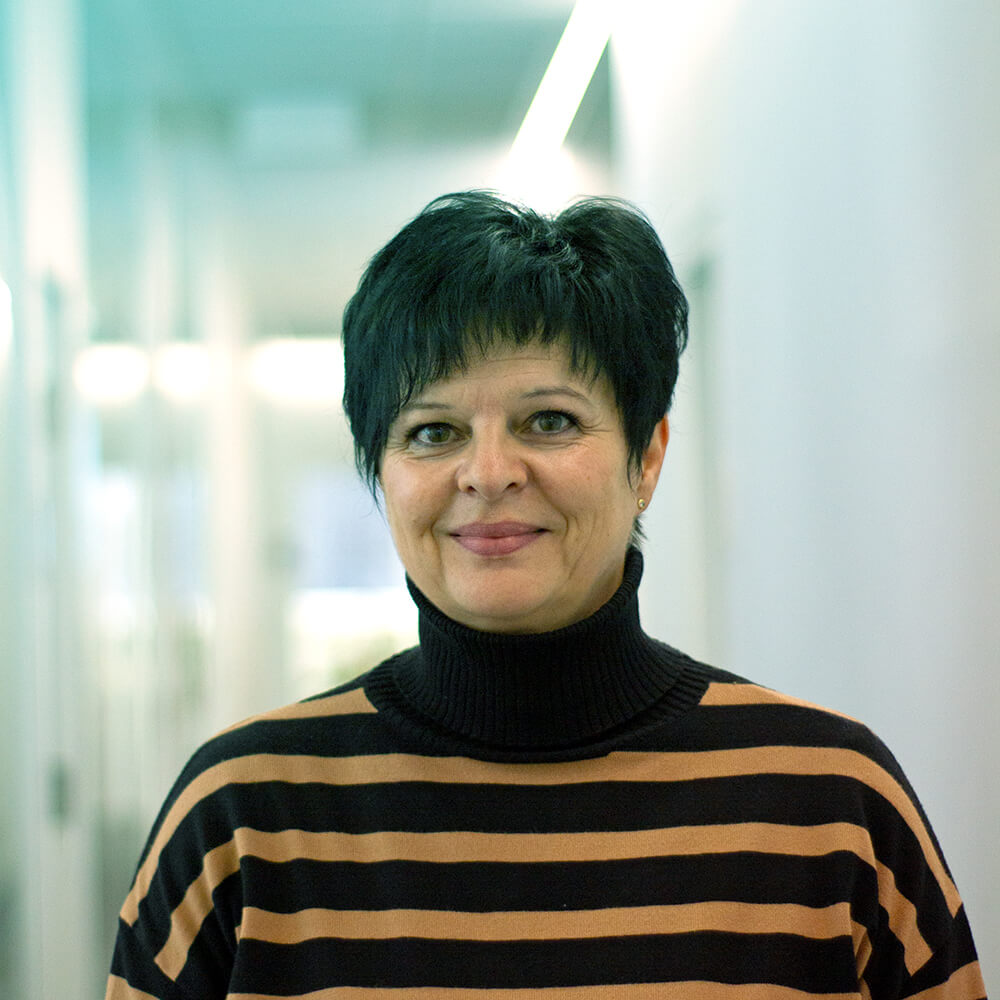
Sandra Huber
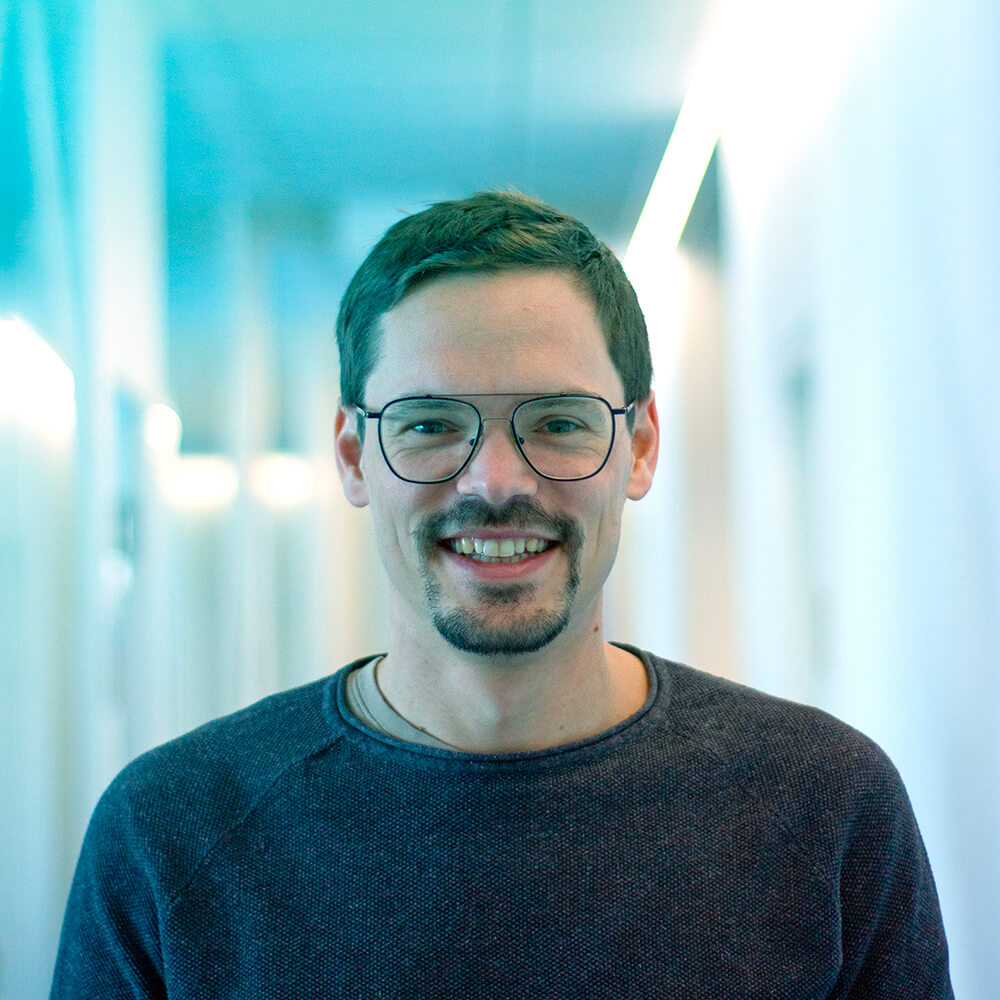
Riedl Tristan
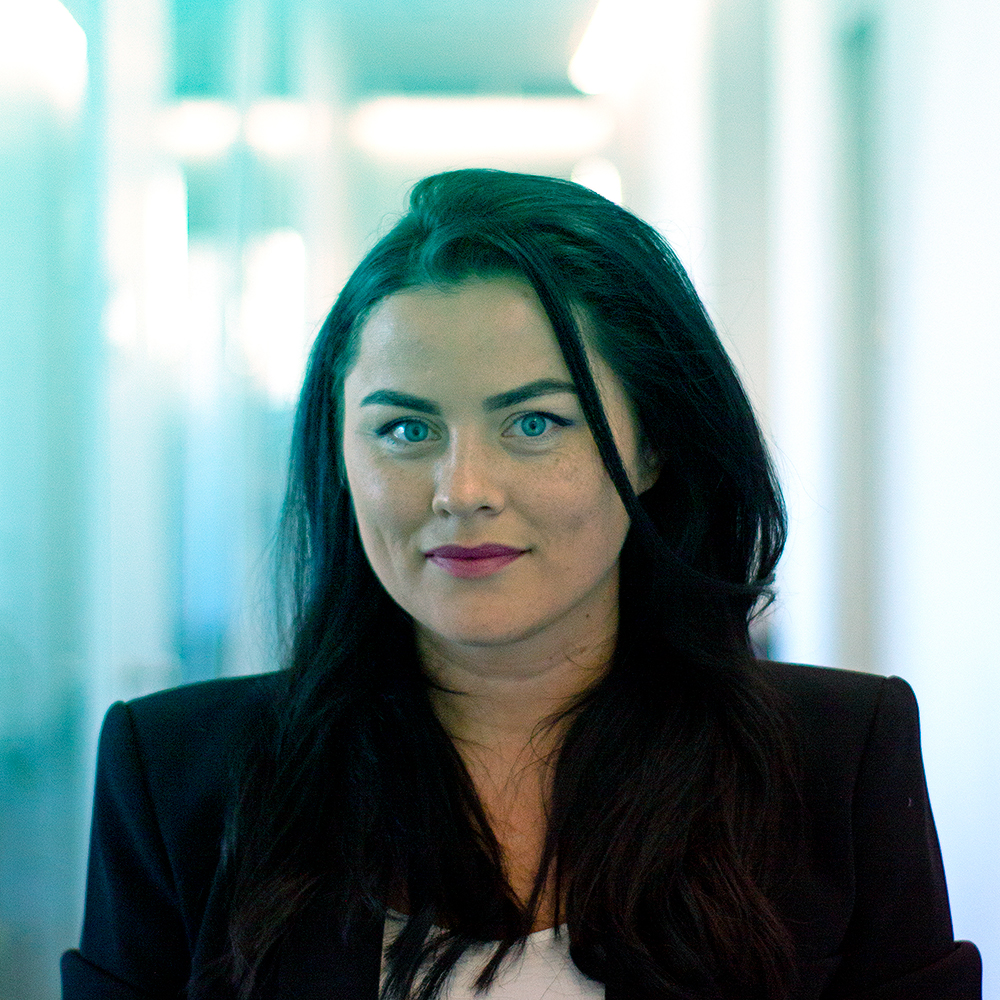
Senida_Demir
Description:
In order to ensure that as many parts as possible that are available for daily work both in the CADstar and in the DDT, the purchasing department organizes all orders from the suppliers. With the support of Microsoft Navision, we try to keep stocks as low as possible, but as high as necessary. In addition, the purchasing department is responsible for price negotiations, incoming goods and the storage and issue of individual items, but also for the search for new suppliers.
Description:
CADstar is certified in accordance with ISO13485 and Directive 93/42 / EEC (for the manufacture of medical products). This ensures that the quality and the company’s internal processes remain uniform and the same. Once a year, the CADstar is monitored by the DQS company in the course of an audit. This is to ensure that no inferior products are used by the end customer, which could subsequently lead to injuries or worse consequences. The QM department is responsible for the complete traceability of the materials but also for the company’s internal documentation and evidence.
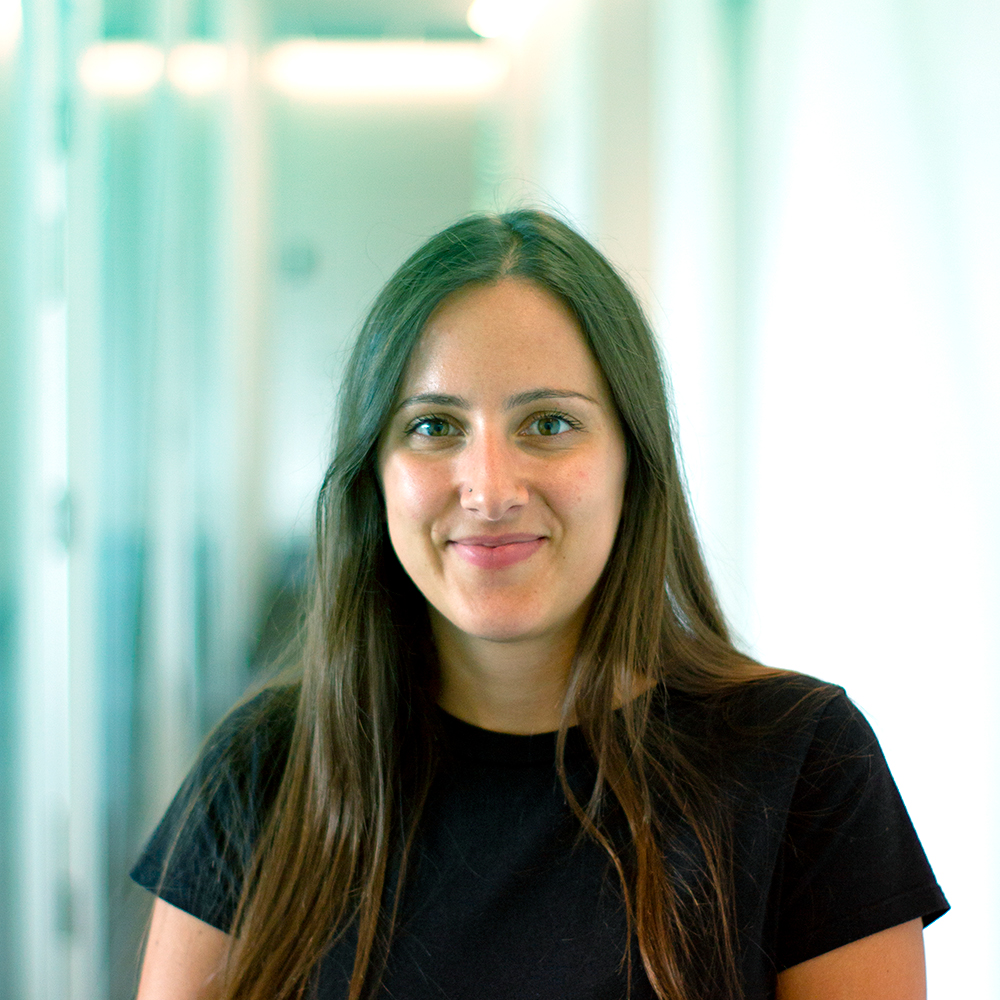
Morgane_Eisl
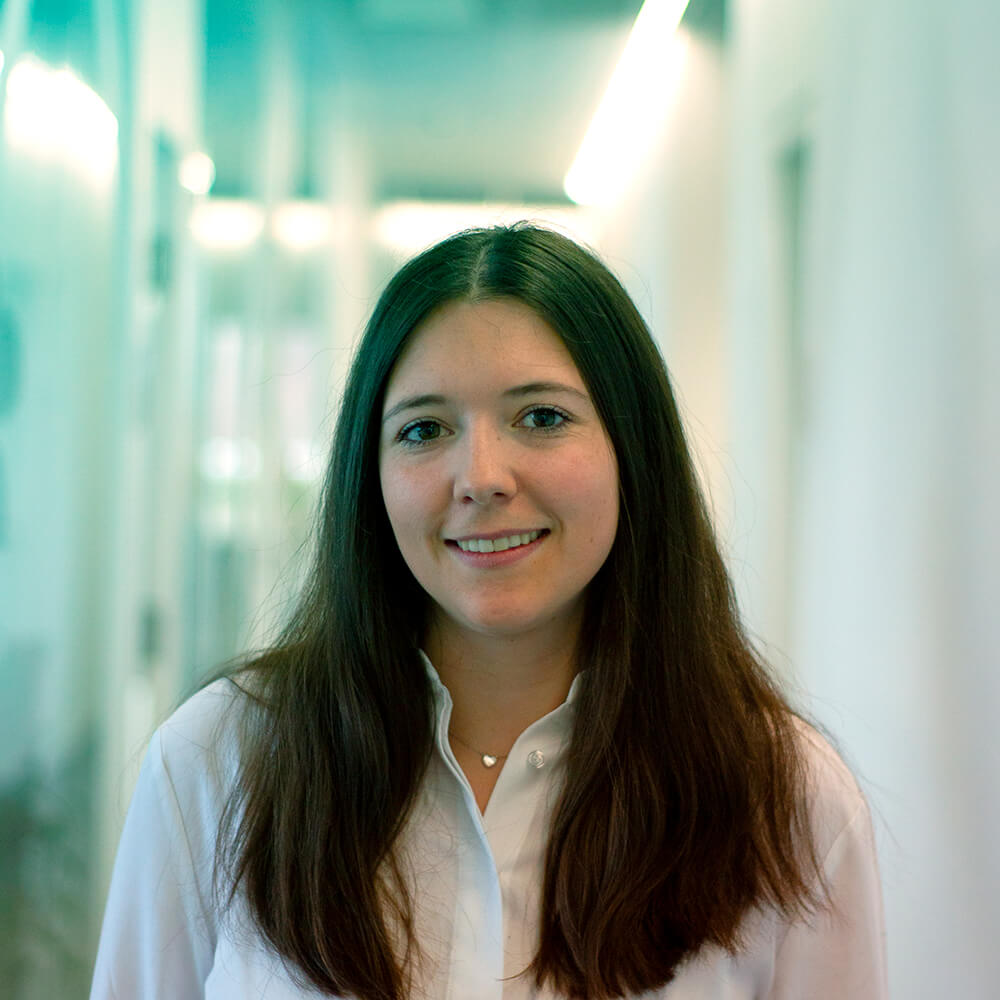
Promberger-Laura
Description:
Our daily routine consists of handling all financial matters of the 6 internal companies and the 2 external companies. Furthermore, we are responsible for the transfers and booking of all business transactions (invoices, payments, etc.) and are the contact persons for our customers, tax consultants, etc.
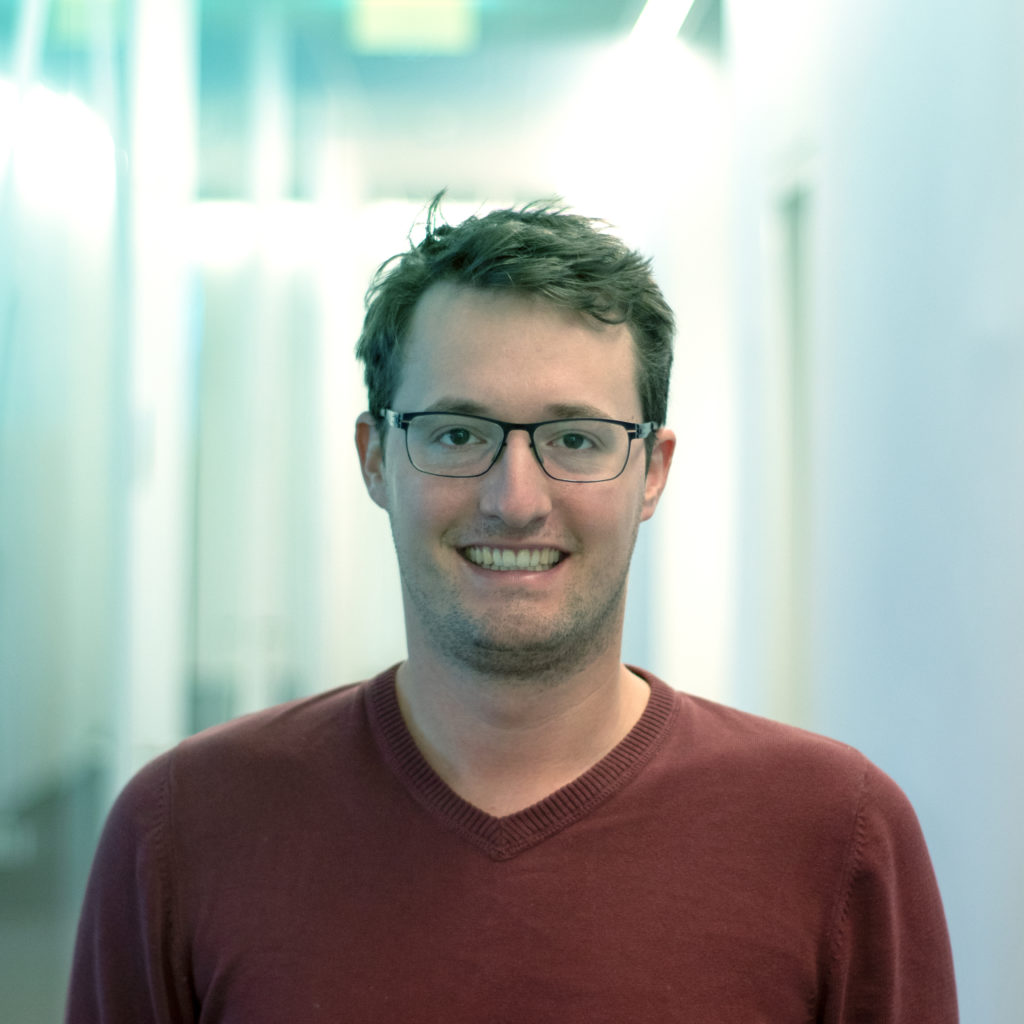
Markus Rossmann
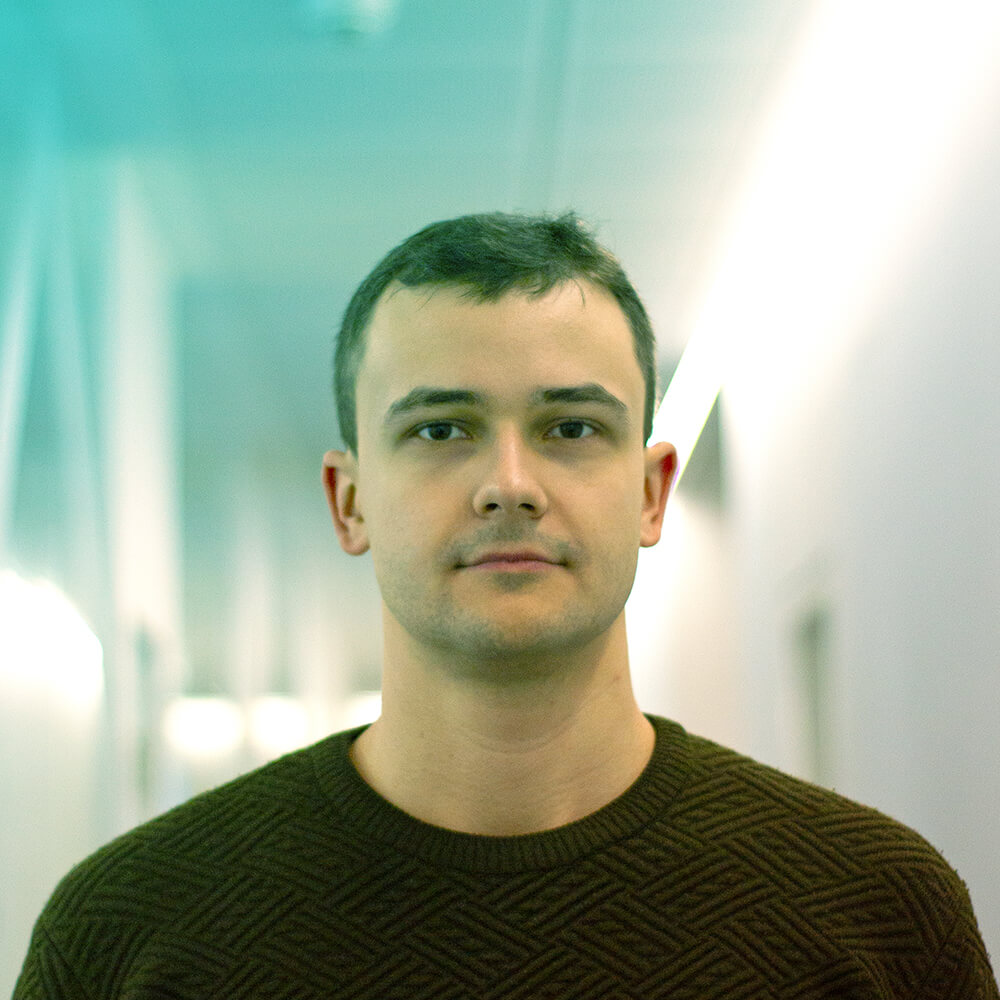
Petronaitis_Andrius
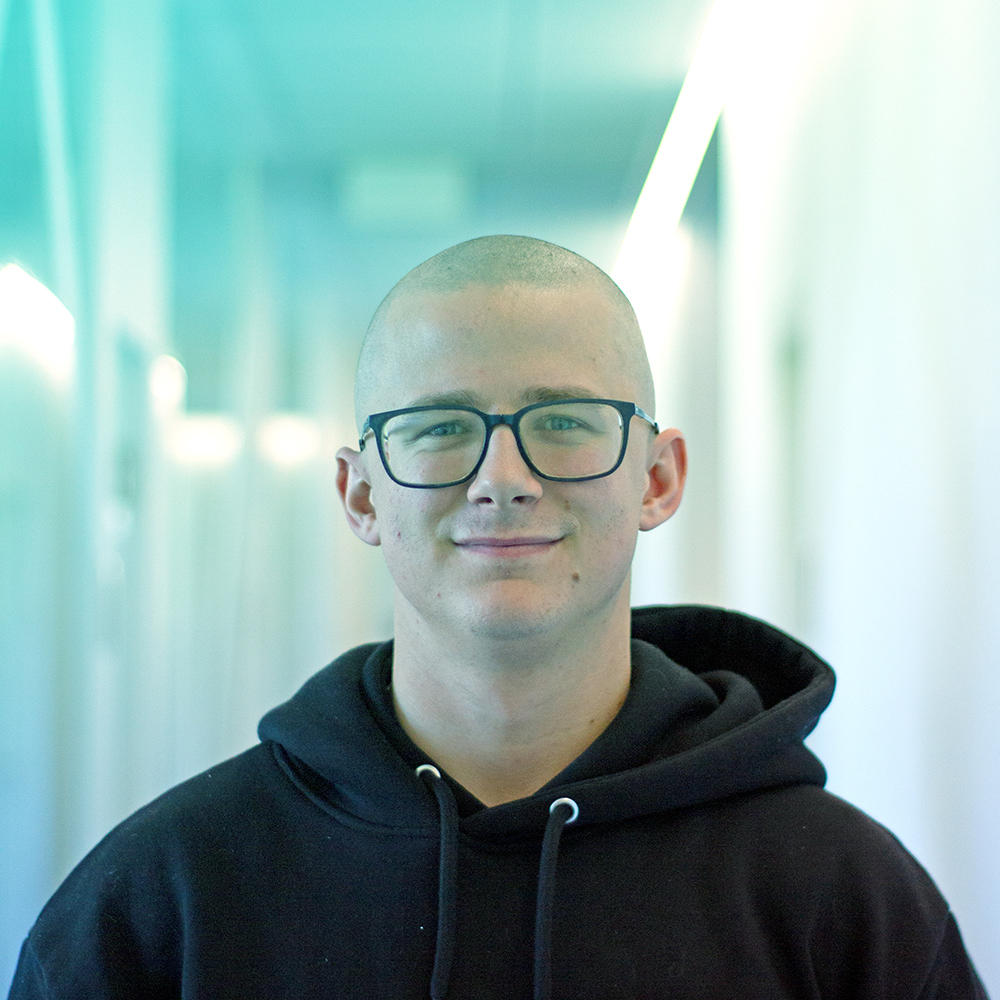
Kainz-Sebastian
Description:
The hardware department is responsible for the development of the scanner hardware and everything that has to do with electricity in the scanner. You take care of new ideas for the future as well as ongoing production. The main task is to develop new circuit boards. The second major area is the technical assessment and design of electrical actuators and the consultation with suppliers. Standards and the measurement and validation of electrical devices are also part of the area of responsibility. The devices are then checked in external EMC laboratories (electromagnetic compatibility).
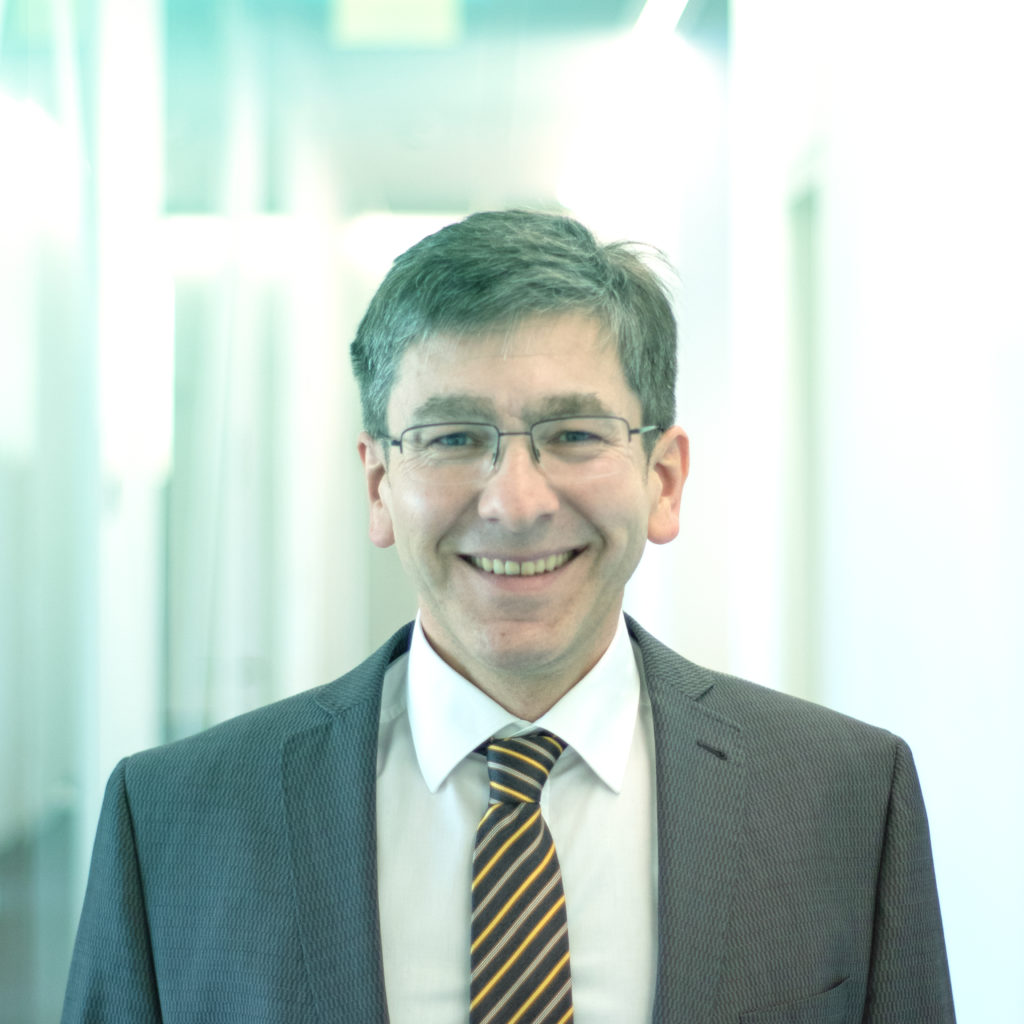
Rupert Schoenauer Neu
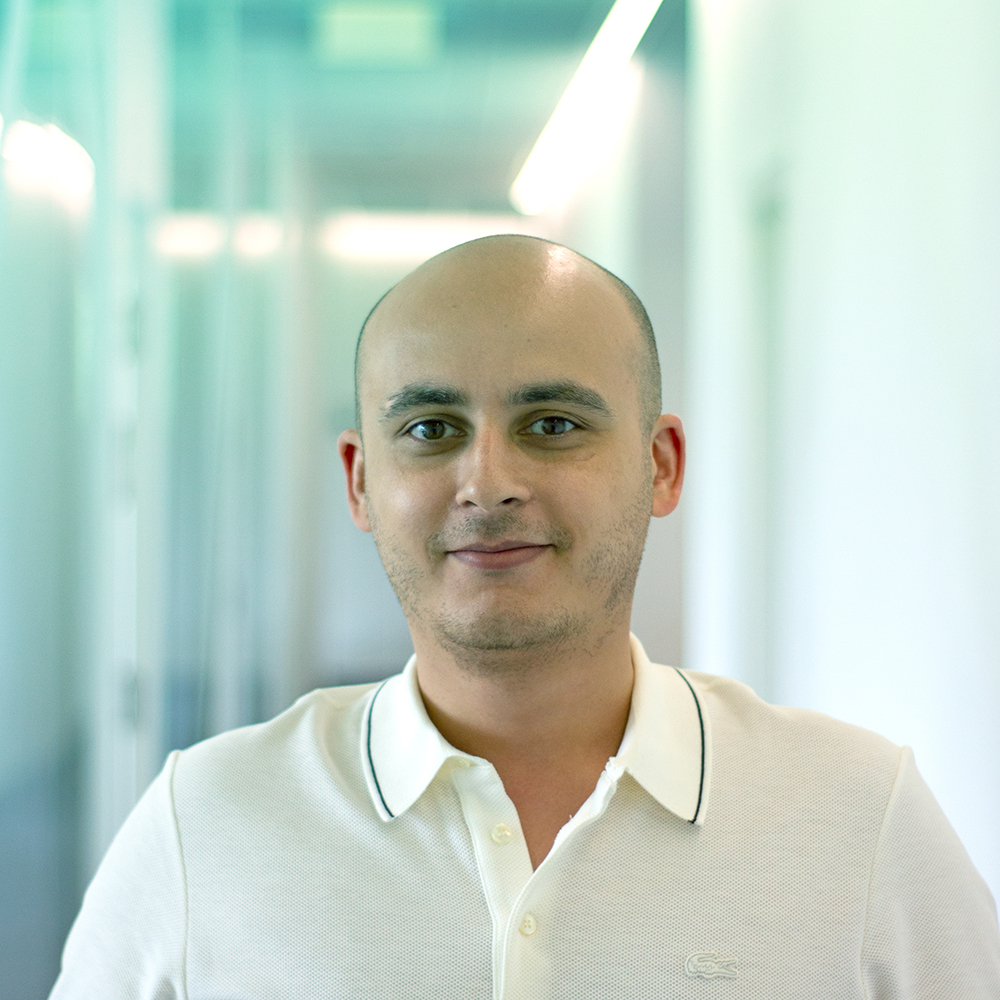
Naghizadeh Mohammad
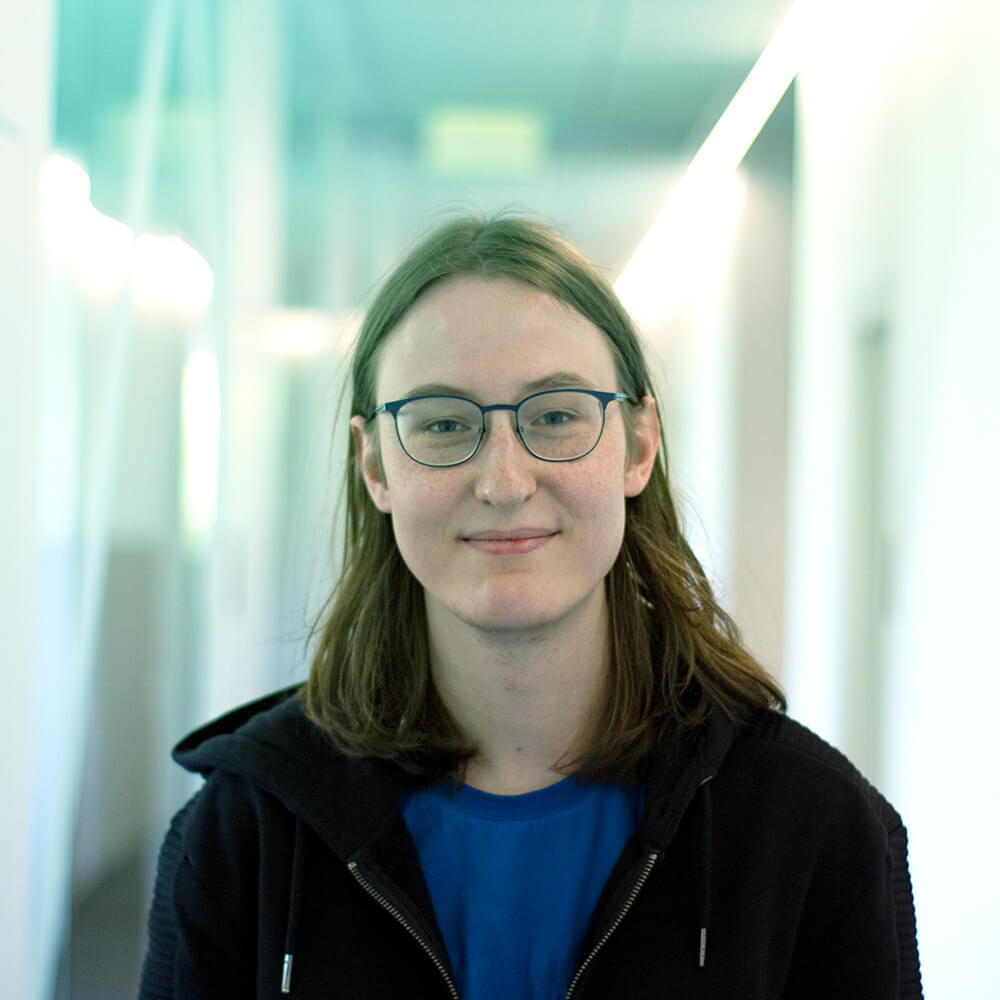
Michael_Wechner
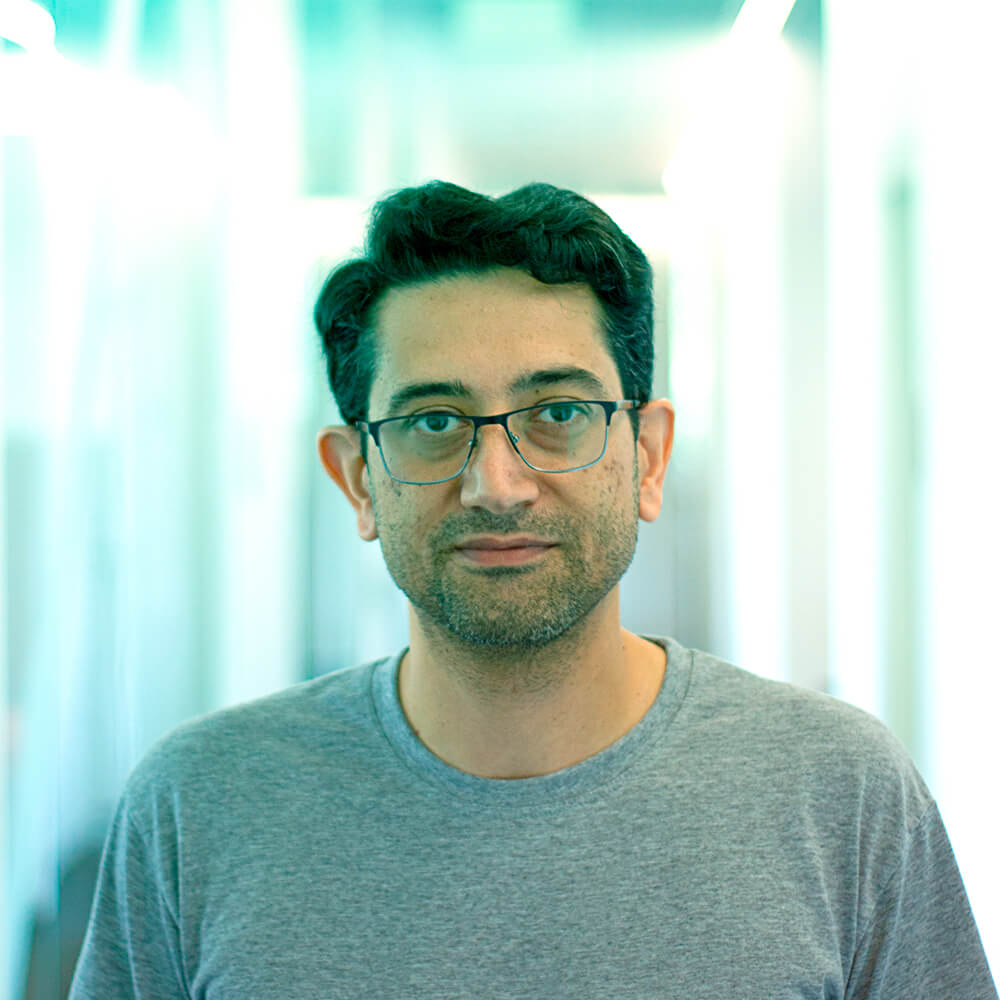
Moez_Mahyar_Ahmadi
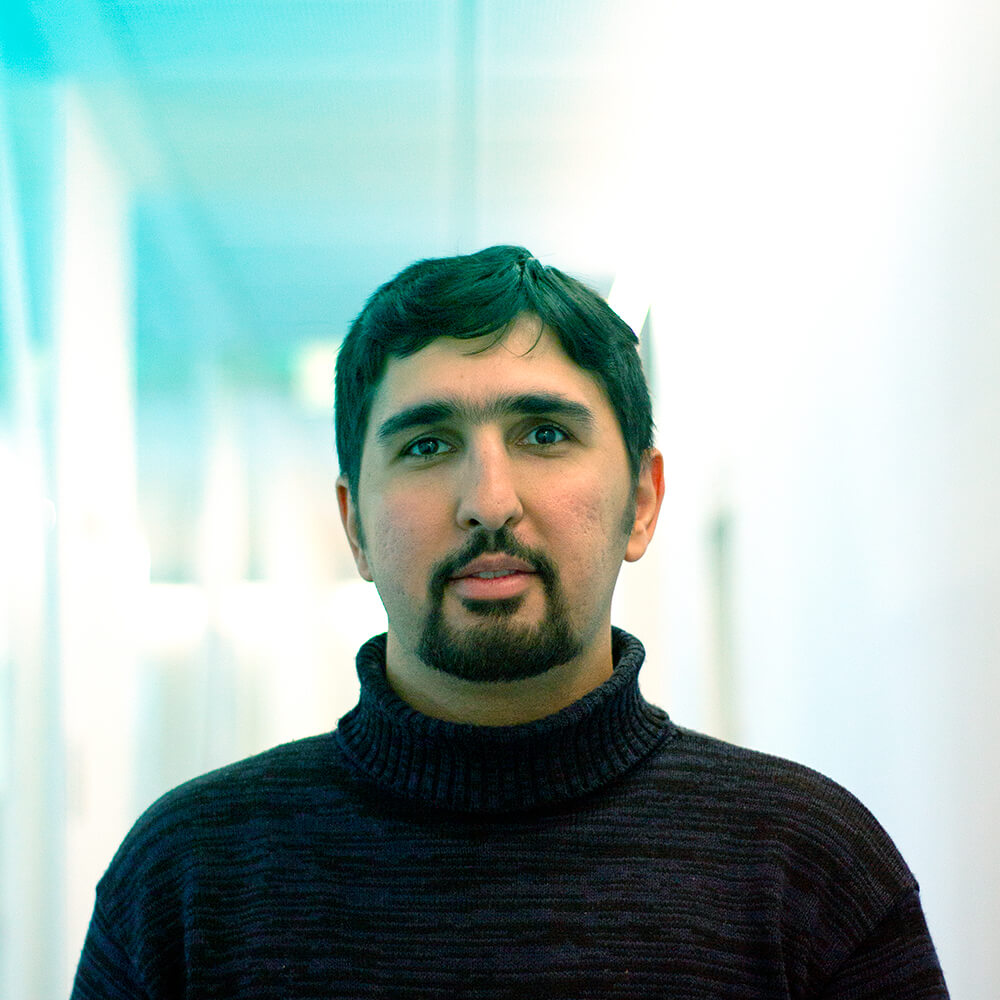
Masoud-Ghasemi-Dehkordi
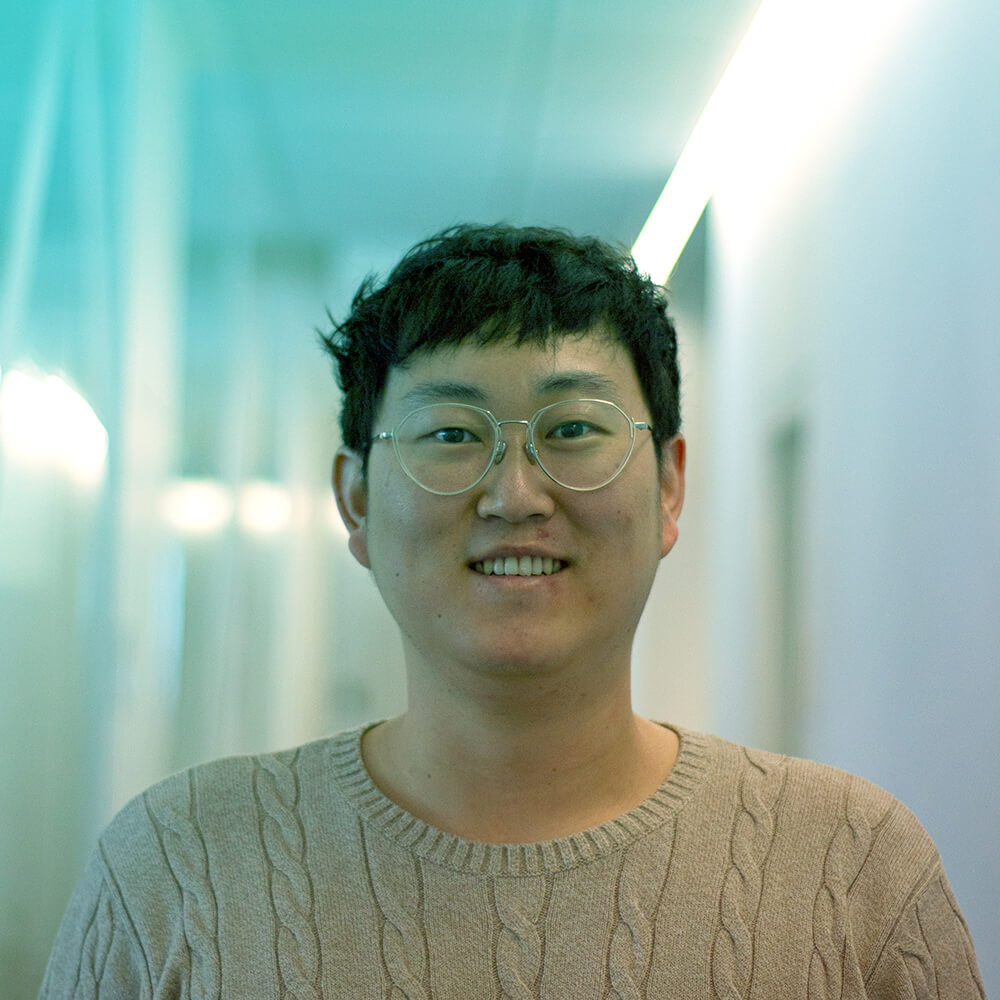
Wang_Zexian
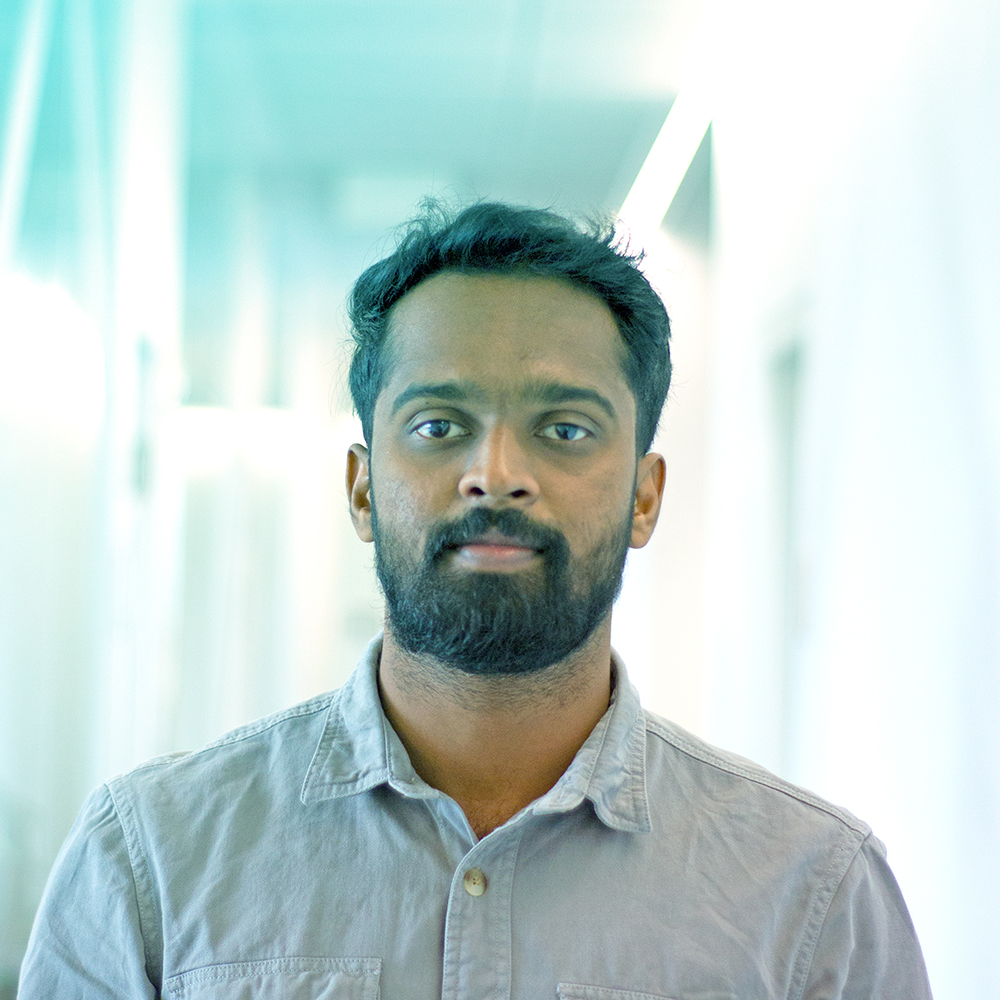
Anandhu-Pallikkudi
Description:
The software development team is responsible for developing all of the scanner software and is constantly working to improve the existing software to make it one of the most robust and reliable scanner software on the market. Software development, maintenance and updating are the core aspect of this team. The team follows the agile working methodology and organizes daily meetings to decide on individual responsibilities and update current tasks. Every task or problem that the team takes on is first thoroughly investigated and, if necessary, discussed with all associated departments. Once the task has been defined, a complete design, development, and integration roadmap is formally outlined. Once the implementation is done, you define the test case to run tests on the first level. Finally, the implementation is reviewed by at least one of the colleagues before it is ready for final publication. In addition to the new development tasks, the team also works closely with the support team to fix software bugs reported by customers and to fix any other bugs found on the company’s premises. In parallel, the team is working on the future implementation of new scanners to achieve better, faster and more reliable results.
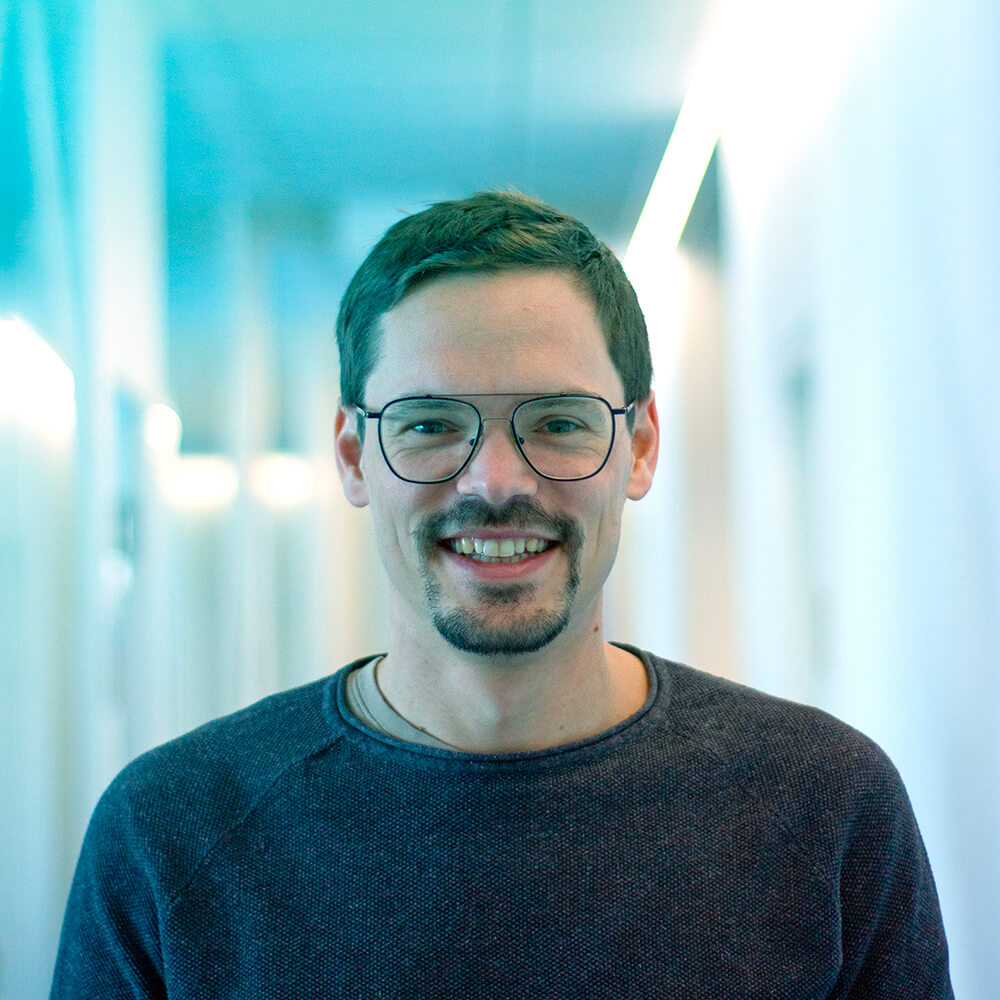
Riedl_Tristan
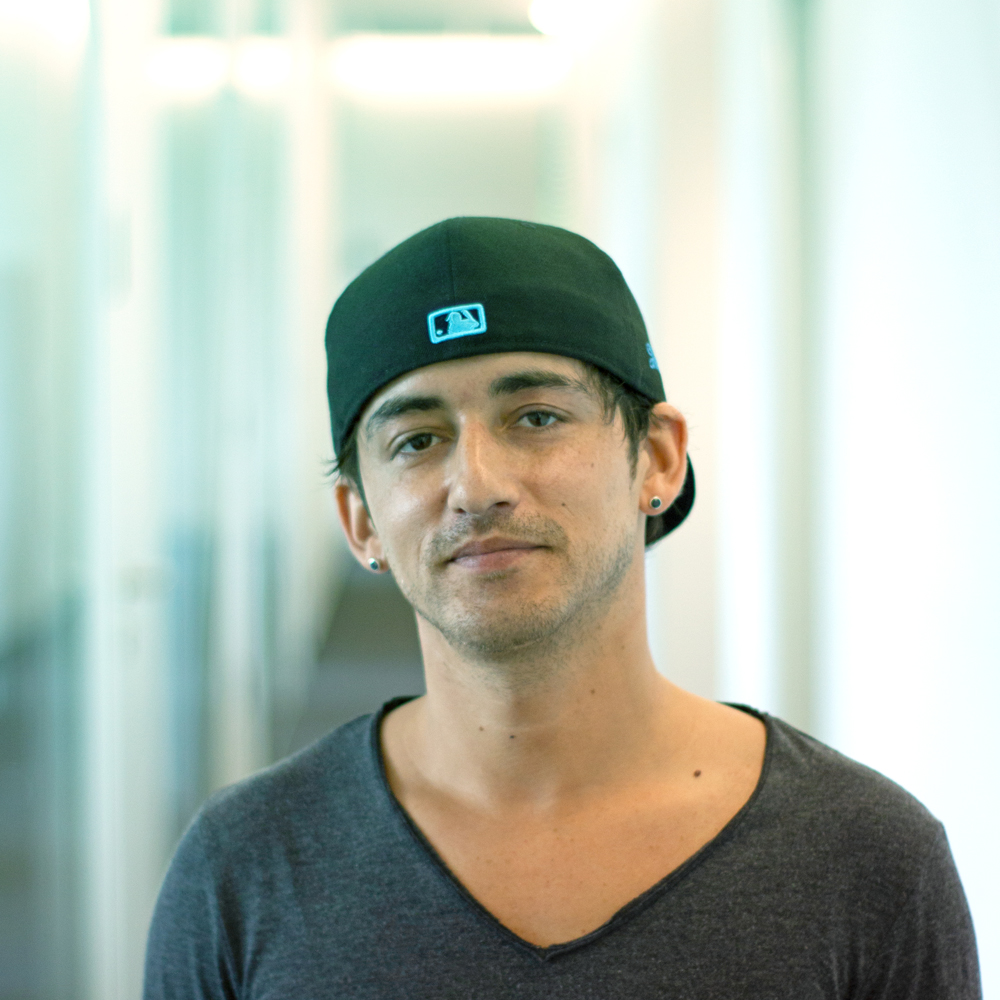
Cadari Jeton
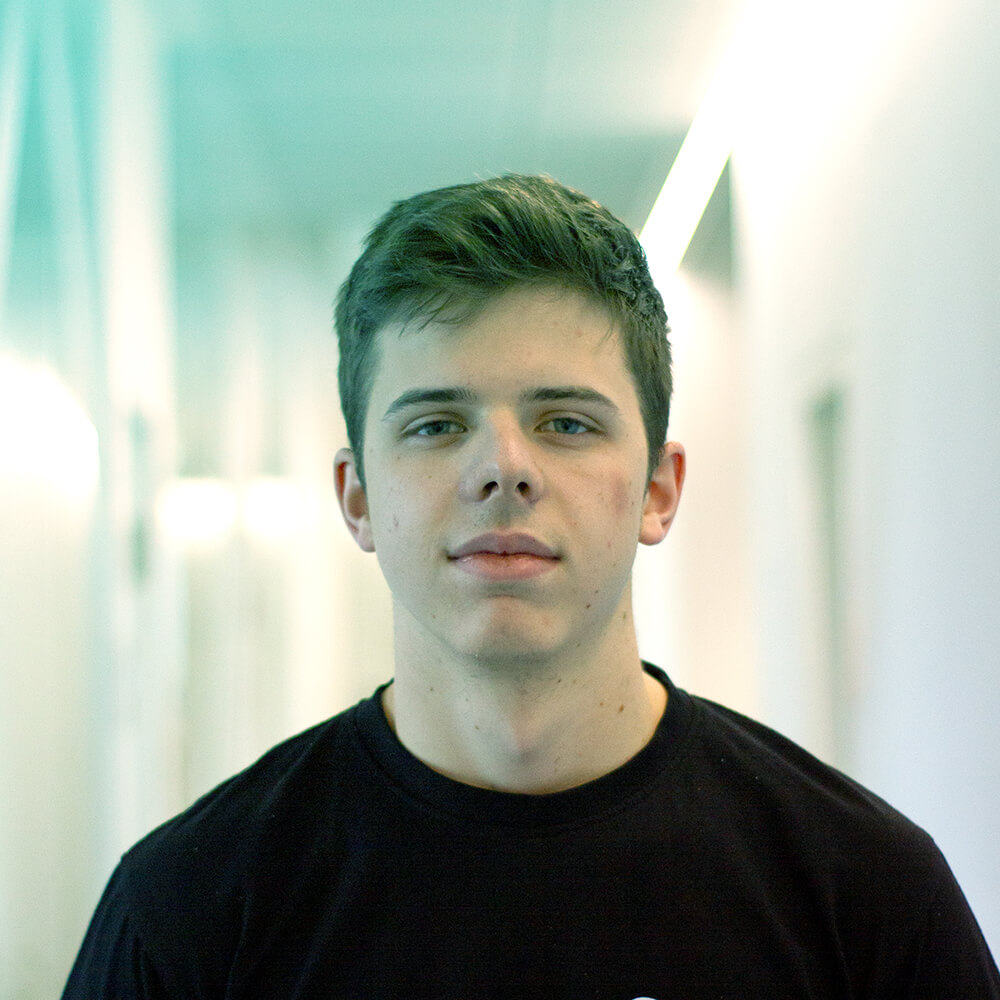
Eberl-Fabian
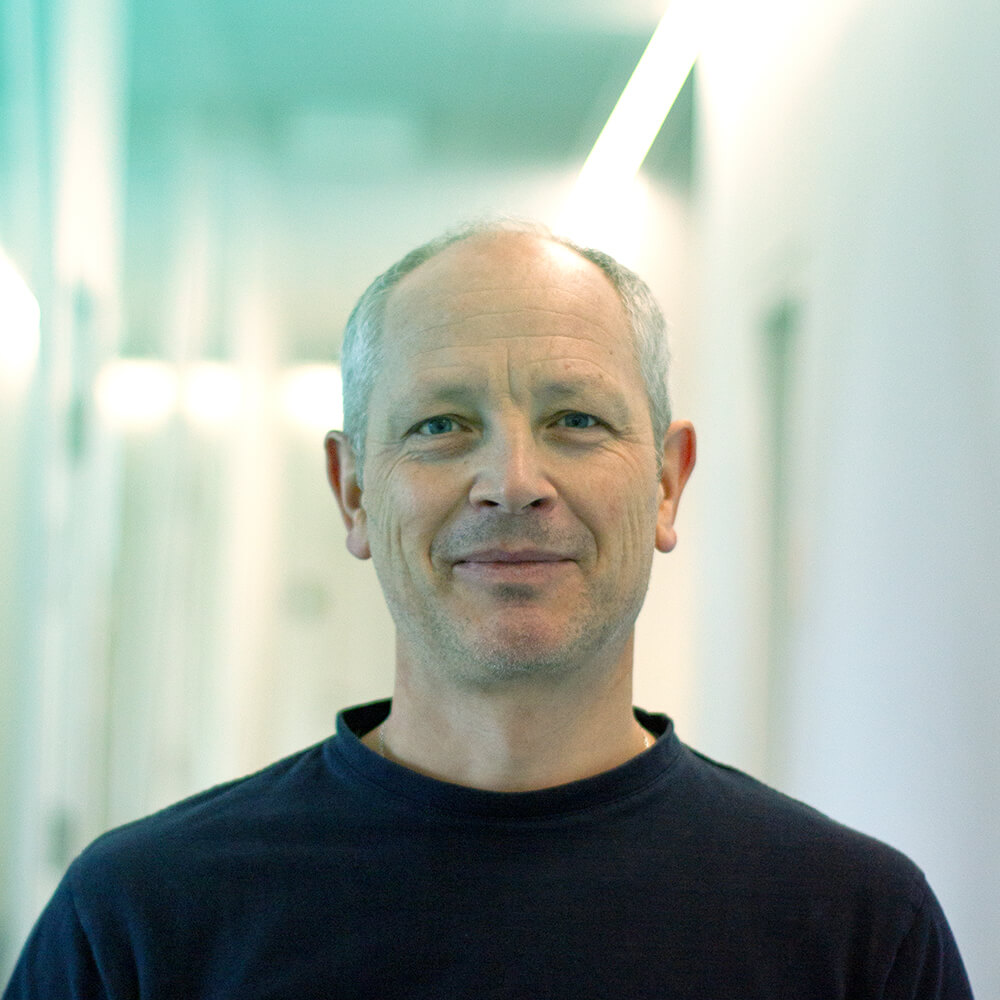
Hafner-Karl
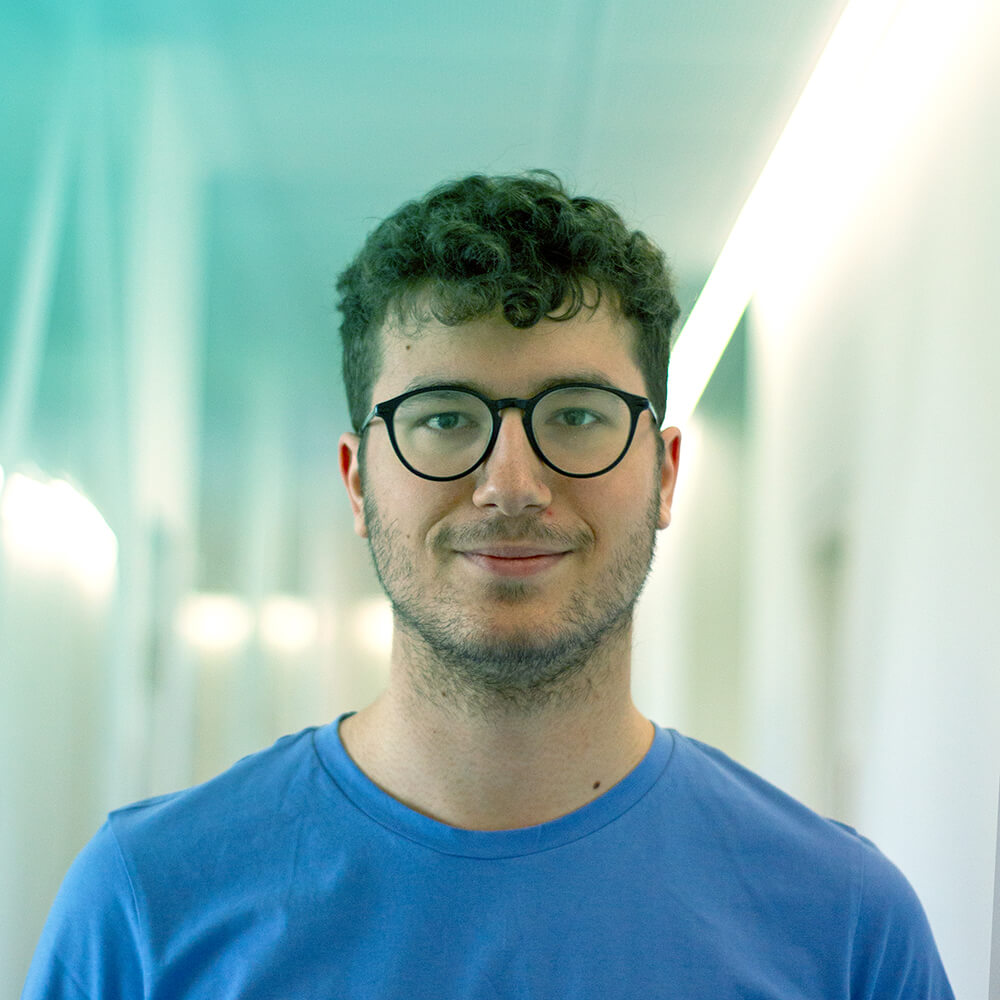
Besic Amin
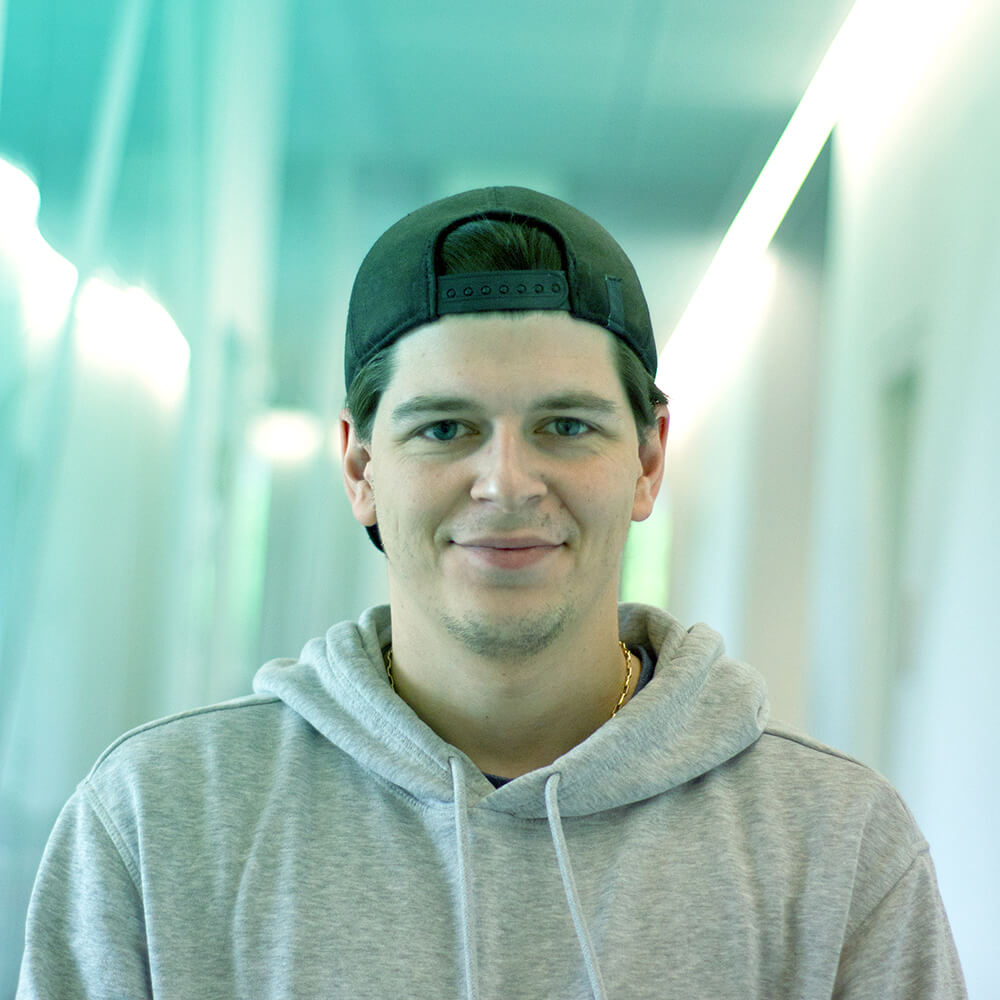
Denis-Bajric
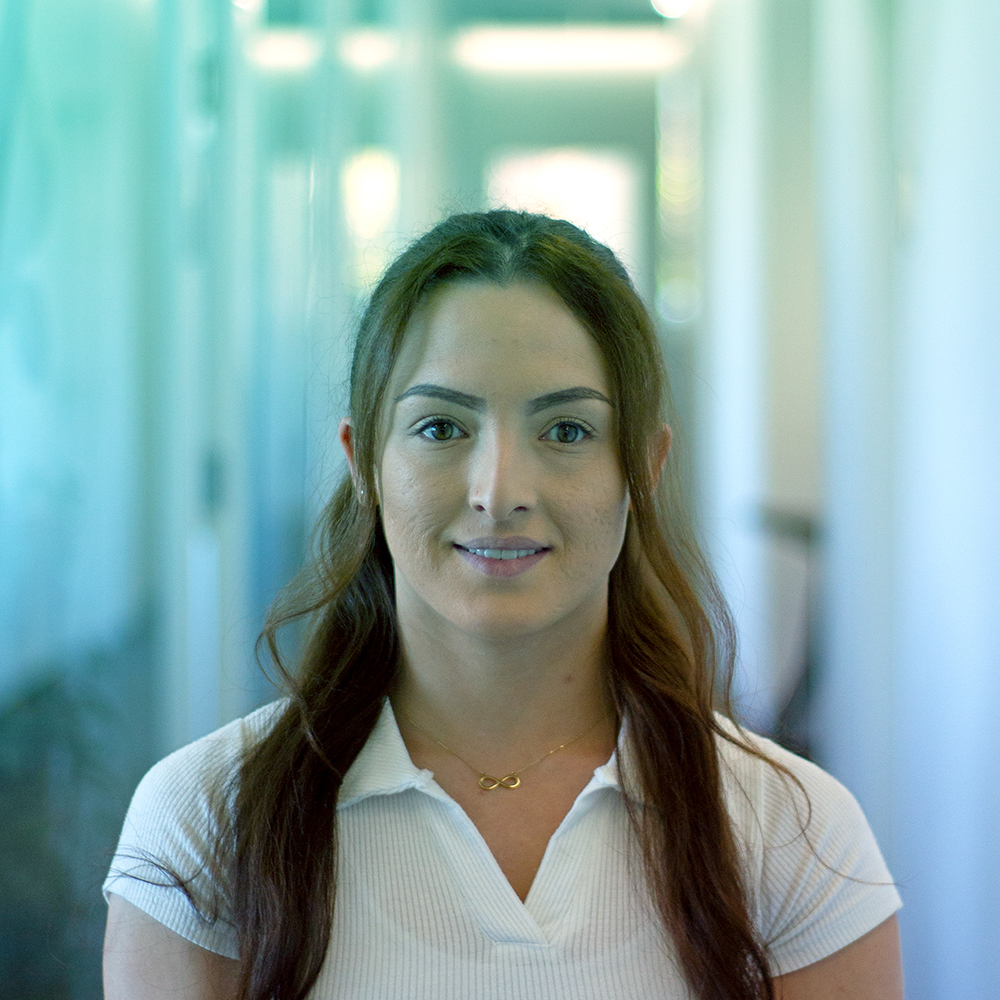
Karadeniz-Ebru
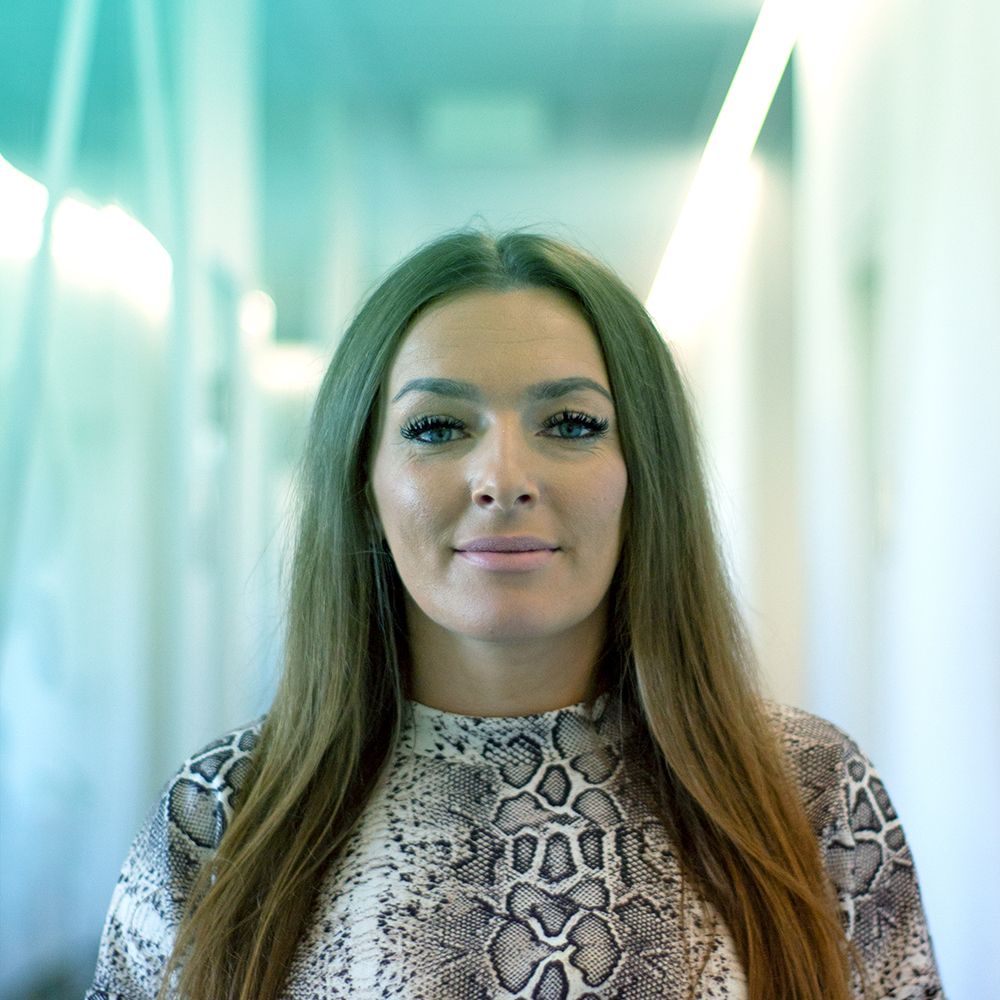
Vidovic-Aleksandra
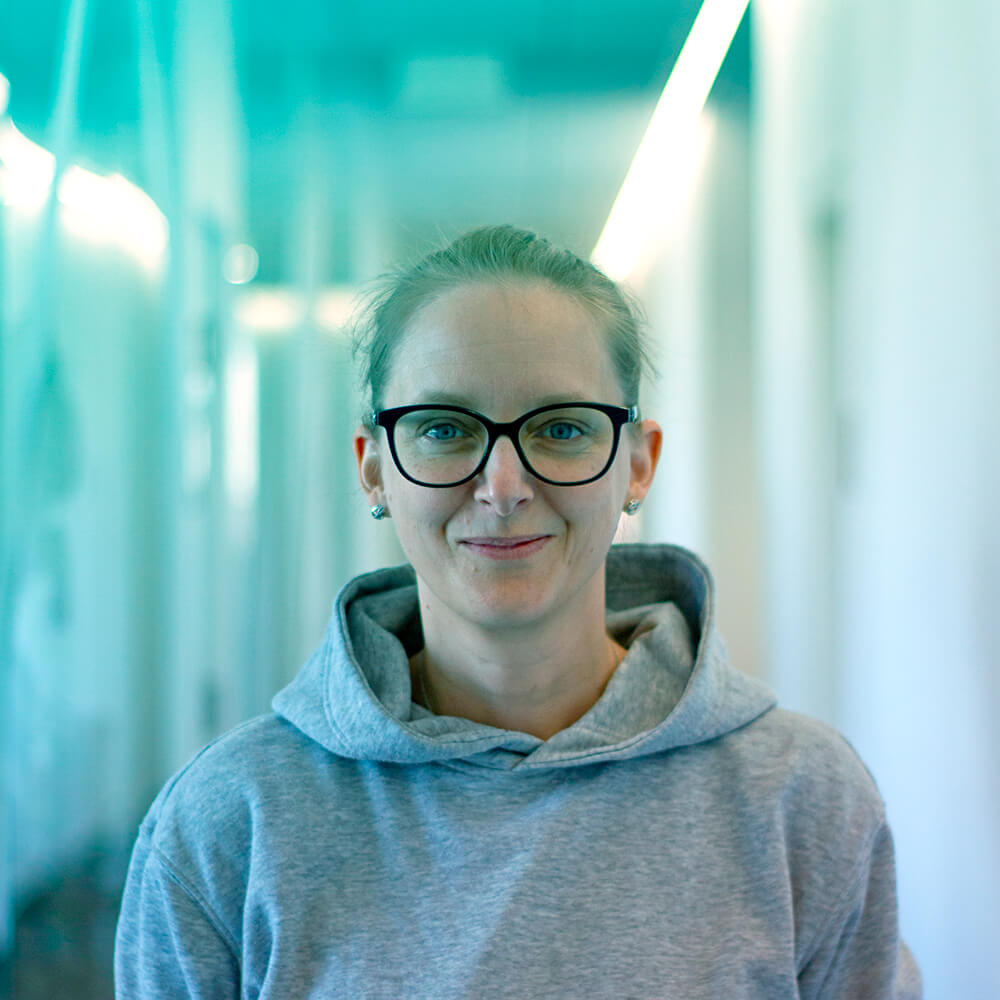
Reiter-Alexandra
Description:
Our daily routine consists of processing the orders that are entered by the clerk. We set up the crowns and bridges and place the blanks in the machine. After that we start the machine. As soon as the milling process is complete, we take the work out of the machine and take it to the dental technology department, where it is processed further by the dental technicians.
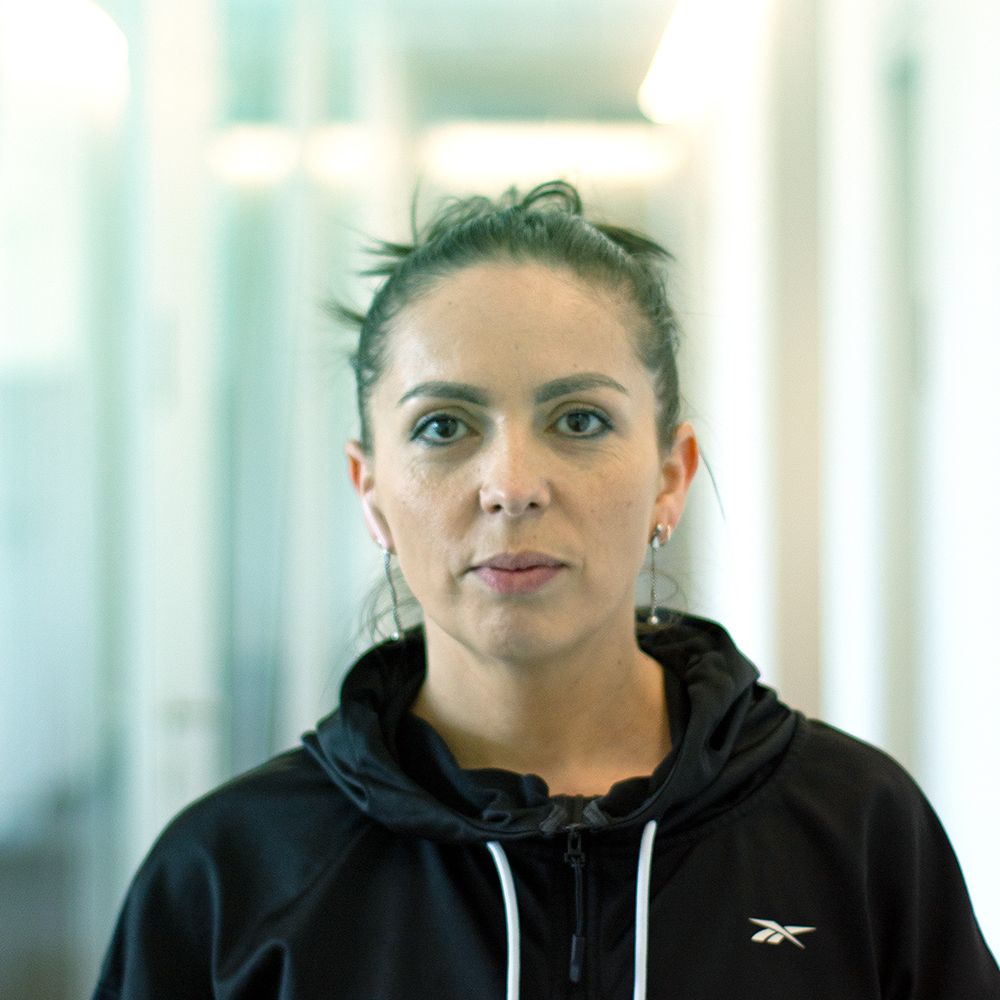
Amela_Alic
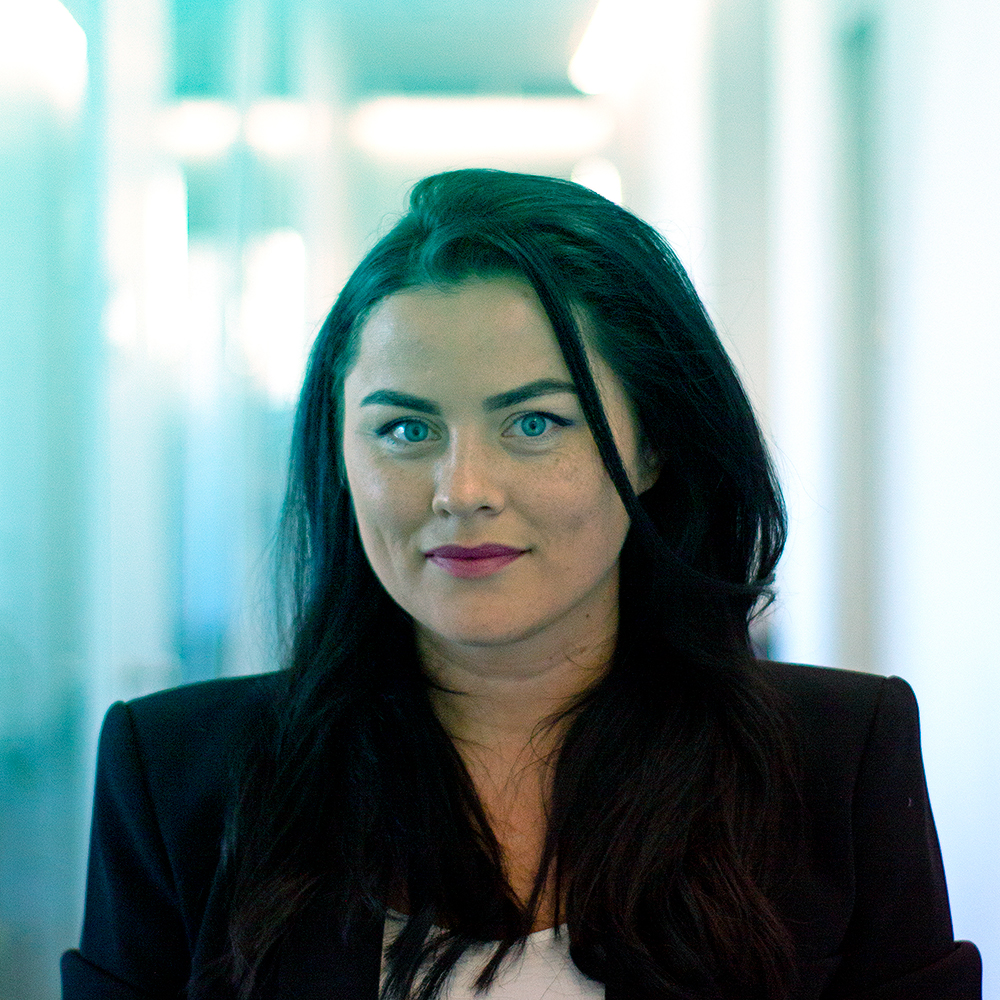
Senida_Demir
Description:
The day-to-day work in this department is individual. In the mornings you are usually very busy with a lot of phone calls and handling customer concerns. In addition, there is the organization and processing of the collection of shipments from our customers. You enter the collections and send the labels to the customers. General organizational tasks such as hotel reservations, train and flight reservations, scheduling appointments, organizing meetings and training courses are also part of this department’s area of responsibility.
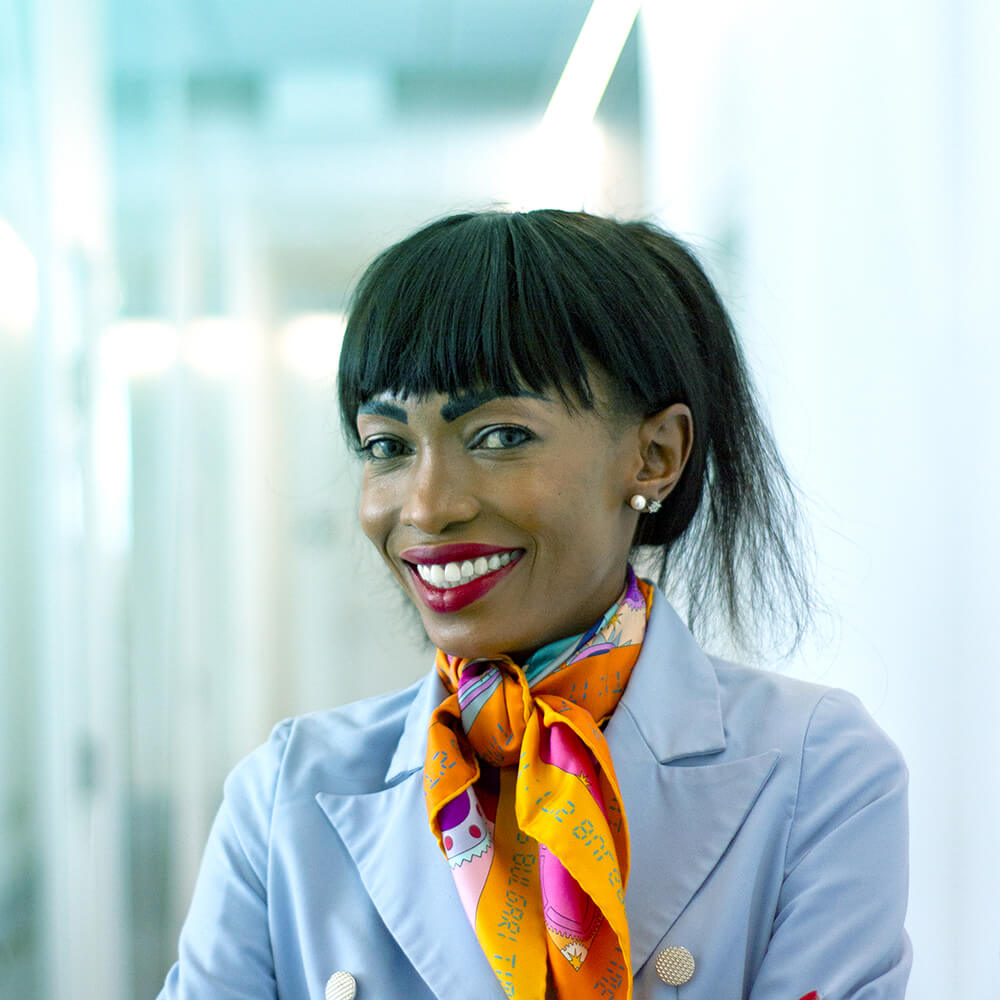
Brenda Severin Dick
Description:
The main task of the marketing department is to convey the corporate image to the outside world. This includes, for example, the website, sales and advertising documents or videos and packaging design. Furthermore, she is an integral part of the company and intervenes in many departments in order to support them visually and technically. This results in further areas of responsibility such as support (protocol documents, webinar technology, …), dental technology (data sheets, instructions for use, …), software development (GUI – user interface), back office (job advertisements, information mails to customers, …) and many others. The social media area is also looked after both technically and conceptually.
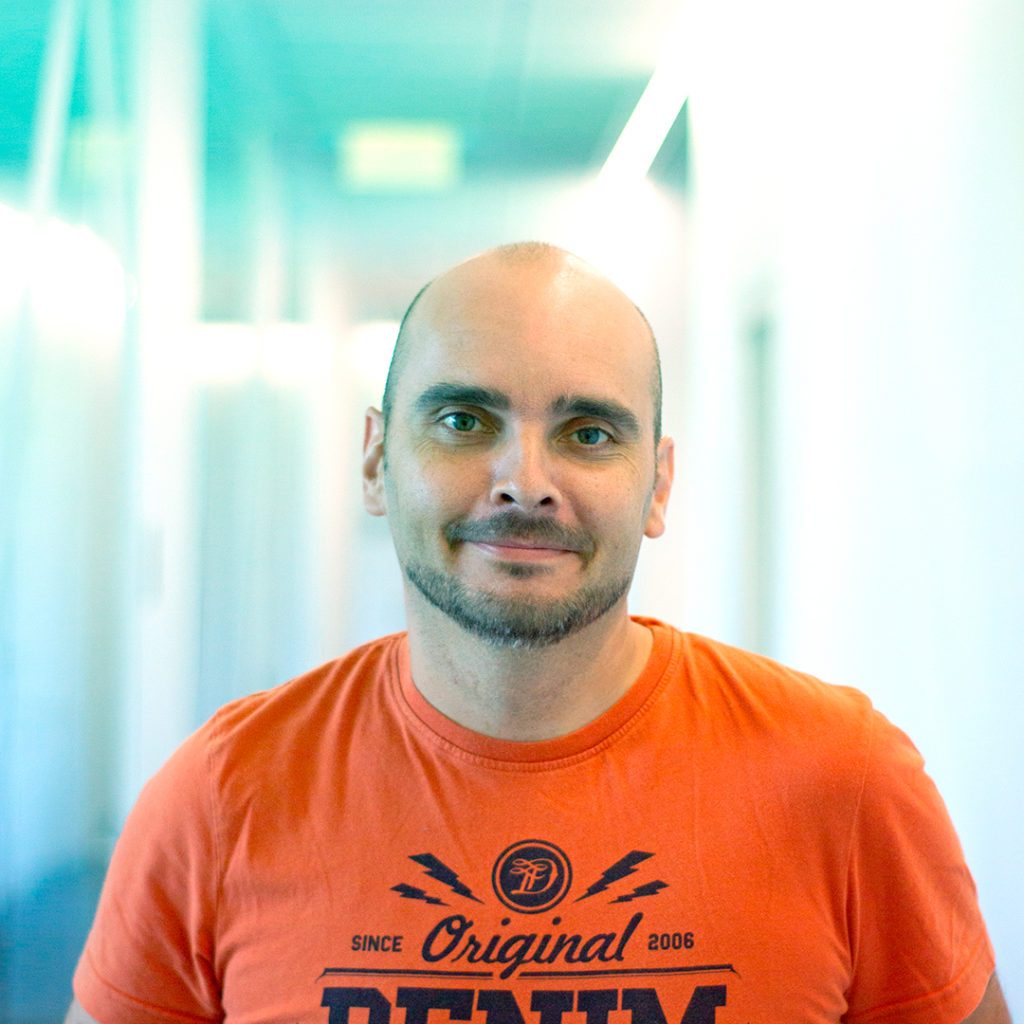
Kurt Brucker
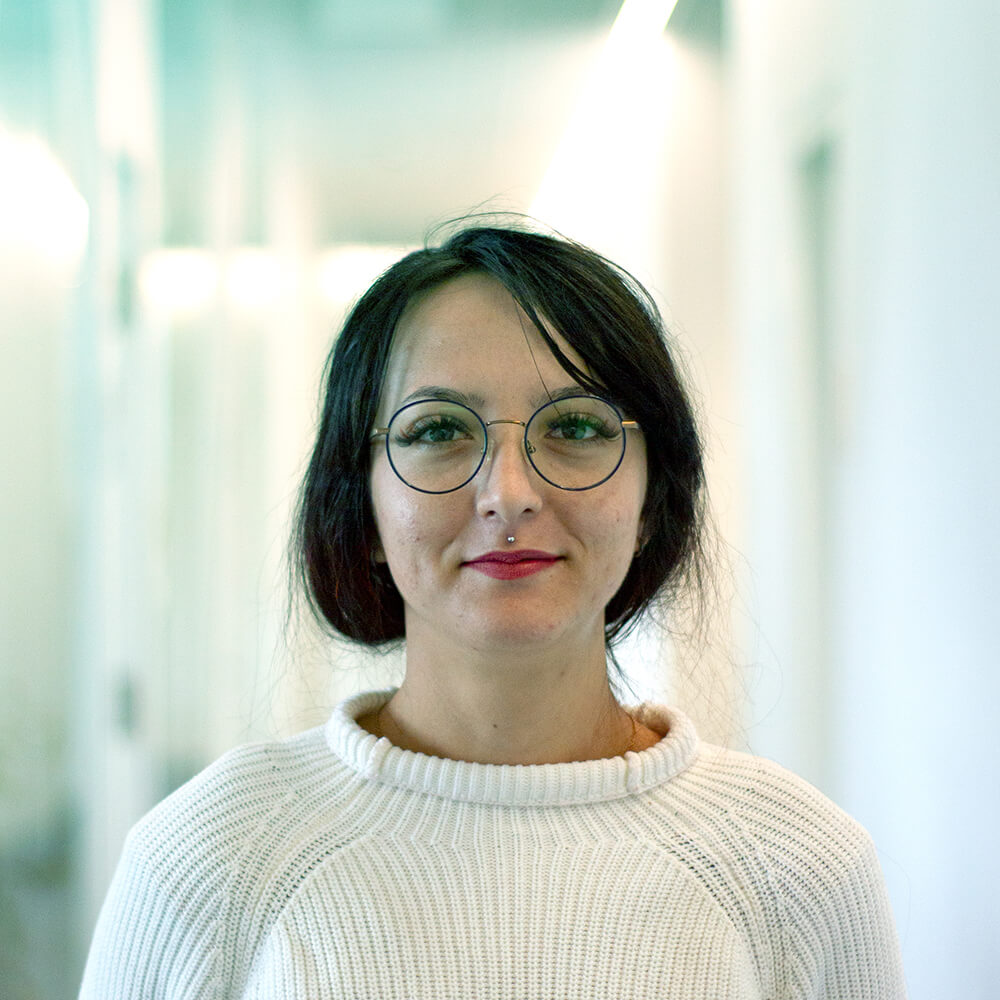
Macelaru-Adelina-Elena-Da
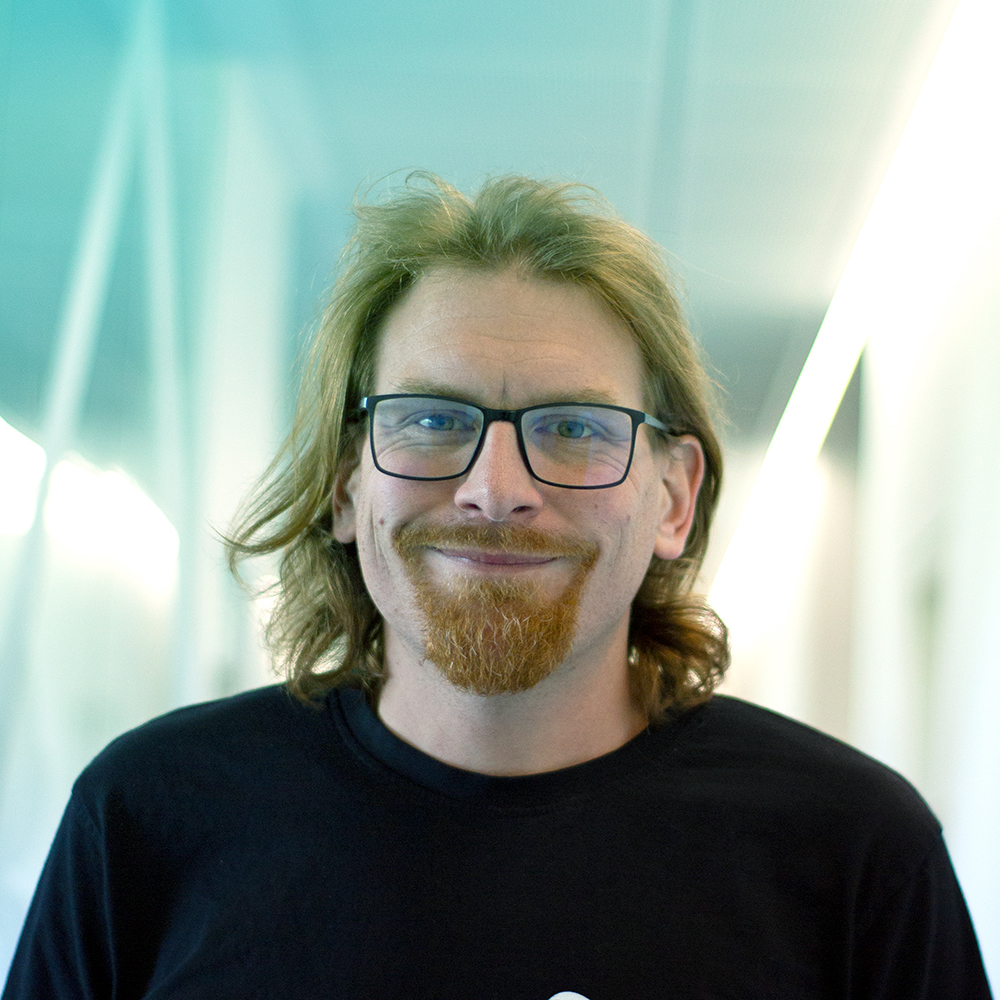
Steueregger-Thomas
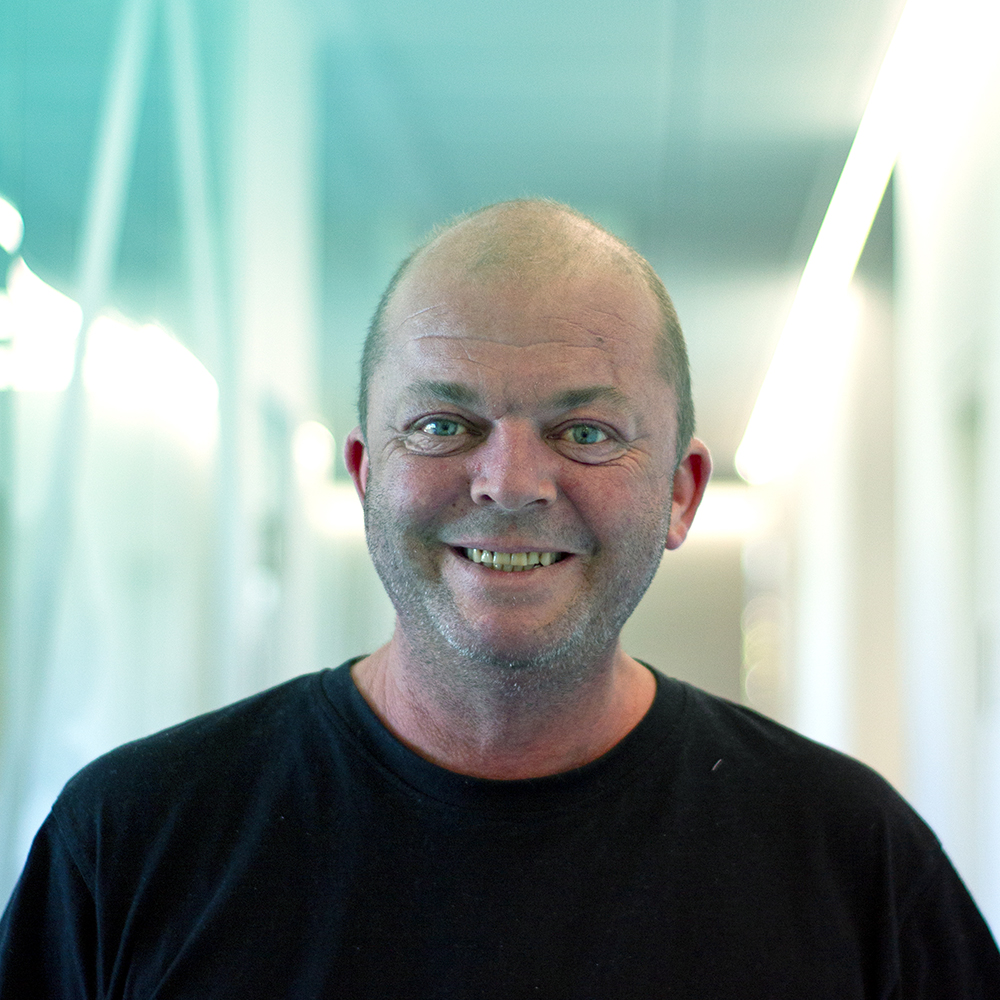
Aigner-Christian
Description:
The main task of this department is to ensure the production and availability of the scanners and their accessories. The development department is also supported. The construction of dental scanners now has a long tradition at CADstar. At the beginning the CS.Ultra, then the CS.UltraPro up to the current model series with the names CS.Neo and CS.NeoPro was developed and produced. The form of the open scanner that has become common in the meantime comes from the pen of CADstar, which was adopted and copied by the competition. All assemblies, cables and accessories in the scanner are produced by this department on a daily basis, thereby guaranteeing availability. All scanners sold in the last few years were finally checked and then passed on to support for shipping. Another area of responsibility concerns the maintenance and repair of the scanners. Regardless of whether a scanner is 3 months or 5 years old, if it is possible and the customer so wishes, the devices will be serviced and repaired. The troubleshooting, which is sometimes necessary, is carried out meticulously and always concluded with a positive result. The further development of the devices is a crucial point that is taken very seriously at CADstar. For this purpose, this department is an important advisor and can also bring in the necessary know-how in some situations, whereby the scanners retain their competitiveness.
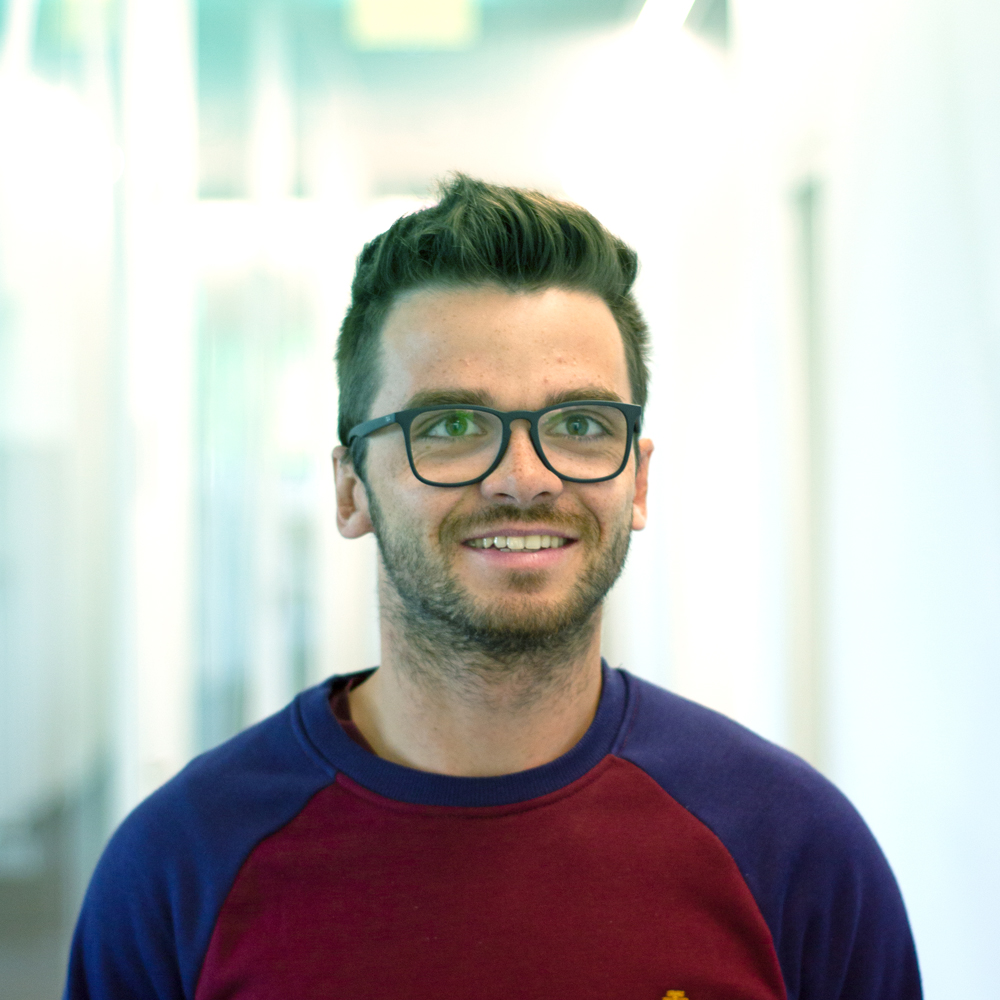
Buchegger Michael
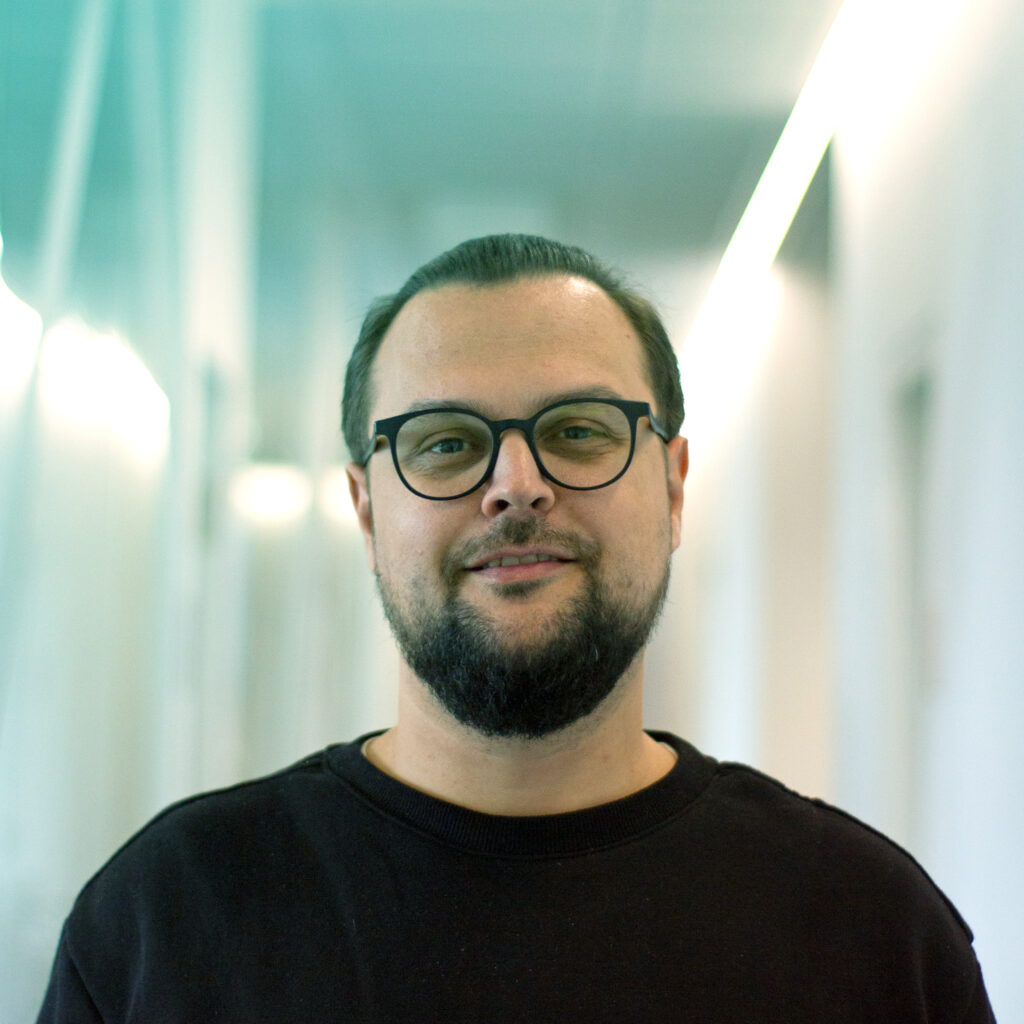
Szabo Istvan
Description:
The support take care of our customers by phone if they have technical questions about our products (scanners) or need help / support with the software. Using the teamviewer, they connect to the customer and analyze the problem. Either it is an application problem (the customer has to be explained how to use the scanner or software) or a technical problem that needs to be solved. If it is a technical problem, it will be analyzed and solved. Furthermore, the department is responsible for the configuration and installation of new customer systems as well as for the final inspection (last test of the scanner) and scanner installation at the customer’s site. In addition, support is always available to all colleagues if we have internal technical problems at our workplaces.
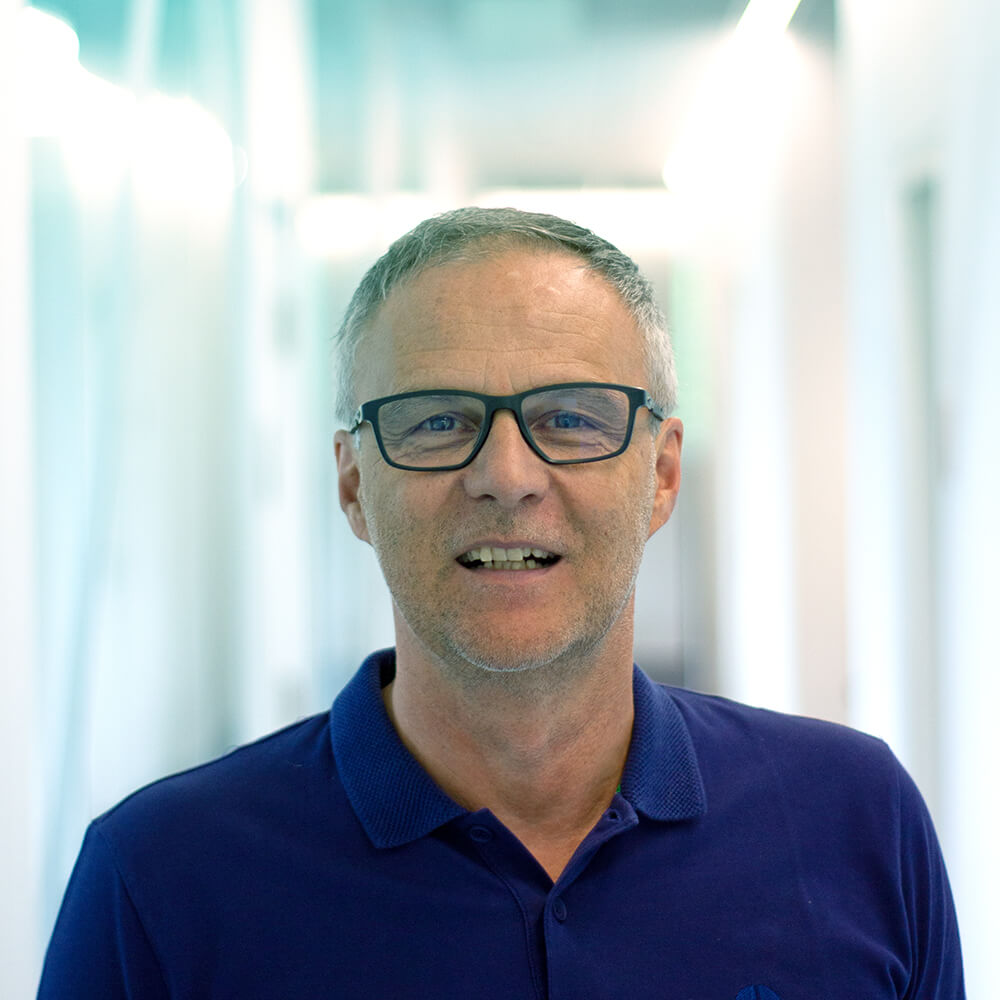
Jürgen_Moser
Description:
Sales is the interface to our customers and dealers. We take care of the submission of offers, the presentation of our products, the closing of the sale and the aftercare of our customers. Furthermore, we try to find new dealers and to inspire them with our products in order to open up new markets. Since 2021, we have also been looking after laboratory customers in order to offer our services here and to ensure a long-term business relationship. All necessary sales and distribution documents (price lists, sales folders, etc.) are prepared together with the marketing department.
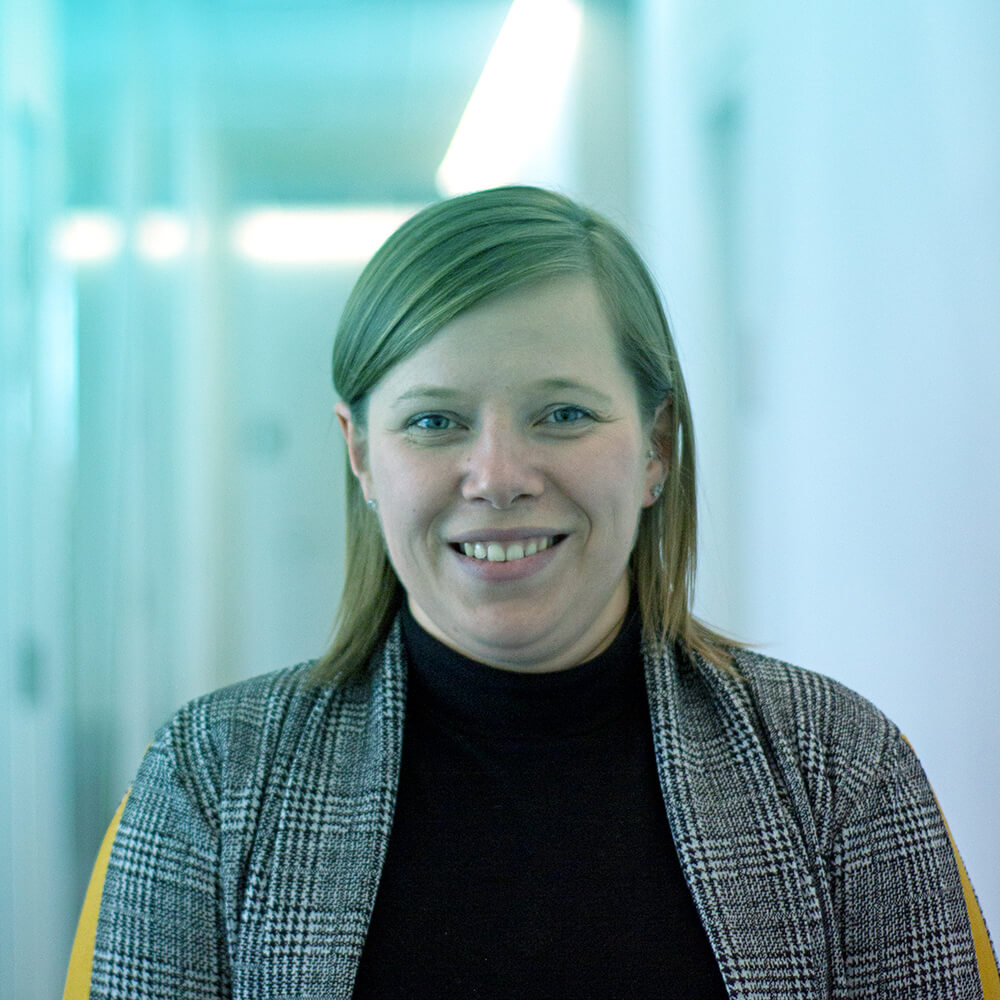
Lechner Susanna
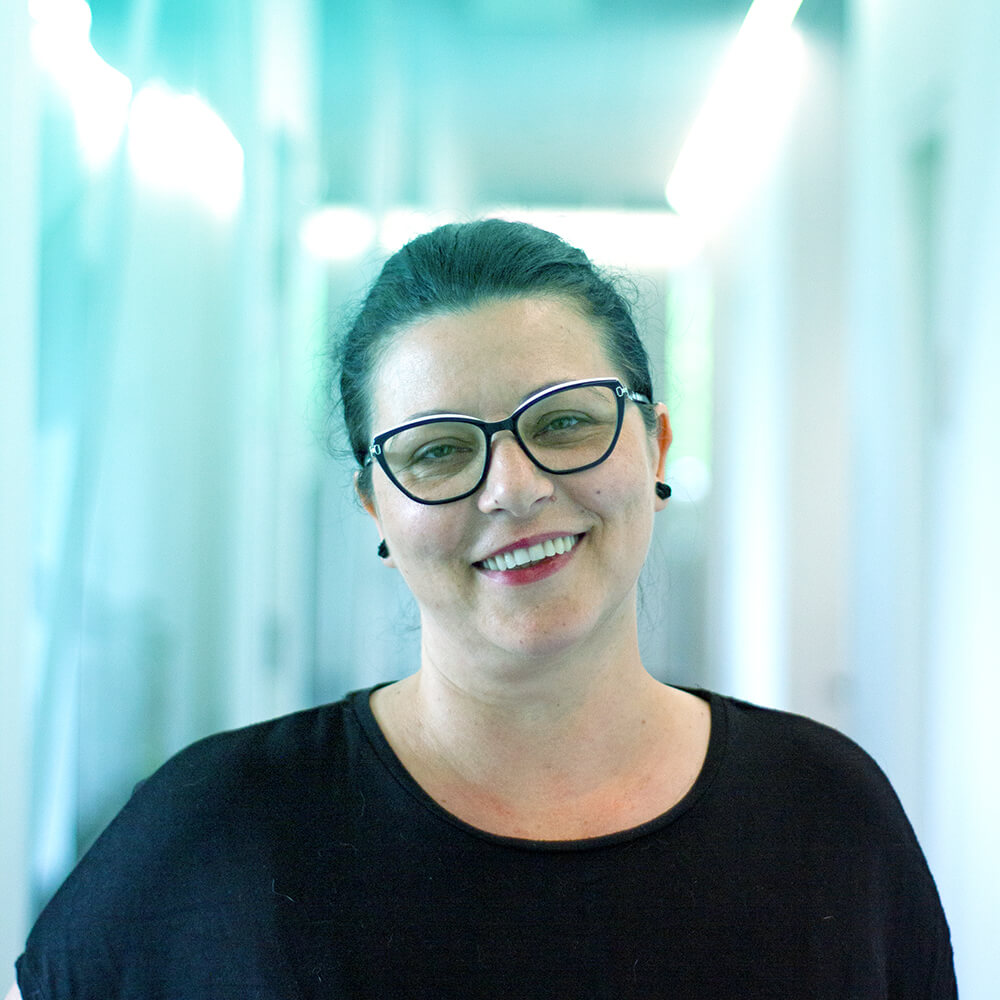
Mirela-Wechselberger
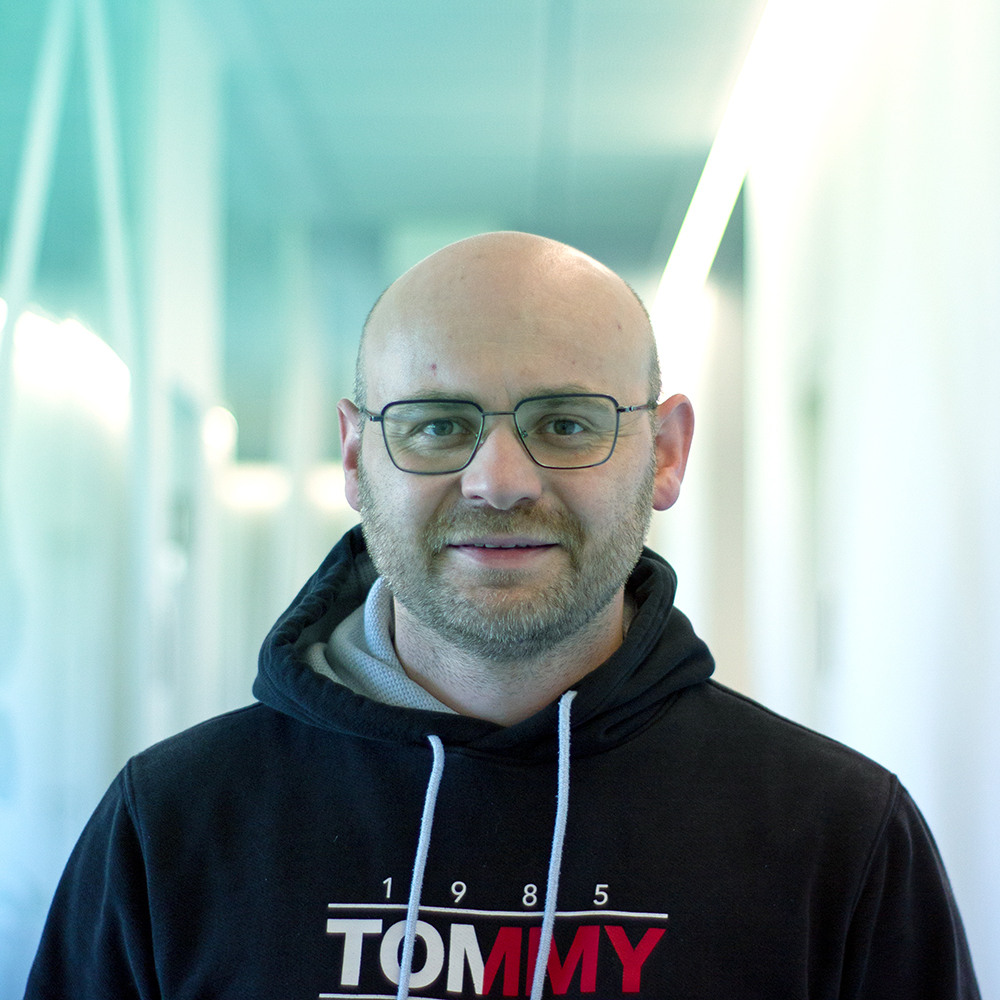
Peula-Ljubinko
Description:
On average, around 150 commissioned work per day is accepted by this department, prepared for further processing and handed over to the respective department. After production, the work comes back, is packaged and then delivered either with GO-Express or the outbound (work from the Salzburger Land). They also take care of auxiliary dental work (scanning, grinding chamber, …), prepare the invoices or add advertising material to the packaging. Any customer questions will be answered if possible or forwarded to the appropriate department.
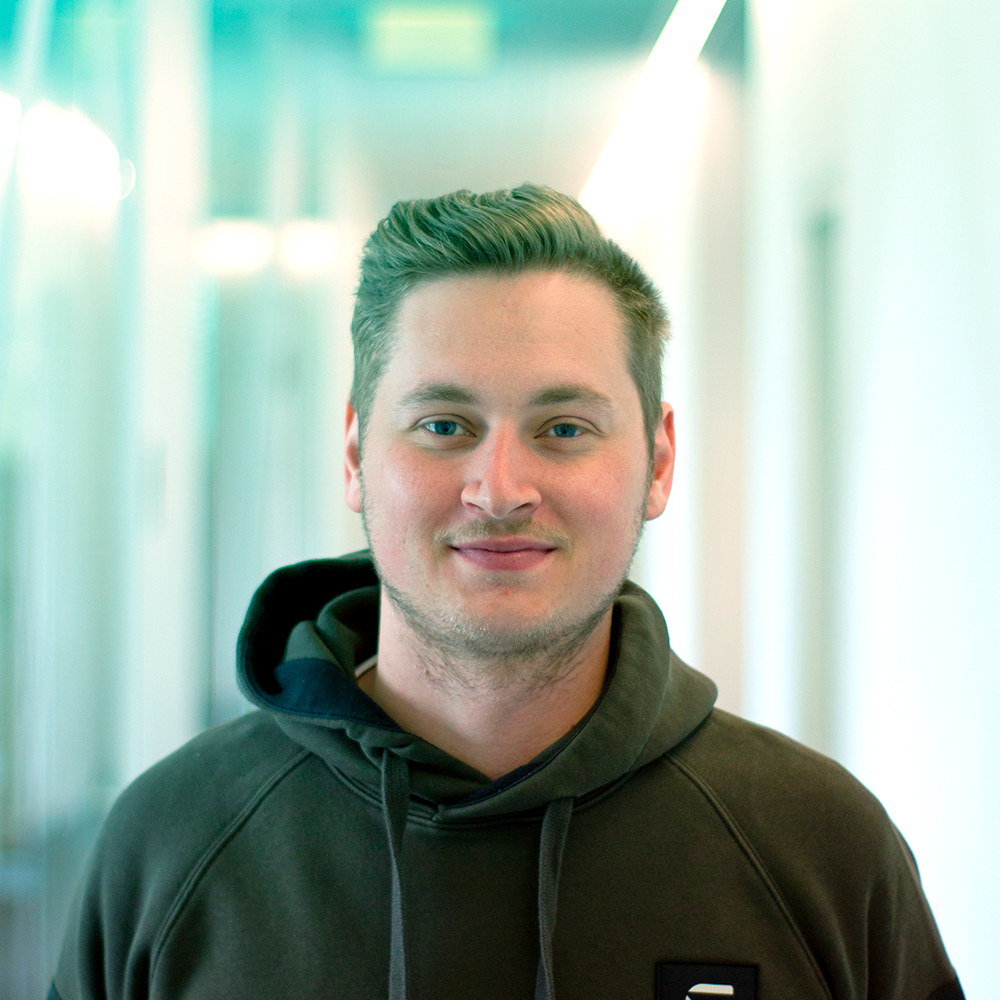
Berger Daniel NEU
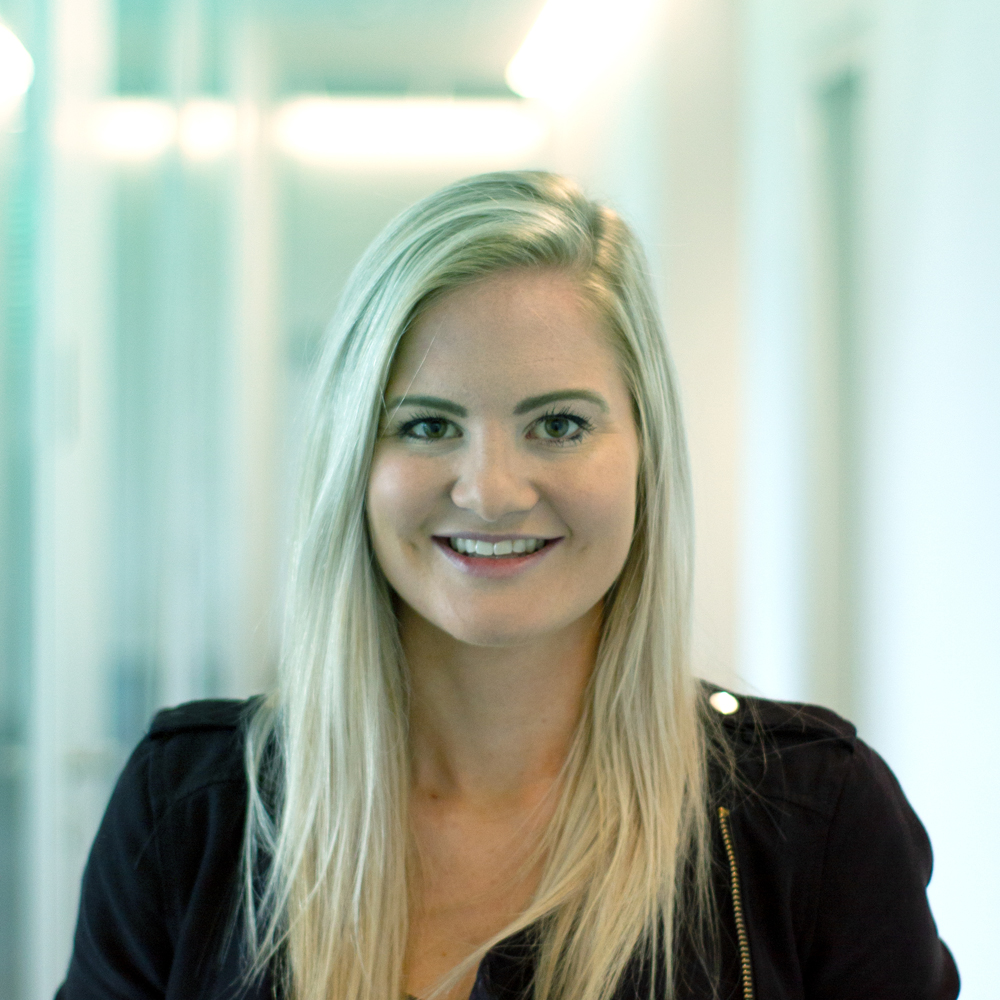
Clee Laura
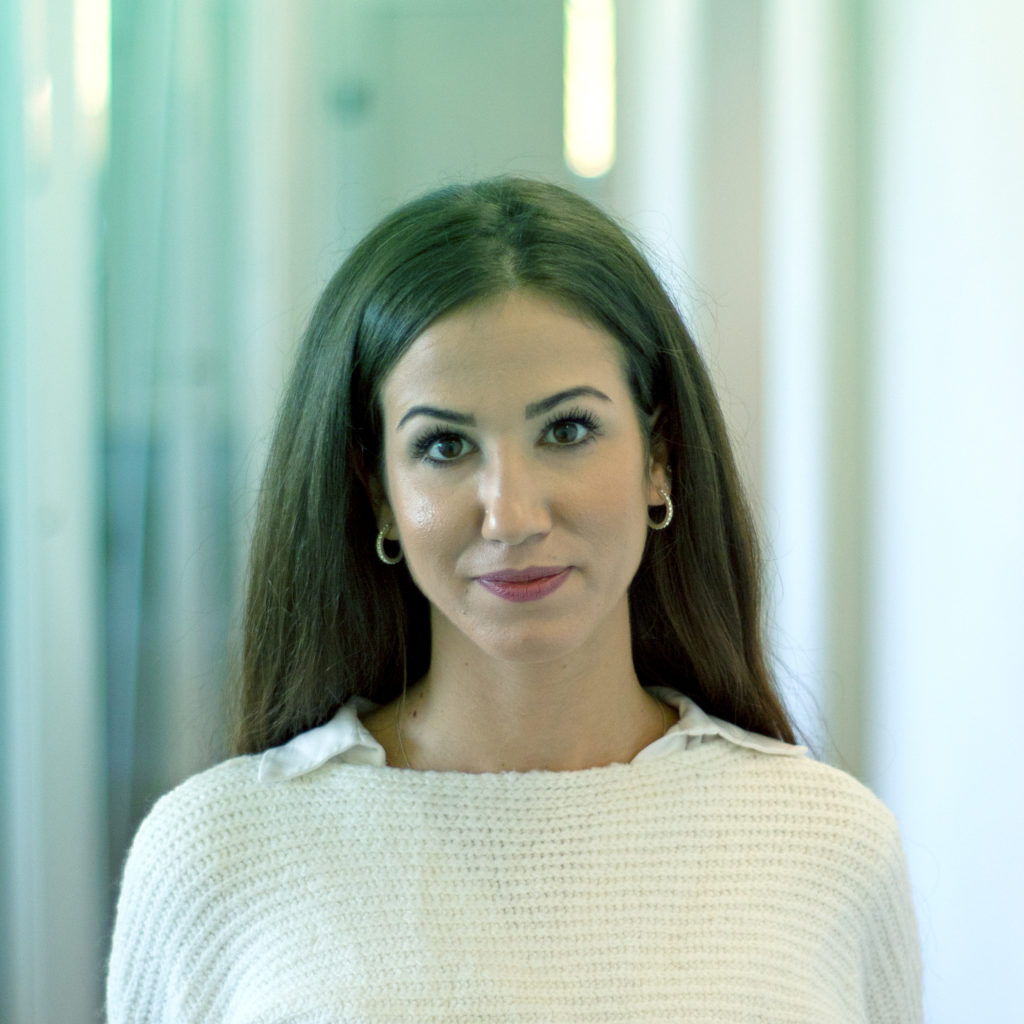
Amina Besic
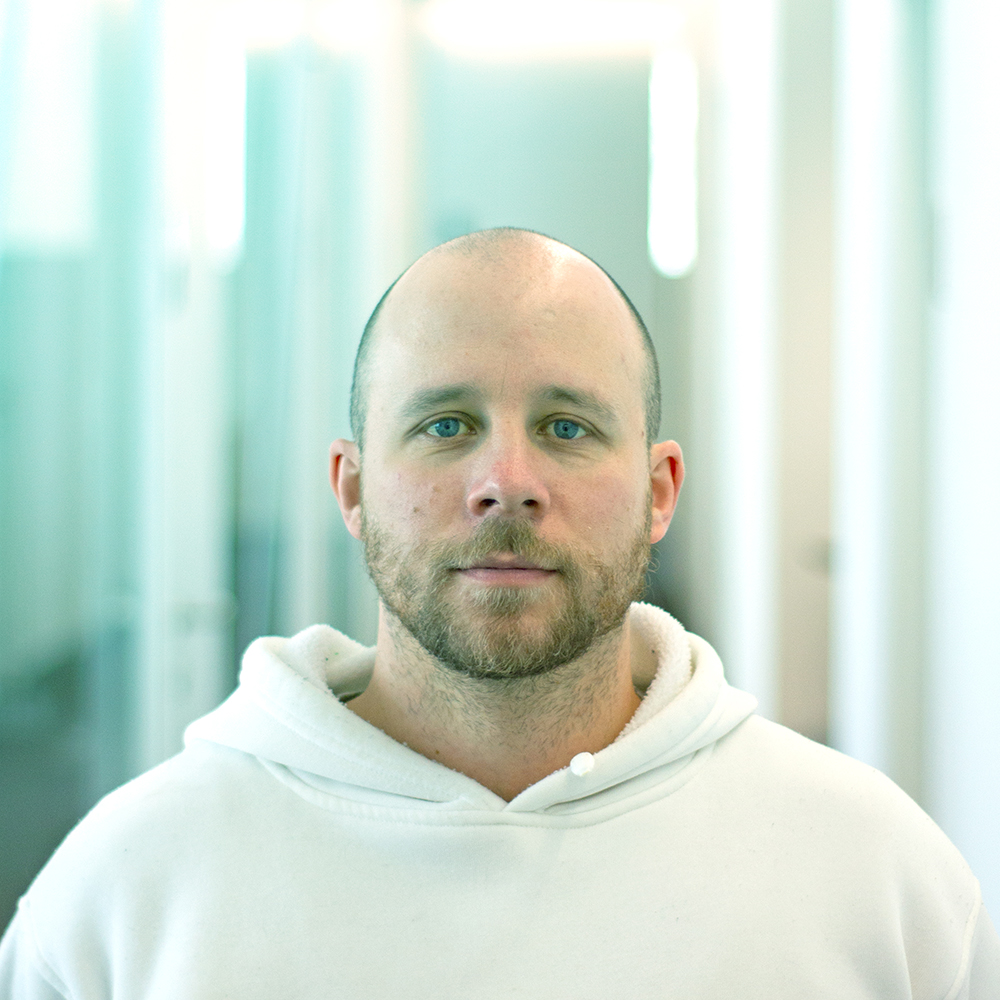
Matija_Filimonovic
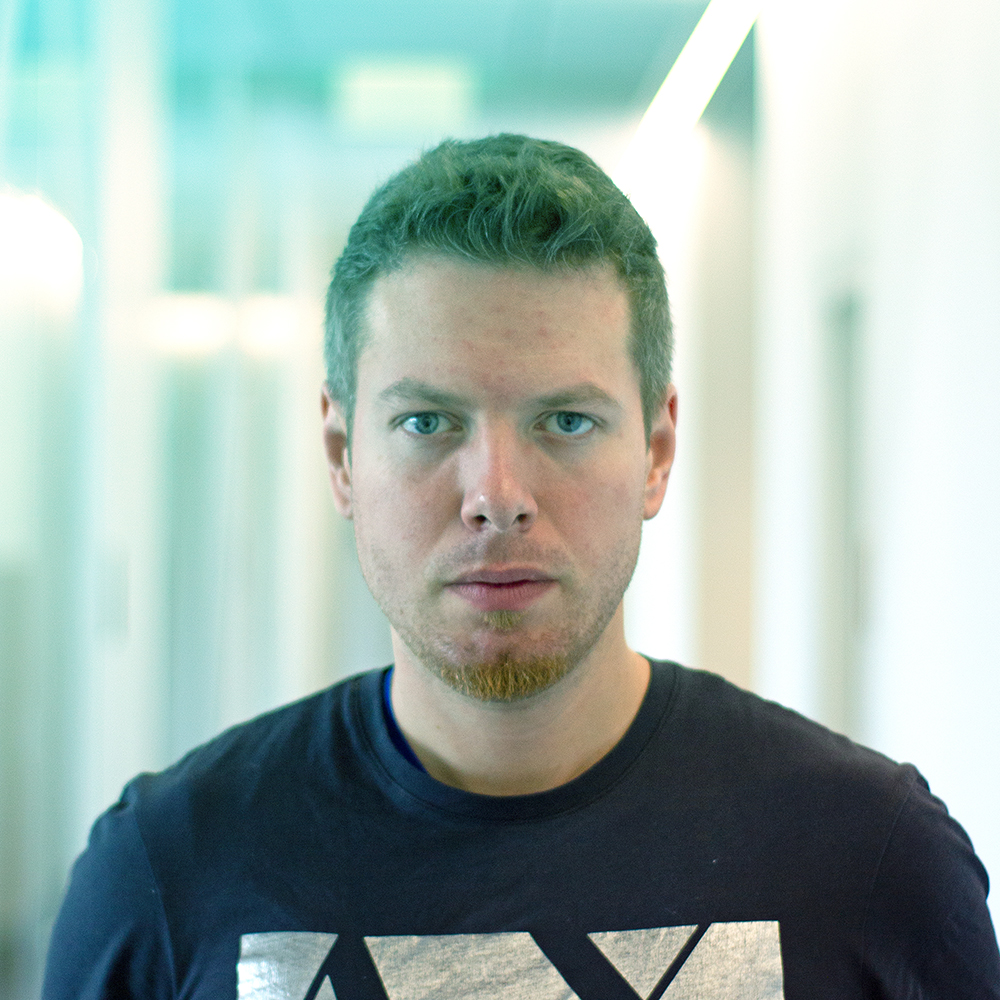
Popovic_Alen
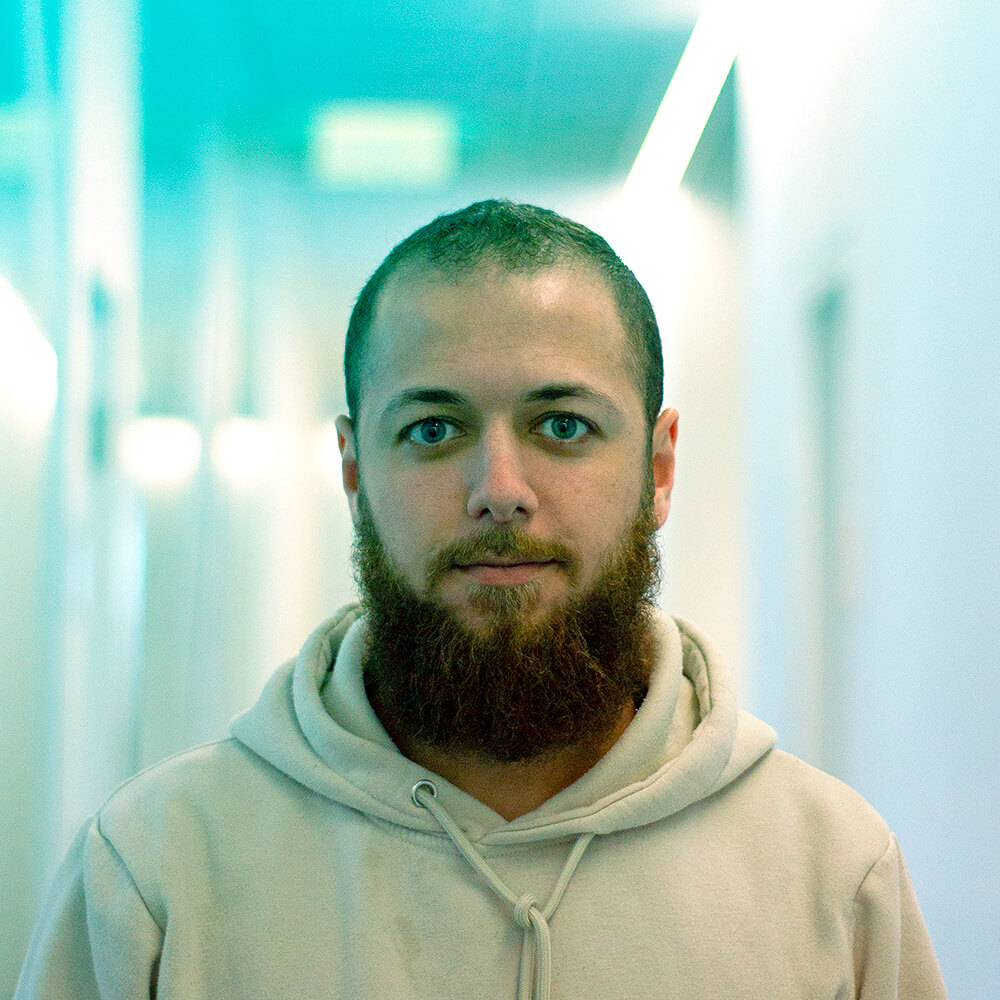
Alsukhni-Mohamad
Description:
Your area of responsibility is very diverse and varied. The core tasks include the digitization of dental work on the in-house CS.Neo with subsequent modeling of the respective dental prosthesis (zirconium, non-precious metal, titanium, individual one-piece abutments, hybrid abutments, bars, SLM, etc.), including product advice over the phone or the very positively received dental technology Support. Subsequently, also the prostprocessing of all materials and work of the dental milling service up to quality assurance before the work is dispatched to the customer. Other very extensive tasks include the interfaces between the customer and the planning office for the Star Aligner treatments (invisible splint correction of the teeth). In addition, the support of customers when ordering original prosthetic parts and special structures, the interface between the dental technology area of CADstar and DDT as well as the technical support of colleagues in support and in all other departments.
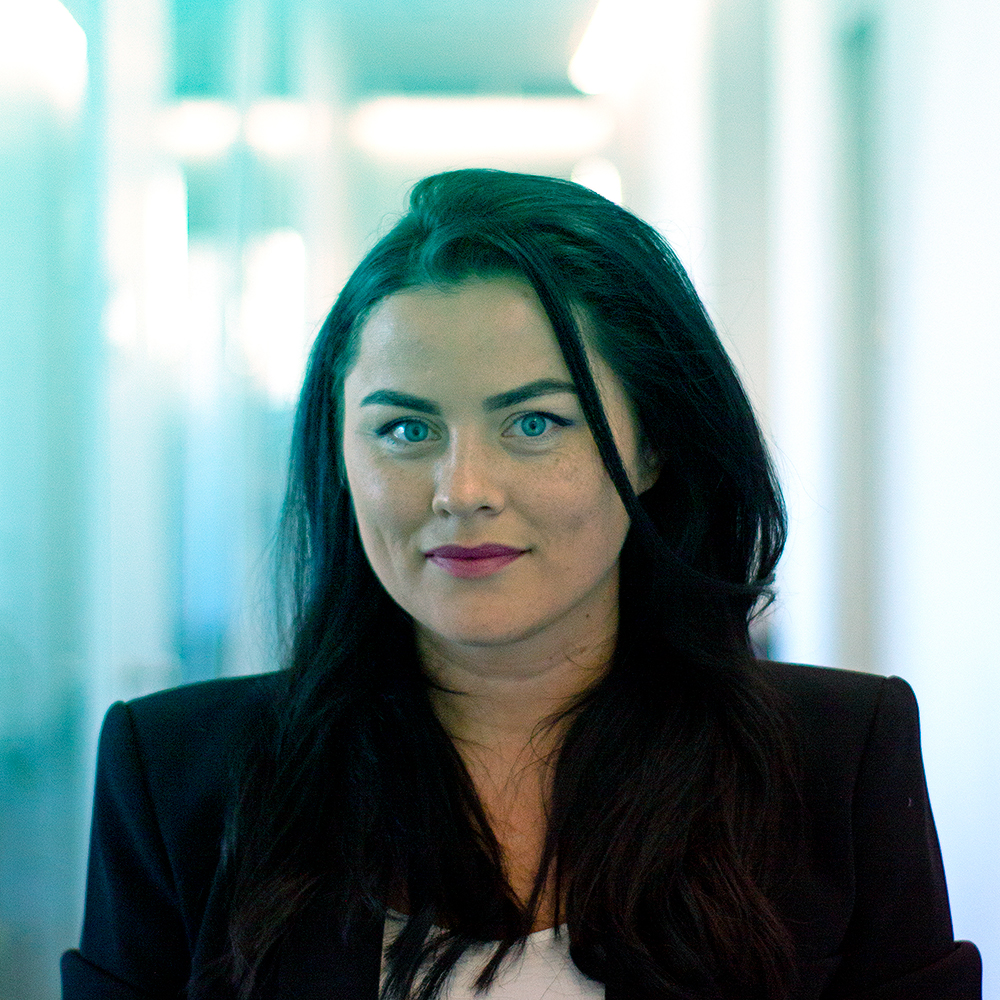
Senida_Demir
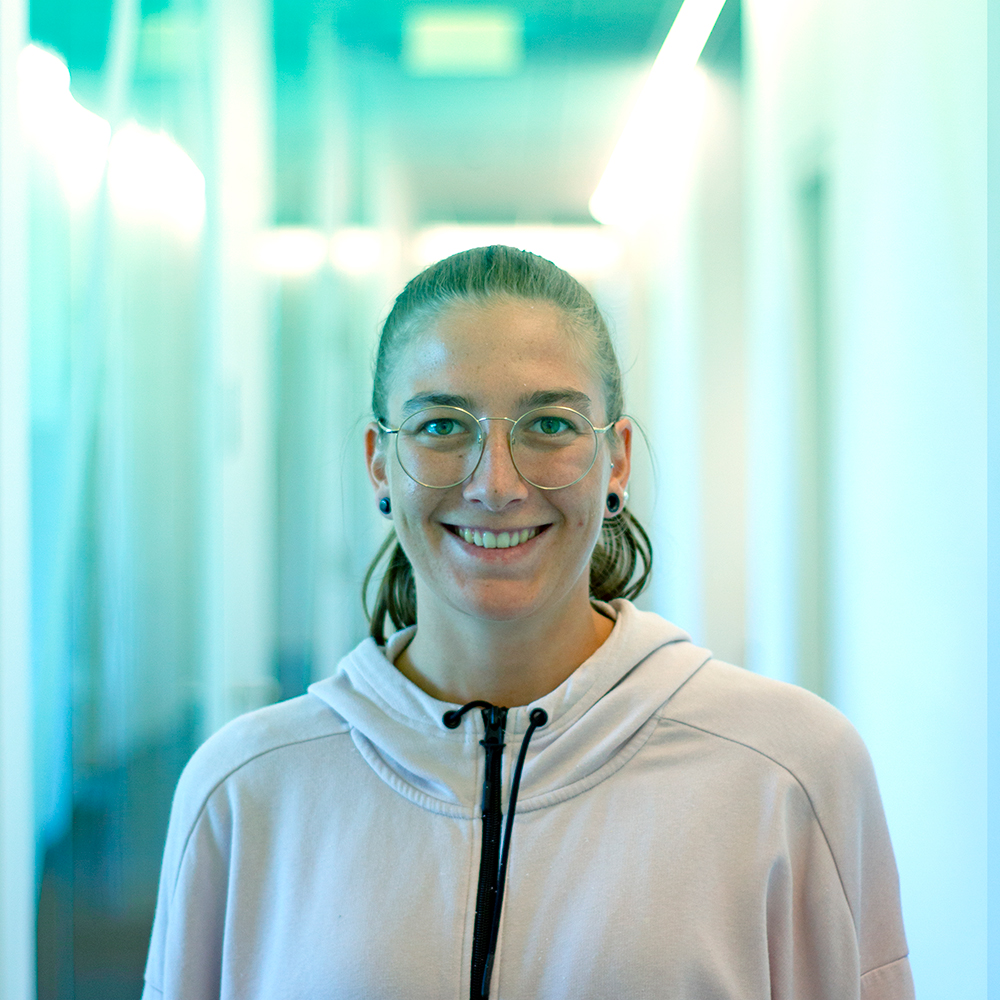
Julia Webinger
Description:
This department takes care of the dental work preparation. Her work areas include the electronic recording of orders, the creation and finishing of the models (plaster, saw cut, working model and master model) and the articulators. These work steps make a major contribution to ensuring the high quality standard. Furthermore, the Staraligner splints are also worked out here.
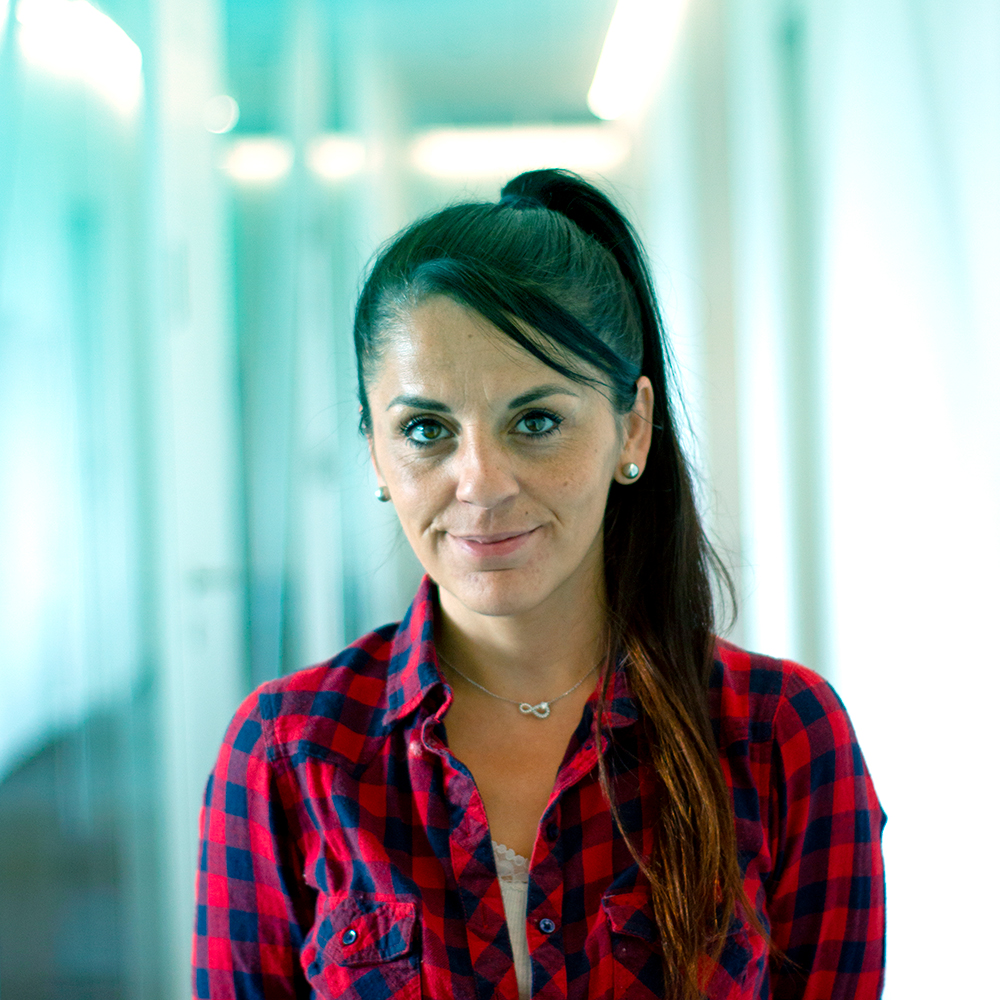
Guelcan Sensu
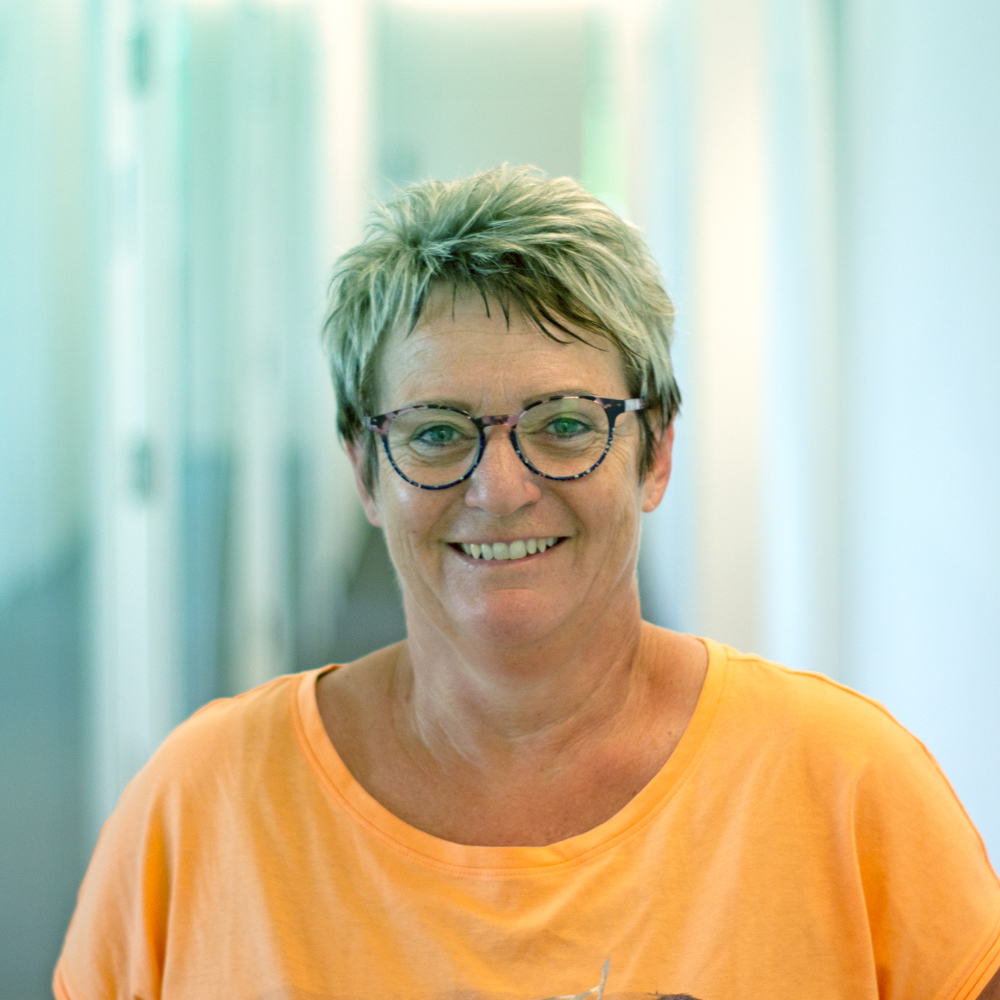
Siller Andrea
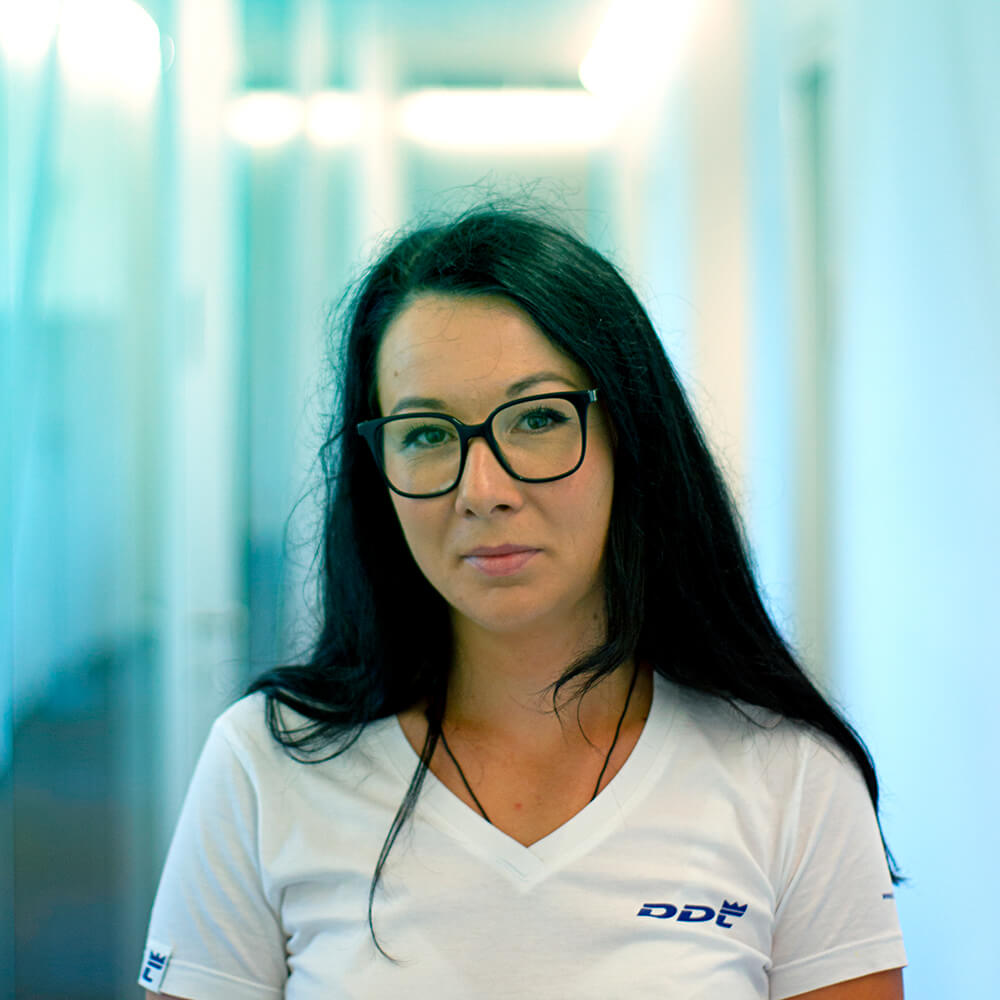
Anca Chiriac
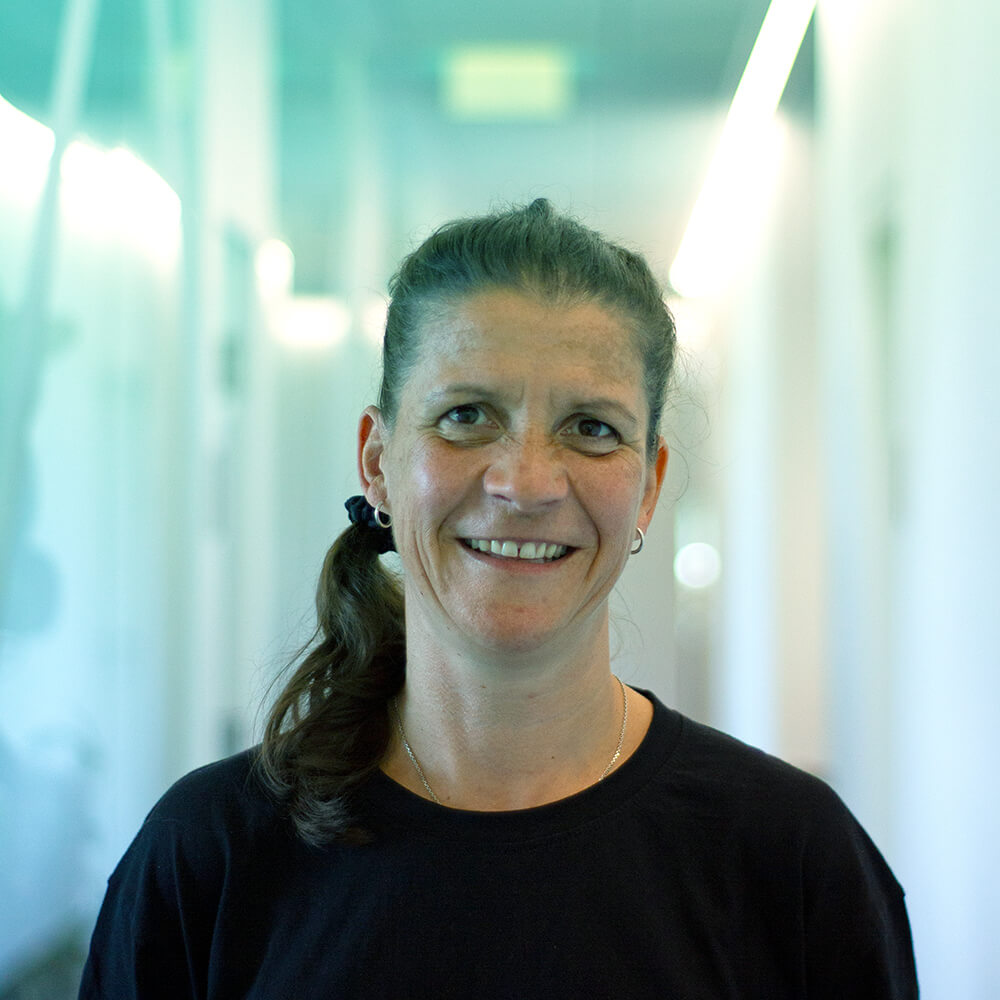
Gold-Mandy
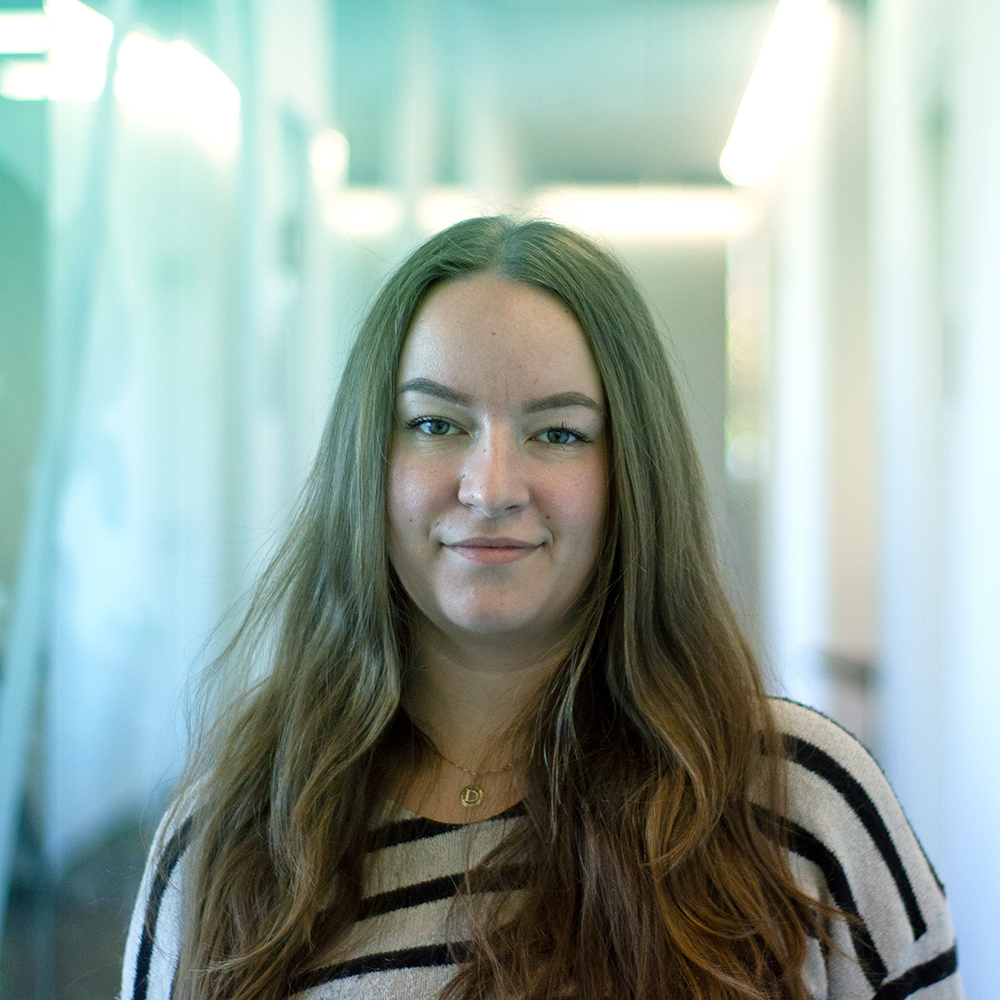
Bajric-Lejla
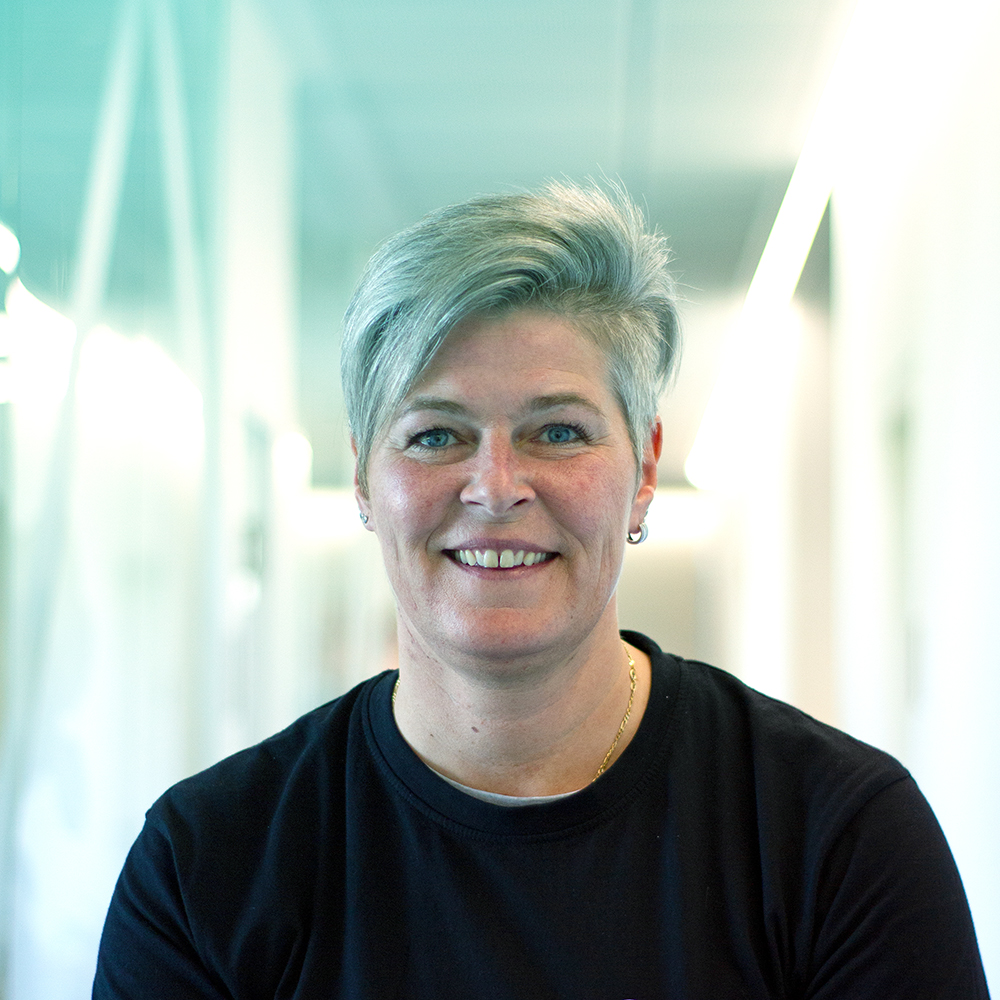
Gfrerer_Renate
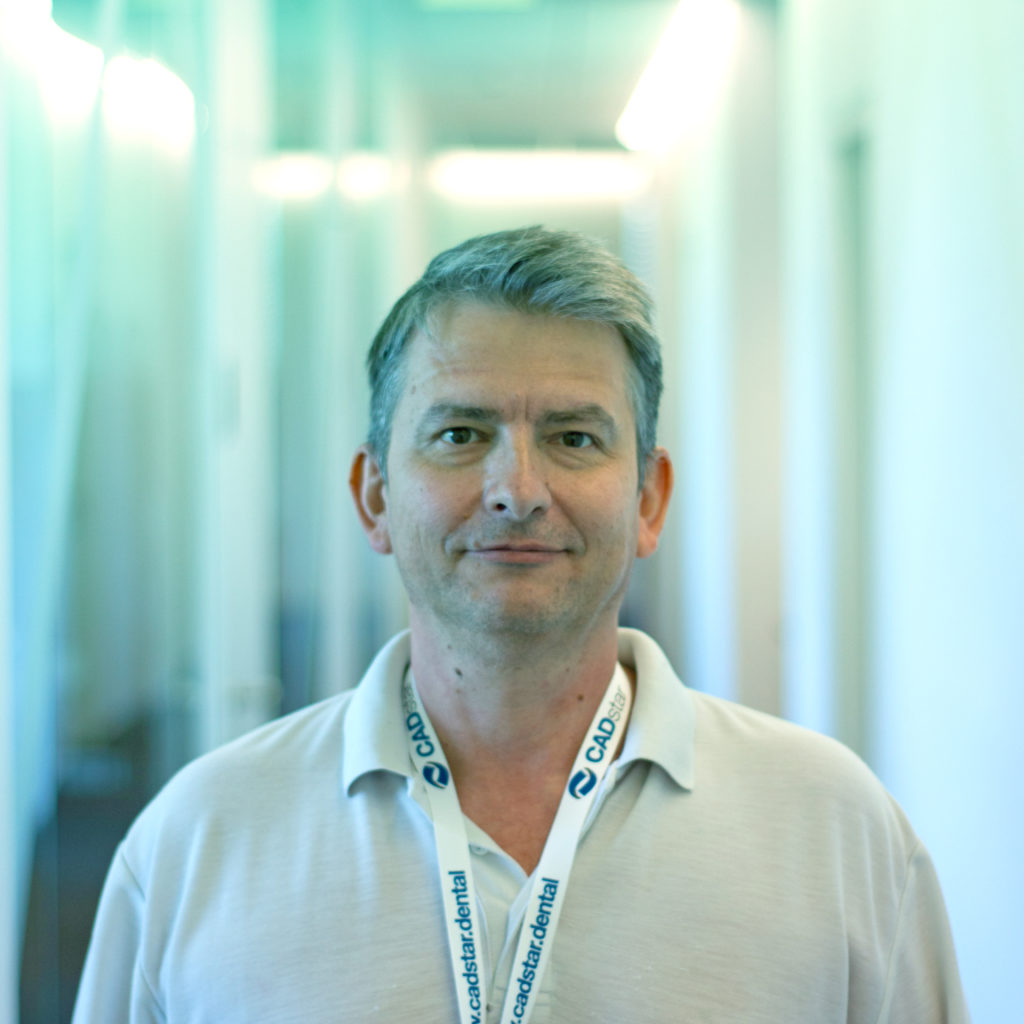
Peter Lapanja
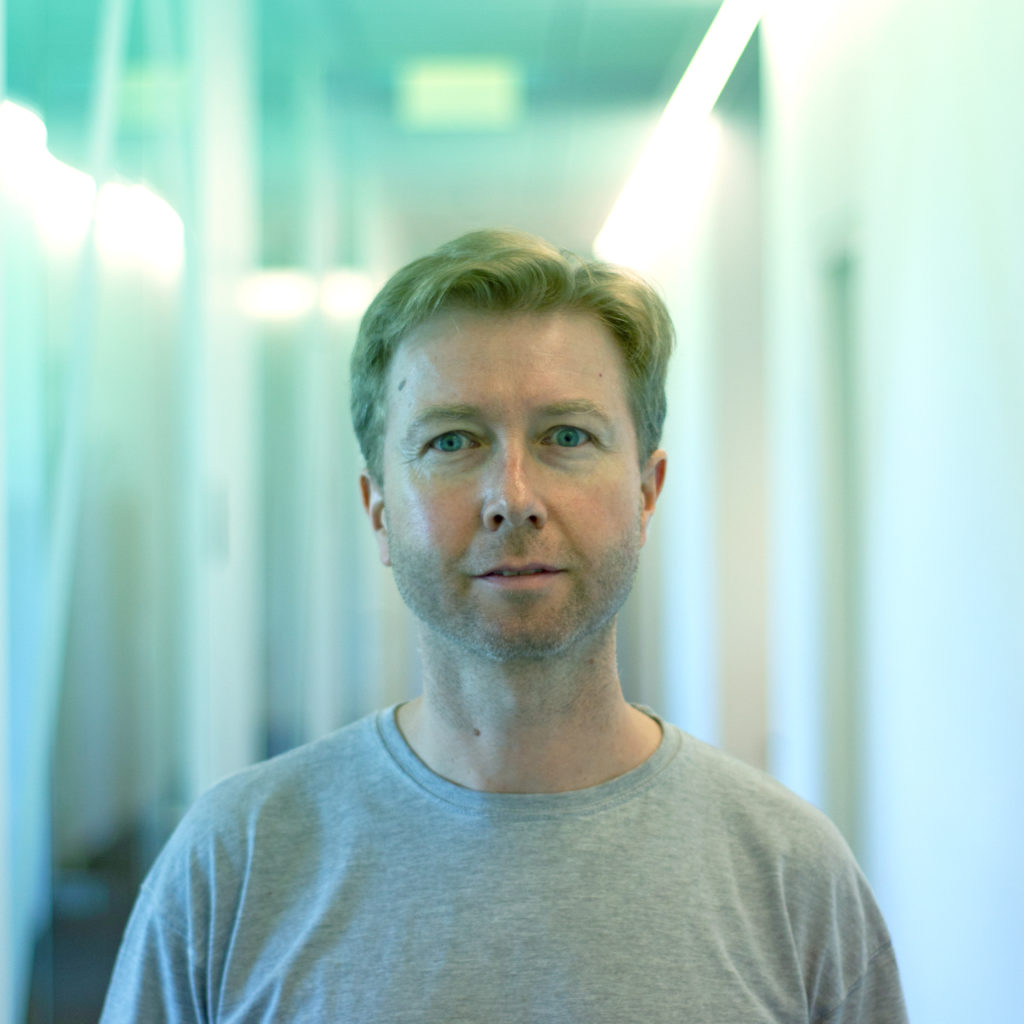
Walter Stadler
Description:
The dental work that our ceramists do on a daily basis is of a very high quality. Ceramic: There are many methods of producing a tooth in ceramic. The traditional procedure is as follows: First a coping is modeled in wax, then embedded and placed in a preheating furnace. In the furnace, the wax melts from the so-called muffle, creating a hollow shape. The metal is shot into the muffle with the help of a high-frequency slingshot; when working with gold, the metal is usually melted with an open flame and shot with the help of the sling. Afterwards, the coping is divested and finished, then the ceramic work can begin. The desired tooth color and shape are created with the aid of ceramic materials, while accents and individualized features are imitated with stains. With the help of CAD / CAM and different materials, the desired tooth shape and color can be milled, this saves the ceramists a little time and they do not have to apply the tooth shape with ceramic materials, but only minimally grind the shape, rework the contact points and the crown finish with paints and glazes.
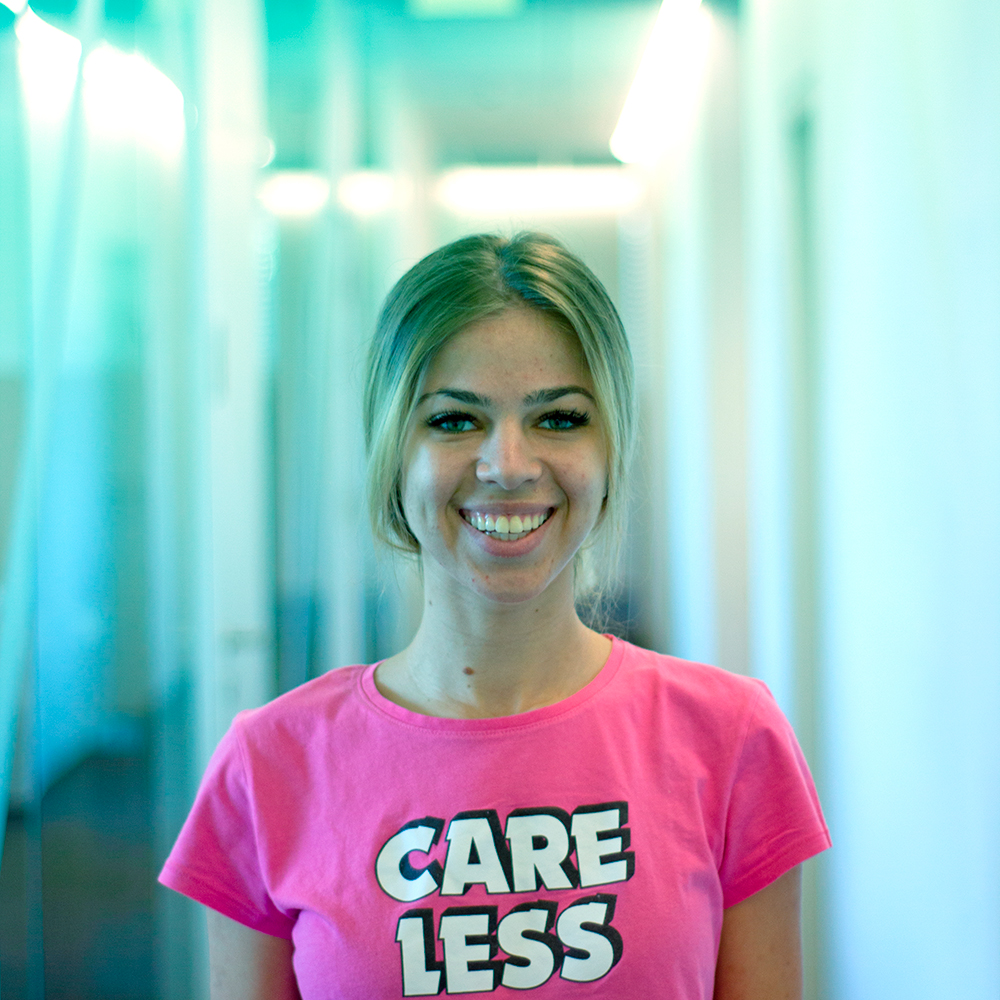
Emana Sulic
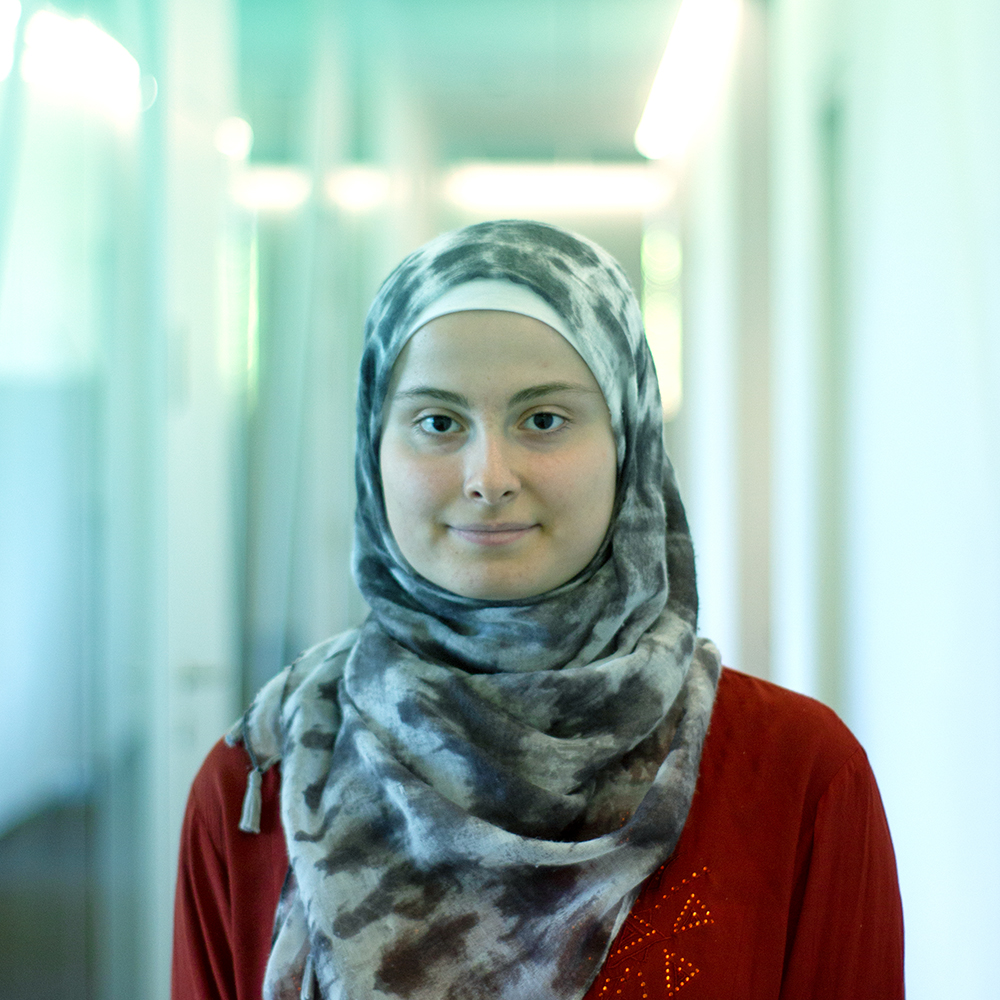
Raghad Sapatw
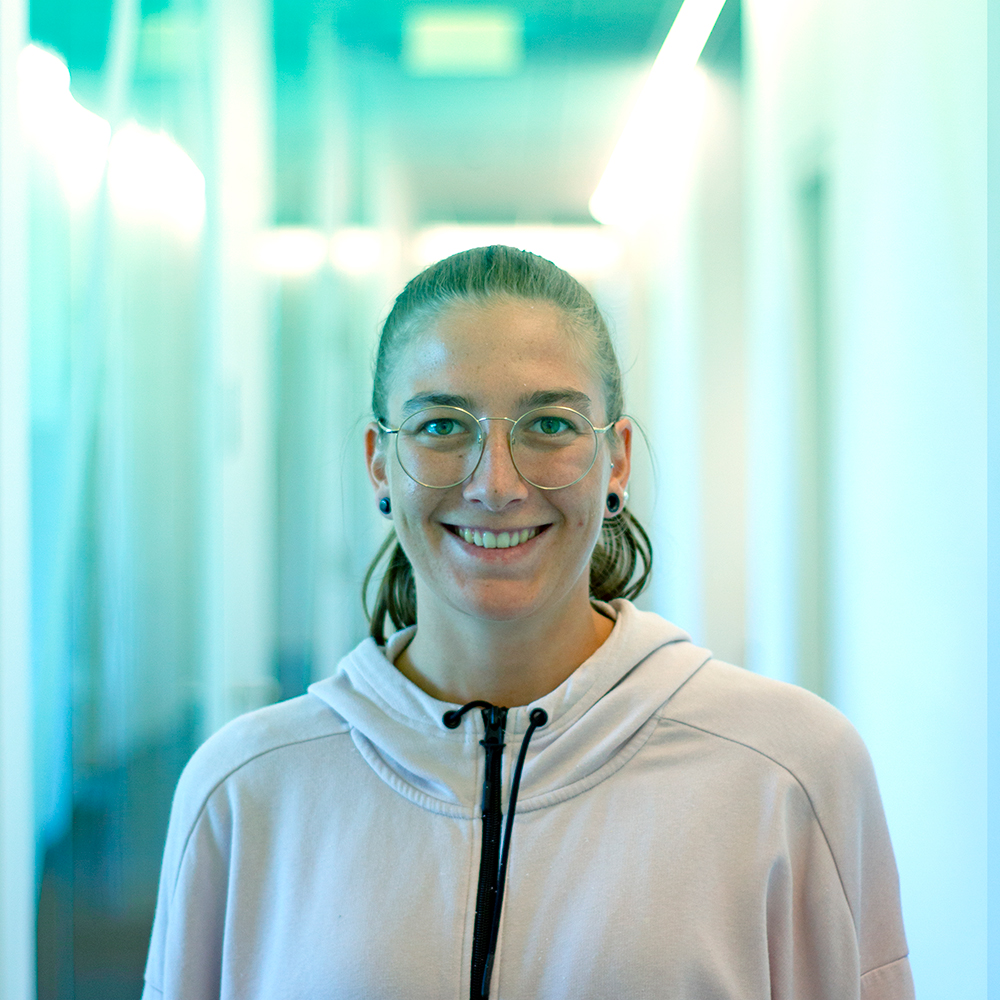
Julia Webinger
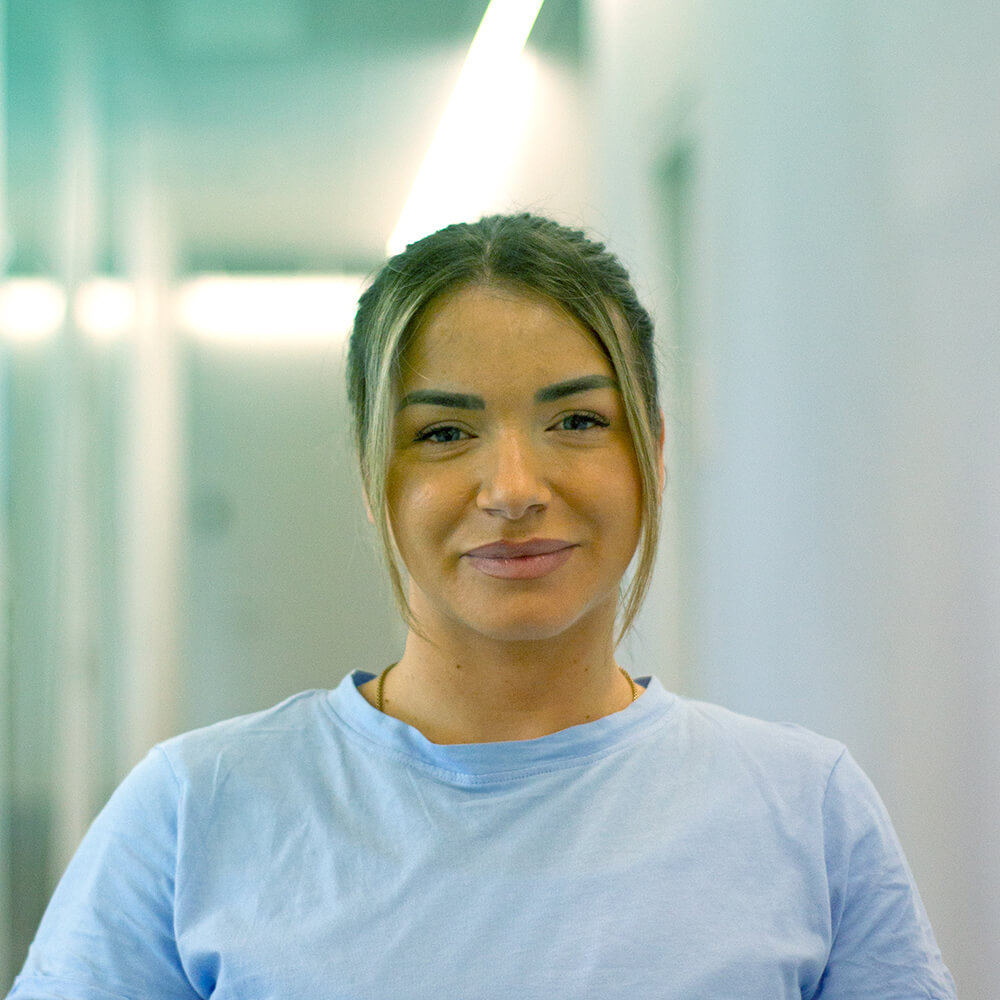
Ardita Avdyli
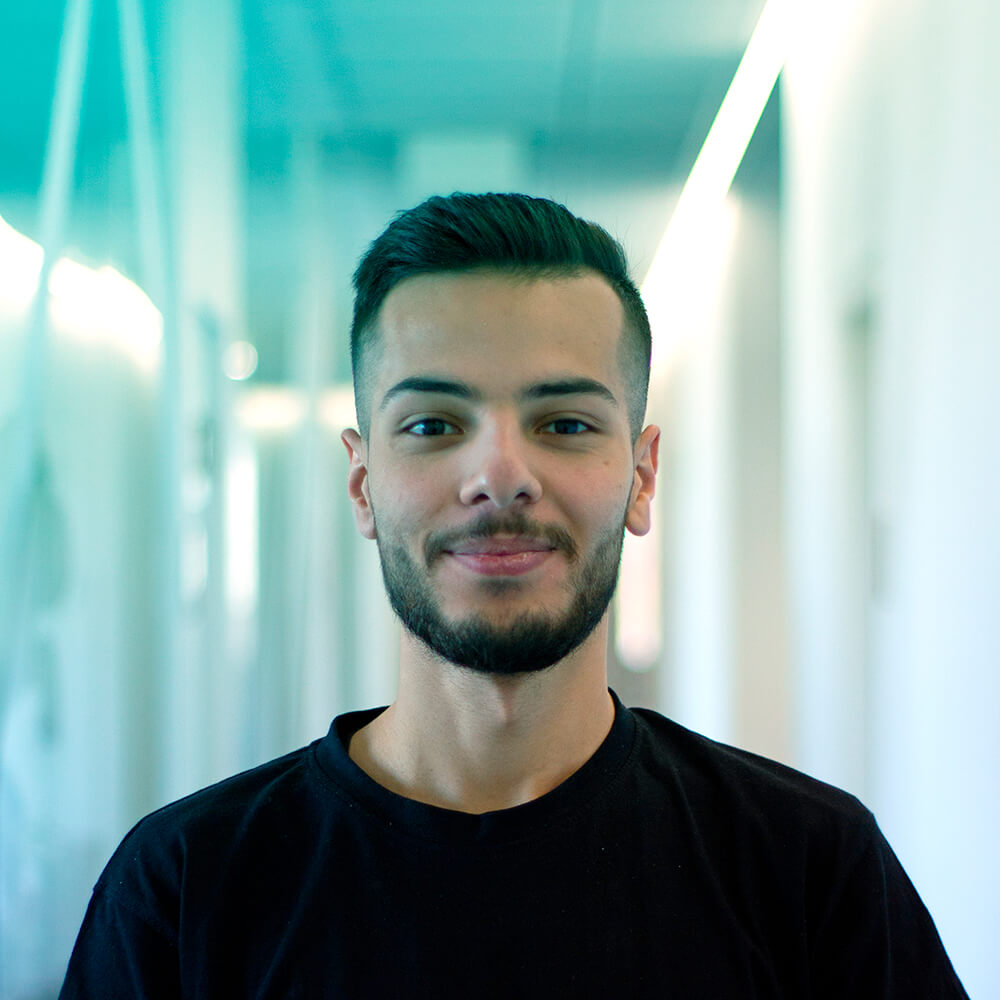
Mazen_Alubadi
Description:
The apprenticeship as a dental technician lasts 4 years. The vocational school is based in Baden near Vienna and is attended in blocks of 10 weeks per year. The training to become a dental technician is varied and the apprentices should be able to learn and implement all specialist areas of dental technology. During the apprenticeship, most of the apprentices find out which specialist area they have a knack for. Initially, the apprentices are busy learning the art of making models correctly; At the same time, bite registrations and individual impression trays are made. Over time, repairs are added, at the beginning slight such as breaks or cracks, over time the repairs become more demanding. After completing the first class of the vocational school, the apprentices are trained in the field of prosthetics. In the 3rd and 4th year of the apprenticeship, the apprentices are made familiar with model casting, total prosthetics and crown and bridge technology so that everything fits and no major mistakes are made when they finish their apprenticeship.
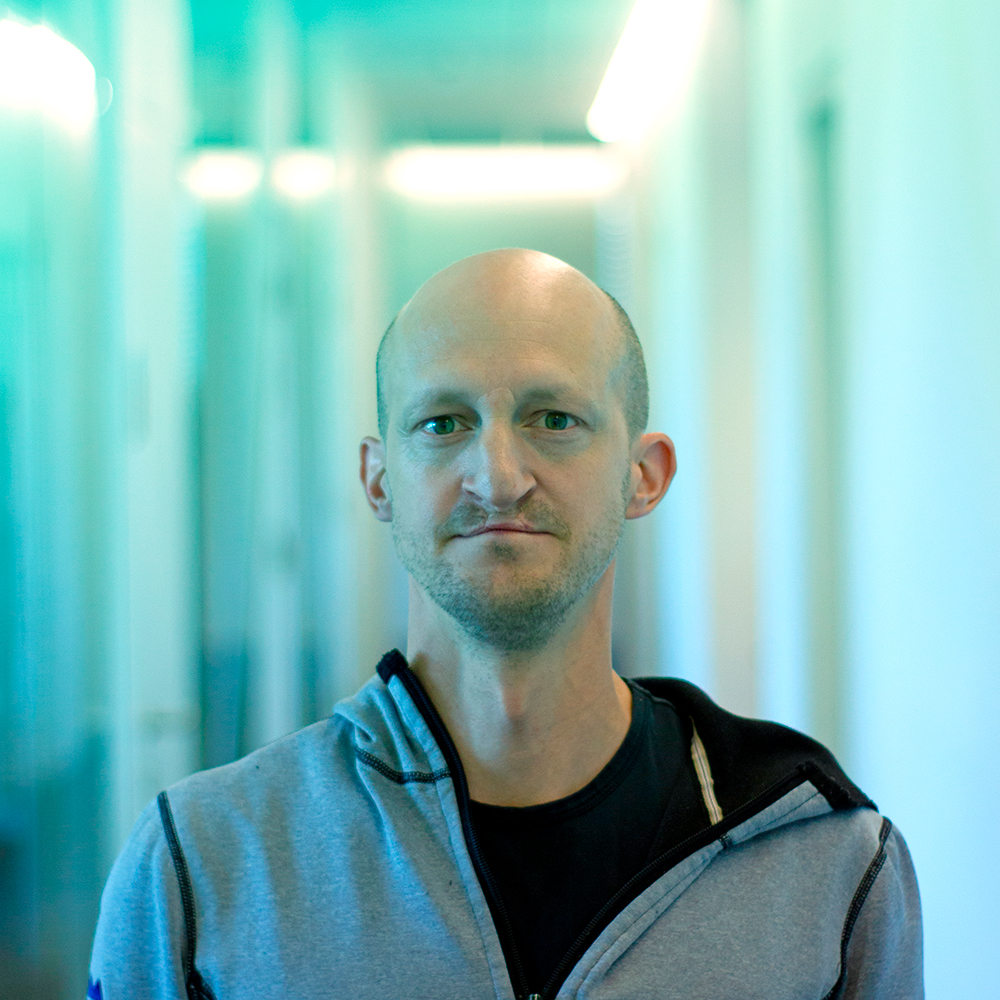
Roman Wechselberger
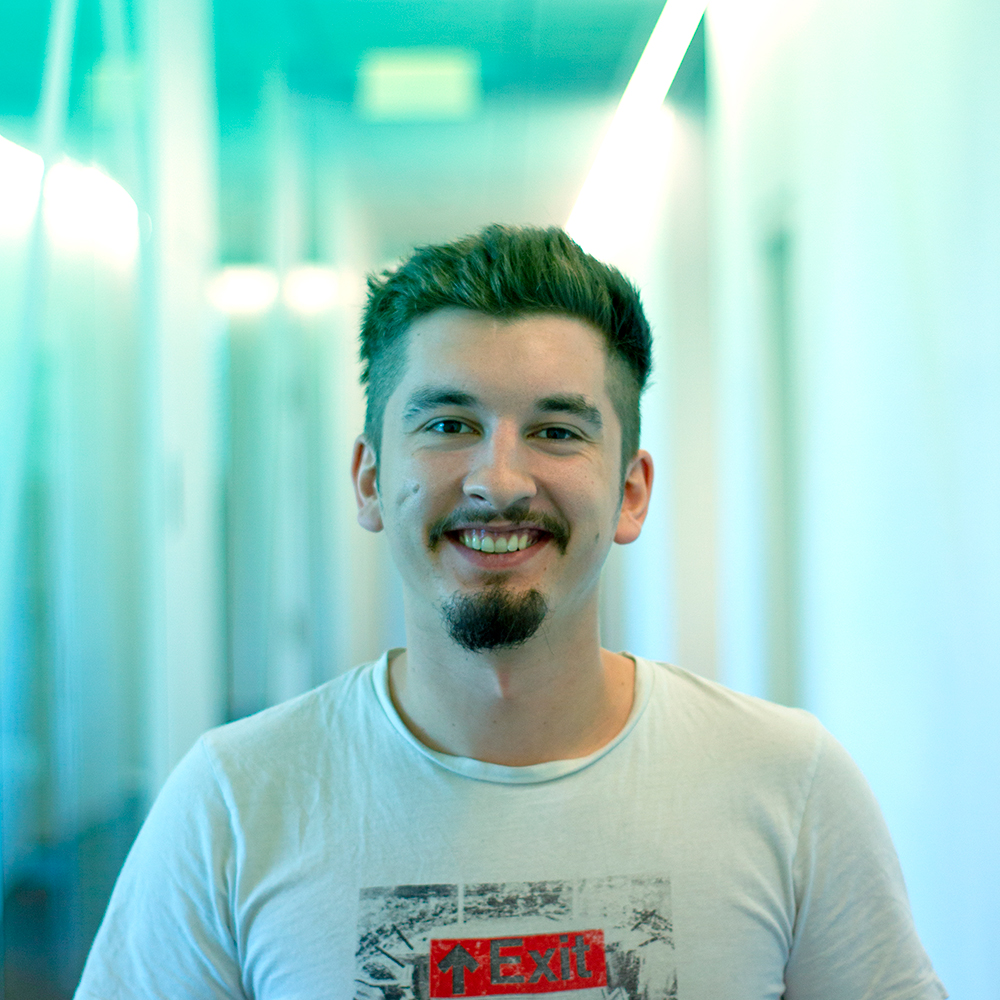
Alexandar Milosevic
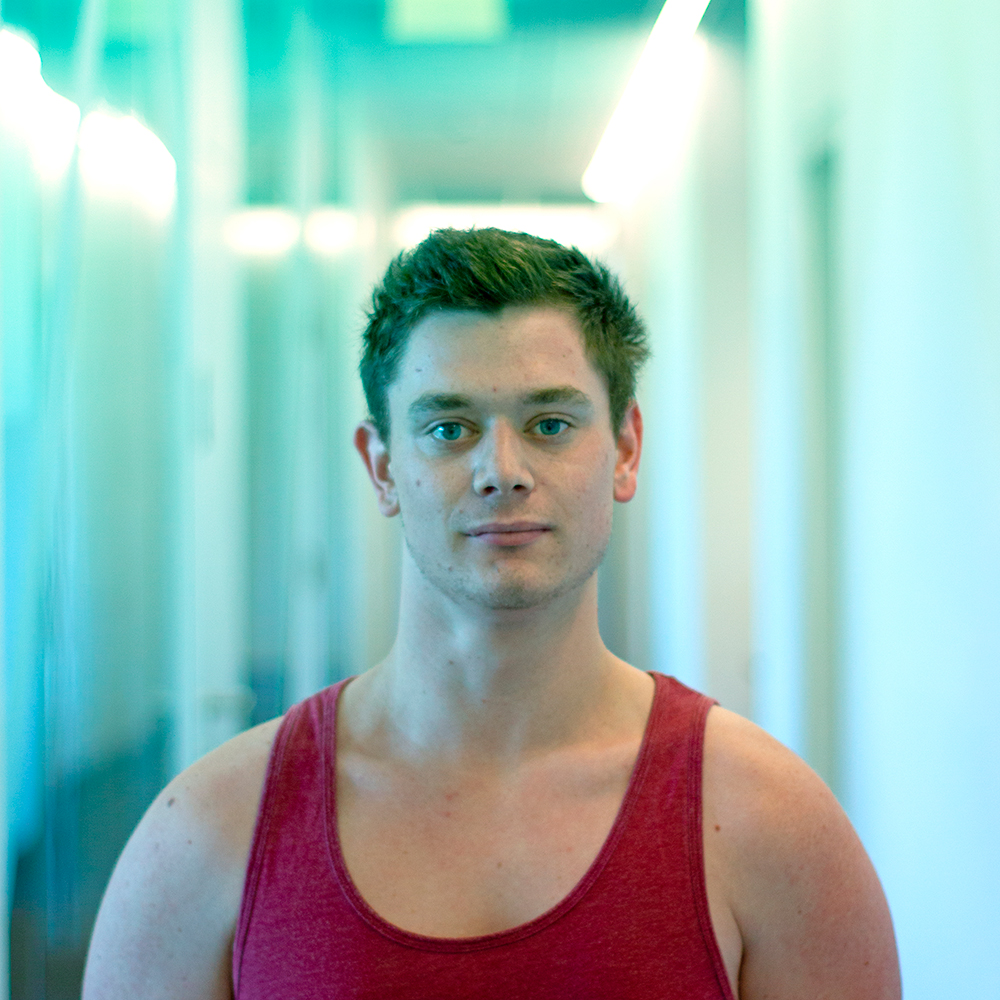
Marco Prommegger
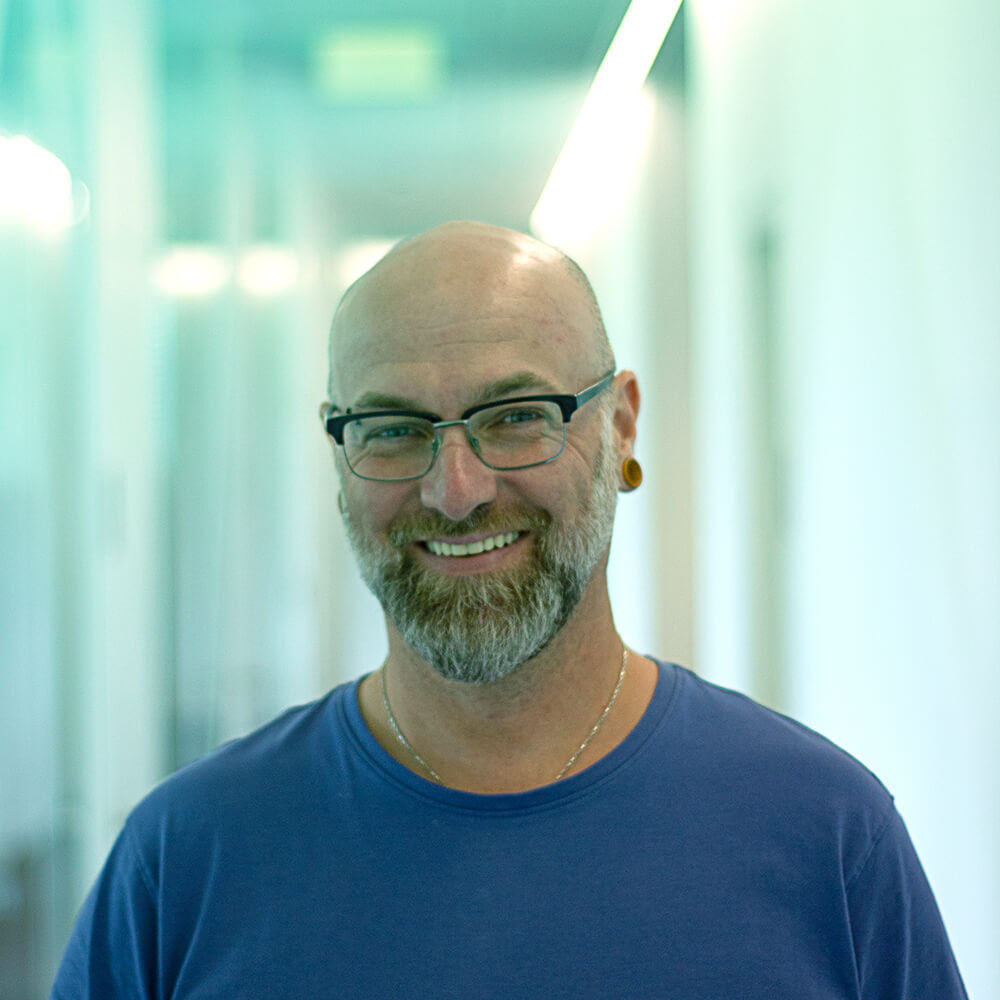
Thomas_Hauser
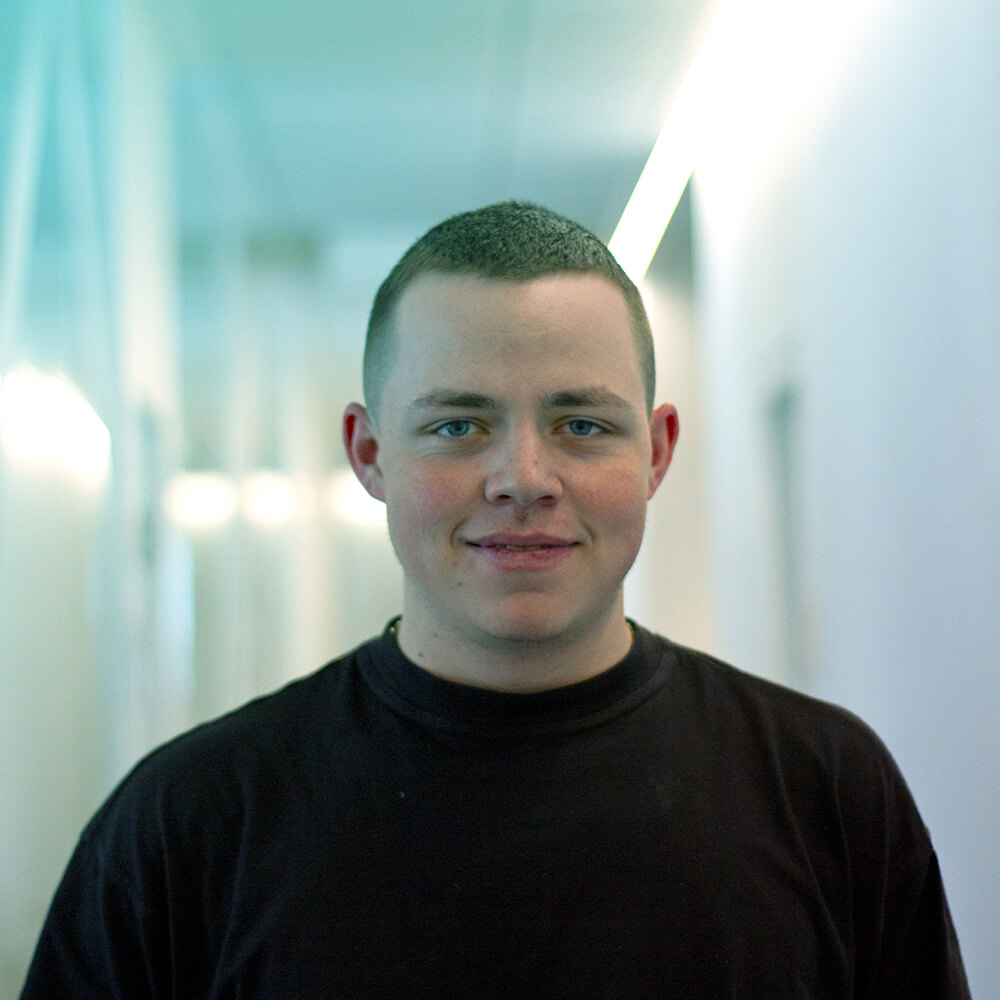
Ziegler_Johannes
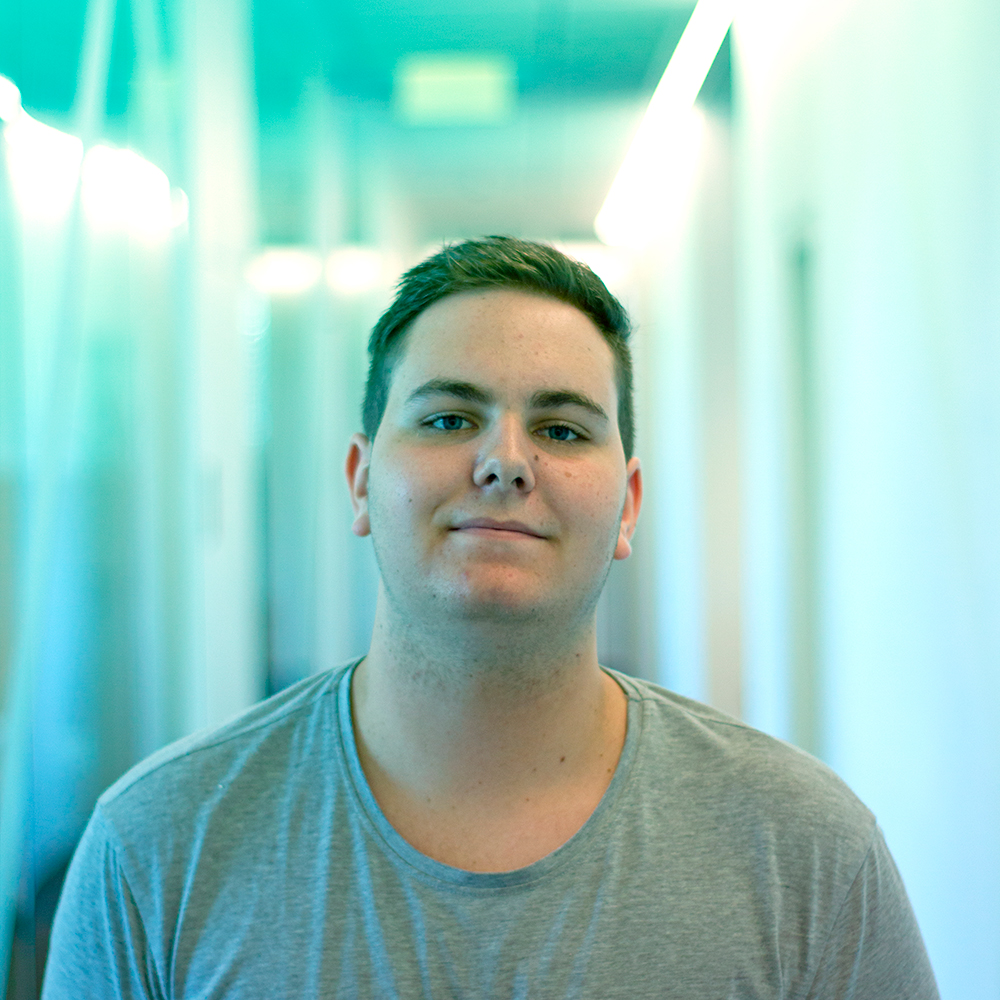
Simon_Hammer
Description:
In order to be able to make a model casting, you need a master model. The model is measured with the help of a parallelometer in order to correctly mark the required brackets. After the measurement has been completed, the model is duplicated with silicone and an investment model is made afterwards. The model casting is modeled on the investment model with wax parts and provided with casting channels. This is followed by investing with investment material to create a casting muffle, the muffle is heated in the preheating furnace to 950 ° C and, once the temperature has been reached, it is cast using frequency centrifugal casting. After the casting muffle has cooled down, the finishing and polishing of the model casting begins.
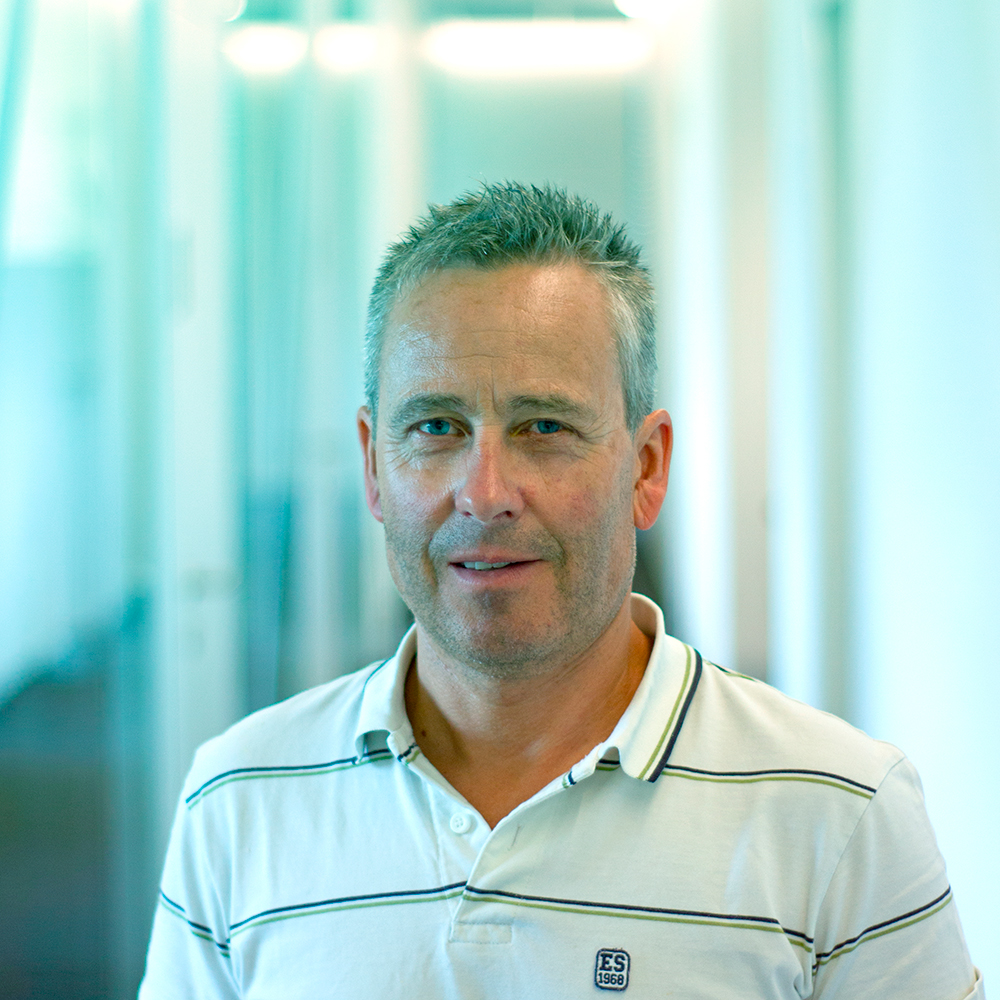
Helmut_Zaller
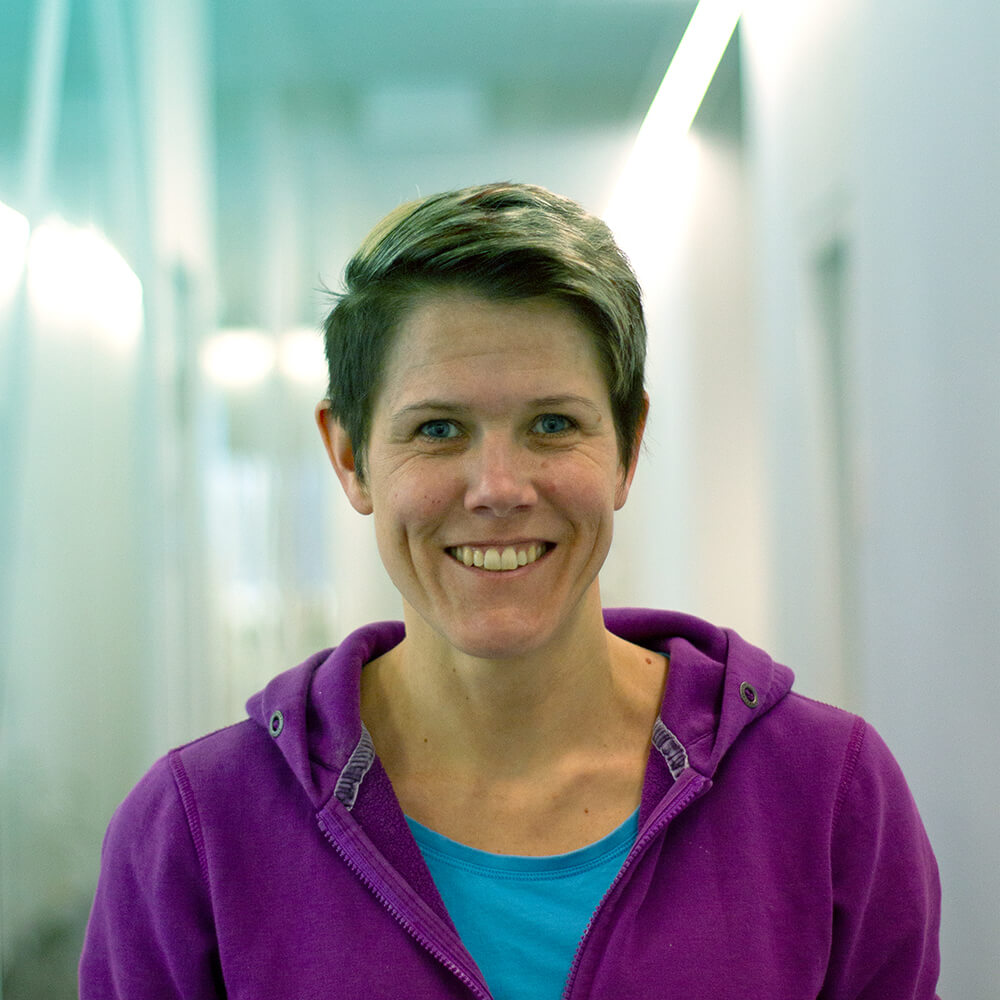
Ingrid David

Strasser Katharina
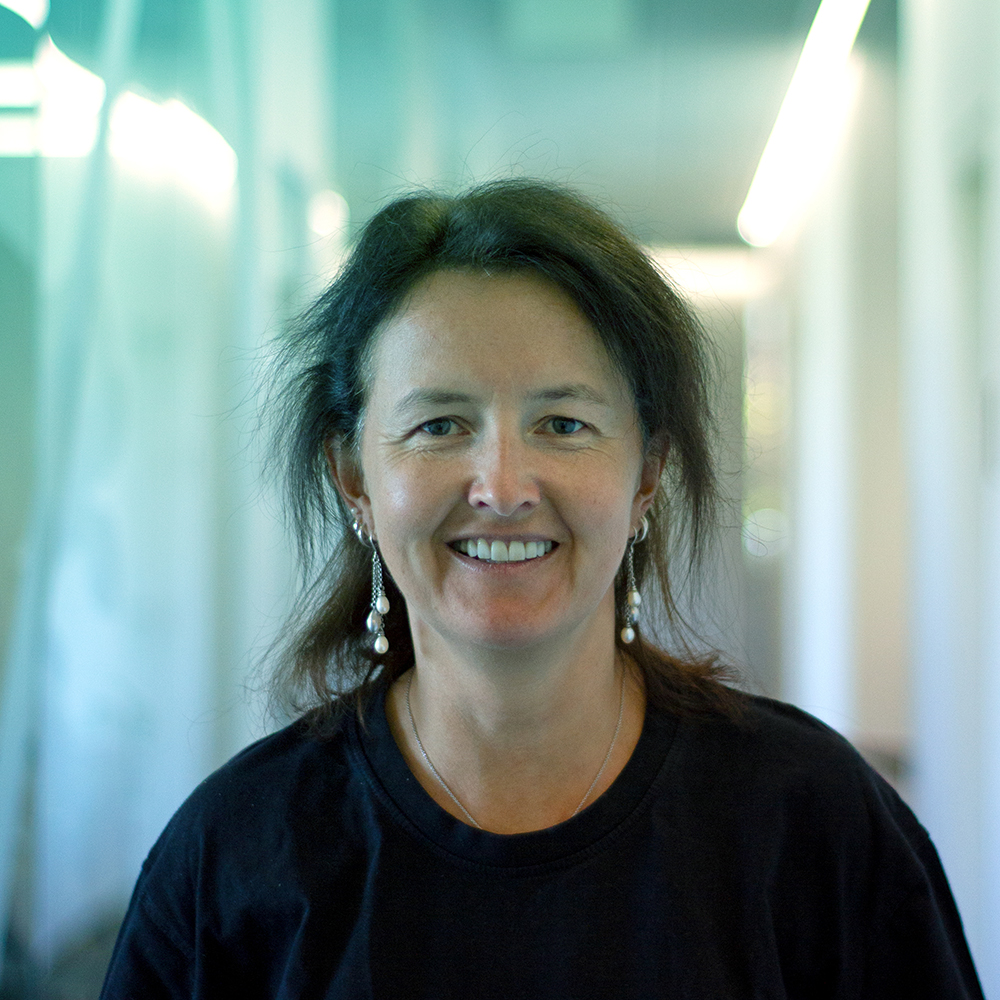
Ofensberger-Hildegard
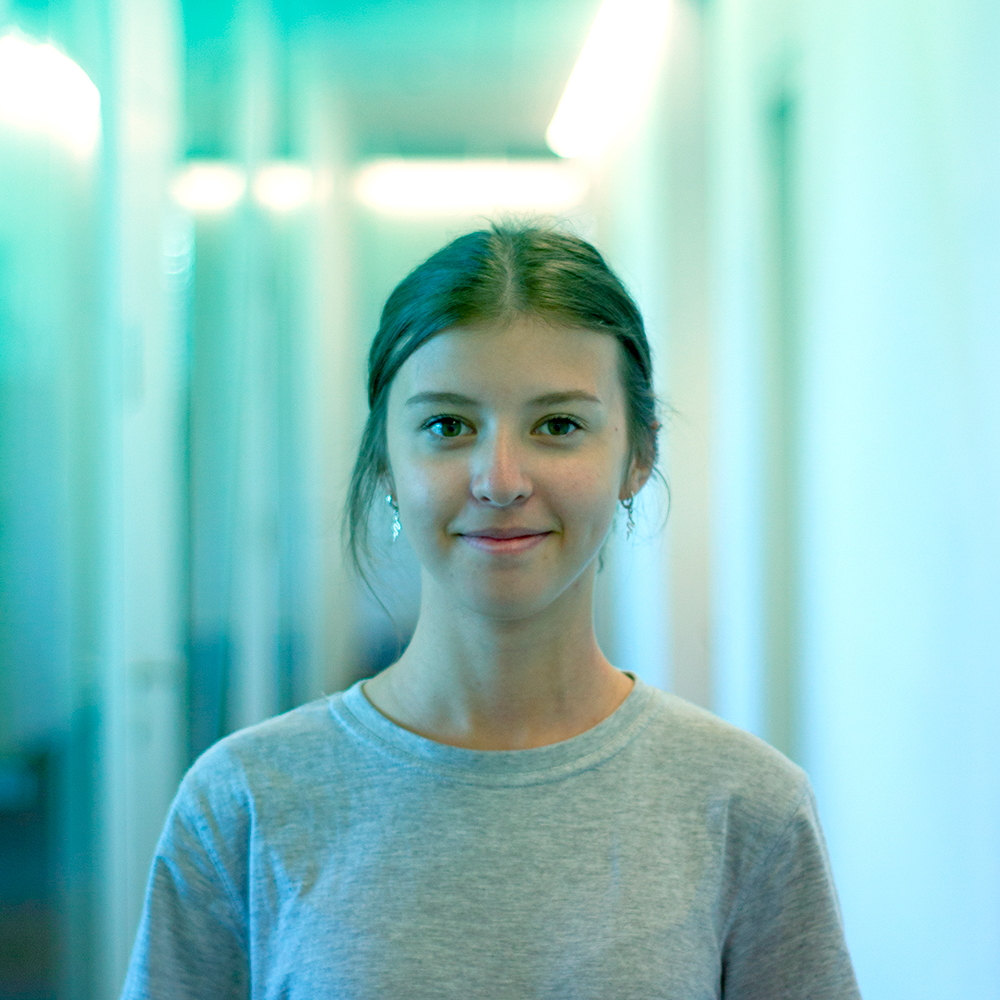
Vesna_Bjelic
Portfolio
3D-Scanners
—
Our scanners combine sophisticated technology and uncompromising efficiency.
Milling
—
We operate the largest and most modern milling center in Austria to support dental laboratories with minimal investment and maximum performance.
Prosthetic Parts
—
The quality of our prosthetic parts is checked by independent institutes and confirmed by our existing quality certificates.
Orthodontics
—
CADstar offers user-friendly aligner therapies and has adapted its 3D scanners to all the requirements of daily digital orthodontics.
WeCare
Resources are valuable. Both “natural” and human.
We have decided to start the WeCare initiative because we want to use our resources more responsibly in the future. This is not only about the basic materials that we need for our work, but also about every employee as a valuable building block for growing together.
Take and give – is an essential guiding principle. To appreciate the value of the “small” in order to strengthen the “big”. Together, we will do it!
To thank you for your commitment, an amount of € 1.50 – € 3.50 is contributed with each meal.
You can save up to € 400 per year, because lunch costs each employee only € 3.00 per day / meal. The costs of around € 9,000.00 per year are worth it to us, because only together are we strong.
anonymously, easily and quickly
In order to offer you an anonymous, simple and fast way to communicate your wishes, concerns and improvement possibilities to us, we have set up an “online” suggestion box. This can be used absolutely anonymously but also with a name. We do our best to address your concerns as well as possible.
In order to create equal rights for everyone, we have a so-called voluntary actual wage increase.
In January 2020 there was an increase in the actual wages of 2.5% in the collective agreement with the metalworking industry, but only for employees in this collective. Commerce and general industry do not provide for this increase, maintenance or overpayment. However, in order to offer everyone the same rights, this increase is rolled out to all employees every year.
For some it is essential to life and for others it is a luxury item.
It’s about the coffee. Most of us enjoy a good coffee, especially in the morning. And we’re happy that we don’t have to pay anything for it. Since we are not that few people anymore, the annual costs for 94kg of coffee with milk and sugar amount to almost € 2,700, – We think it’s worth applauding.
Not a single light bulb was installed in the new company building
Approx. 435 LED lights, approx. 75 LED emergency lights and approx. 350m LED strips were installed in our new company building. In contrast to conventional lighting means, an LED has an approx. 40 times longer service life, approx. 98% of the total consumption is used for light generation and the raw materials contained can be reused very easily. Another step in the right direction to deal more consciously with raw materials!
We try to convert all types of printing to environmental or recycled paper
We have decided to convert our printed matter to environmentally friendly materials as far as possible. The “PEFC” and “FSC” certificates guarantee careful handling of the flora and fauna on site, fair conditions for their employees and the seamless tracing of the products back to their origin. We also ask that you use printouts responsibly. Thanks very much.
We recycle the heat in the new company building
Since the winter in our part of the world is cooler, heating should of course not be missing. However, we do not heat, we let heat. We use the waste heat from our machines to keep our entire company building warm. In this way, we not only save heating costs, but also do not use any additional energy.
A good start to the day is essential
To start the day relaxed, we work flexitime here. It is therefore possible to do the work between 6:00 a.m. and 8:00 p.m., provided the activity allows it. The core times are from 9 a.m. to 3 p.m. This means that everyone has enough time to take the children to school or simply to sleep in. Those who start the day relaxed have more of it.
We recycle used raw materials
By recycling consumables and not throwing them away, we save costs and raw materials and thus create another source of income.
Attention camera
For security reasons we have been using surveillance cameras for a short time. To protect your privacy, we have made the areas where workplaces are unrecognizable.
We build on your knowledge
It is important to us that you are always up to date and that you can expand your knowledge. That is why we are happy to cover your training costs. We all benefit from it.